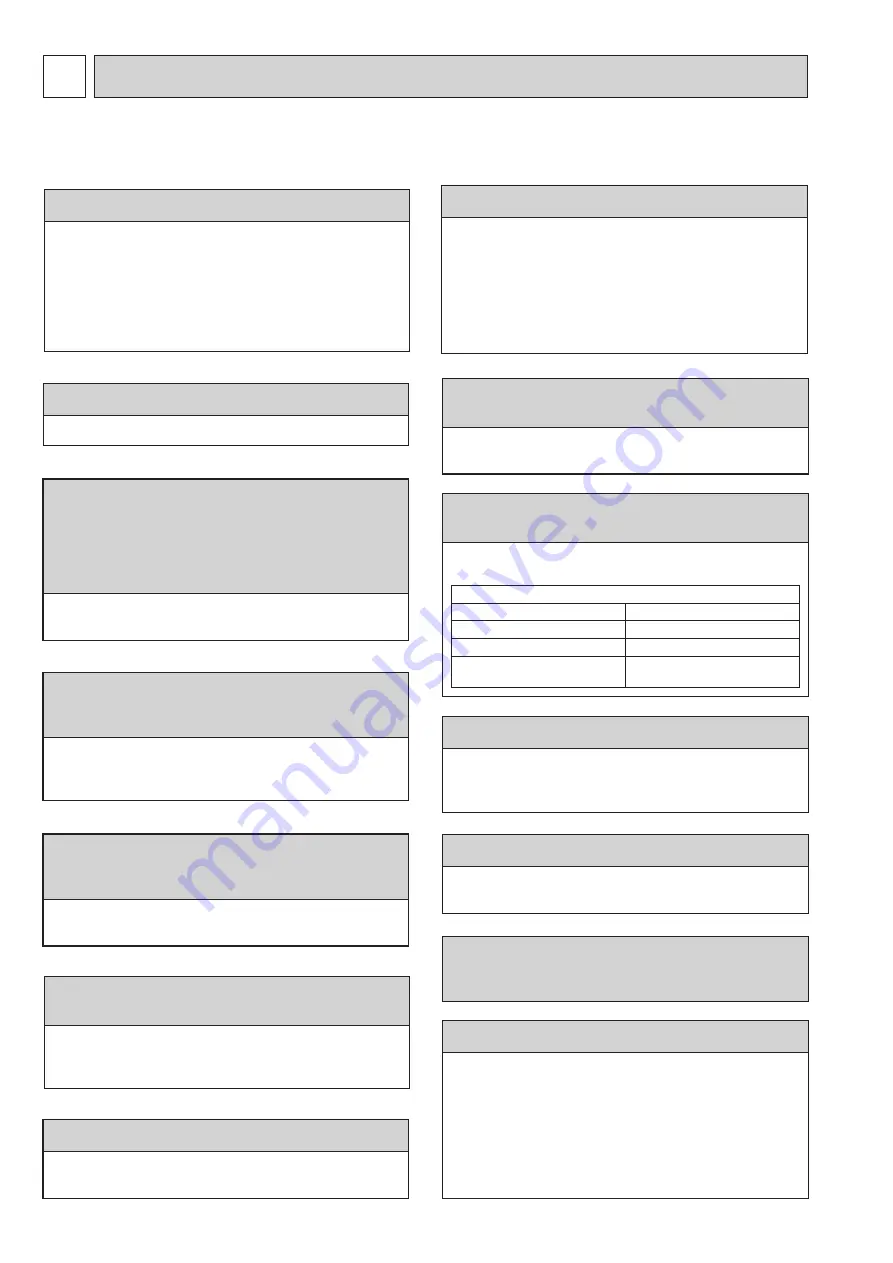
2
OCH744
1
SAFETY PRECAUTION
Cautions for units utilizing refrigerant R410A
1-1. CAUTIONS RELATED TO NEW REFRIGERANT
Use new refrigerant pipes.
Avoid using thin pipes.
Use a vacuum pump with a reverse flow check
valve.
Vacuum pump oil may flow back into refrigerant cycle and
that can cause deterioration of refrigerant oil, etc.
Handle tools with care.
If dirt, dust or moisture enters into refrigerant cycle, that
can cause deterioration of refrigerant oil or malfunction of
compressor.
Do not use a charging cylinder.
If a charging cylinder is used, the composition of refrigera-
nt will change and the efficiency will be lowered.
Use the specified refrigerant only.
Never use any refrigerant other than that specified.
Doing so may cause a burst, an explosion, or fire when
the unit is being used, serviced, or disposed of.
Correct refrigerant is specified in the manuals and on the
spec labels provided with our products.
We will not be held responsible for mechanical failure,
system malfunction, unit breakdown or accidents caused
by failure to follow the instructions.
Ventilate the room if refrigerant leaks during
operation. If refrigerant comes into contact with
a flame, poisonous gases will be released.
Use the following tools specifically designed for
use with R410A refrigerant.
The following tools are necessary to use R410A
refrigerant.
Tools for R410A
Gauge manifold
Flare tool
Charge hose
Size adjustment gauge
Gas leak detector
Vacuum pump adaptor
Torque wrench
Electronic refrigerant
charging scale
Make sure that the inside and outside of refrige-
rant piping is clean and it has no contaminants
such as sulfur, oxides, dirt, shaving particles,
etc.,
which are hazard to refrigerant cycle.
In addition, use pipes with specified thickness.
Contamination inside refrigerant piping can cause deterio-
ration of refrigerant oil, etc.
Store the piping indoors, and keep both ends of
the piping sealed until just before brazing.
(Leave elbow joints, etc. in their packaging.)
If dirt, dust or moisture enters into refrigerant cycle, that
can cause deterioration of refrigerant oil or malfunction of
compressor.
The refrigerant oil applied to flare and flange
connections must be ester oil, ether oil or
alkylbenzene oil in a small amount.
If large amount of mineral oil enters, that can cause
deterioration of refrigerant oil, etc.
Charge refrigerant from liquid phase of gas
cylinder.
If the refrigerant is charged from gas phase, composition
change may occur in refrigerant and the efficiency will be
lowered.
Do not use refrigerant other than R410A.
If other refrigerant (R22, etc.) is used, chlorine in refrige-
rant can cause deterioration of refrigerant oil, etc.
Precautions during the repair service
• Do not perform the work involving the electric parts
with wet hands.
• Do not pour water into the electric parts.
• Do not touch the refrigerant.
• Do not touch the hot or cold areas in the refrigerating cycle.
• When the repair or the inspection of the circuit needs
to be done without turning off the power, exercise great
caution not to touch the live parts.
Preparation before the repair service
• Prepare the proper tools.
• Prepare the proper protectors.
• Provide adequate ventilation.
• After stopping the operation of the air conditioner, turn
off the power-supply breaker.
• Discharge the condenser before the work involving the
electric parts.
Содержание PAC-MK34BC
Страница 27: ...27 OCH744 ...