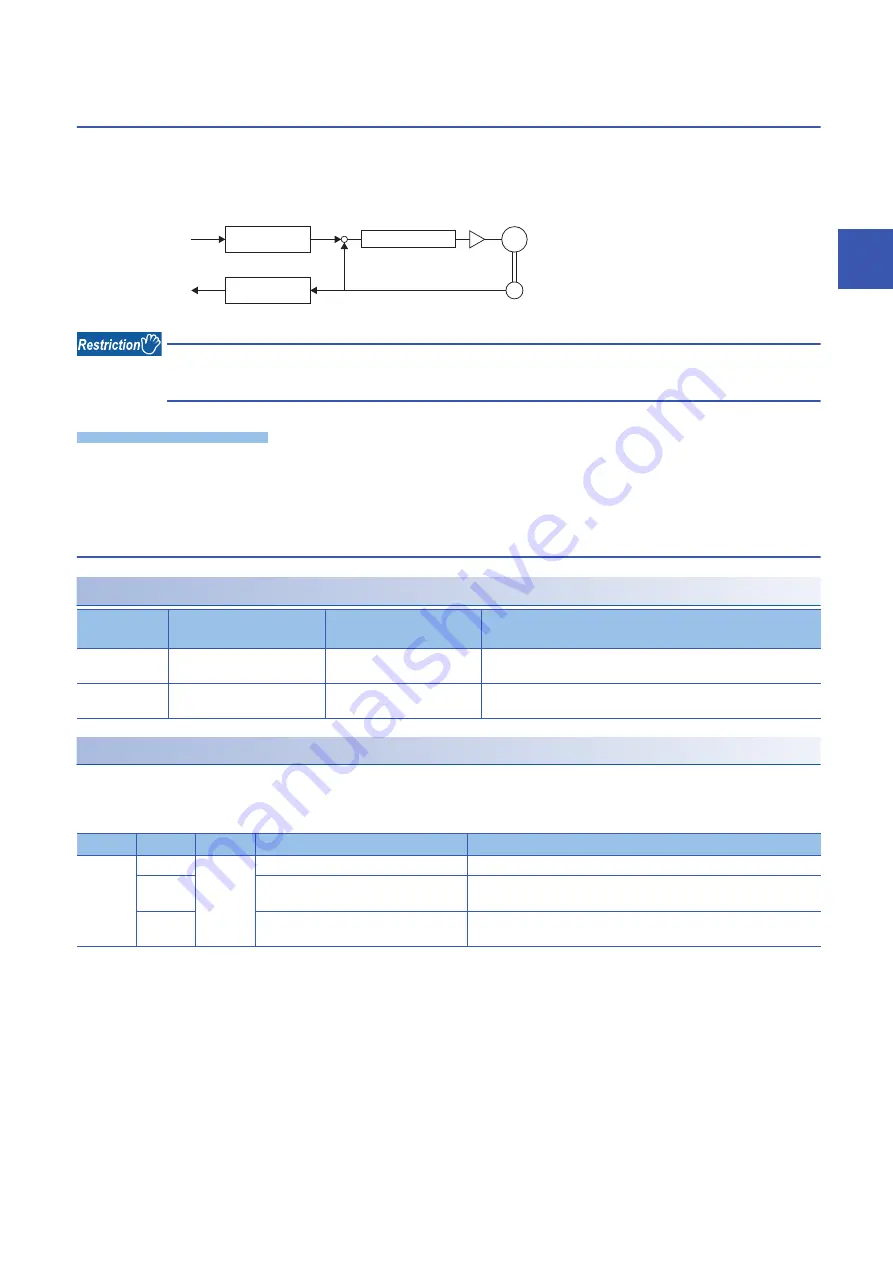
3 BASIC FUNCTION
3.6 Electronic gear function
77
3
3.6
Electronic gear function
Electronic gear function is a function that multiplies the electronic gear ratio to the position command, and sets the ratio of the
rotation amount/travel distance of the servo motor to the rotation amount/travel distance of the command unit as desired. For
the position feedback, the inverse number of the electronic gear ratio is multiplied.
• Set the electronic gear within the range of conditions. If a value out of the range is set, [AL. 037 Parameter
error] occurs.
Precautions
• To prevent unexpected operation, set the electronic gear correctly.
• If an excessive command pulse frequency is inputted from the controller in the cyclic synchronous position mode, [AL. 031
Overspeed] or [AL. 035 Command frequency error] may occur, depending on the value of the electronic gear ratio.
Setting method
Setting with servo parameters
Setting with object dictionary
Set the electronic gear numerator for [Motor revolutions (Obj. 6091h: 01h)], and electronic gear denominator for [Shaft
revolutions (Obj. 6091h: 02h)].
For details on the objects, refer to the User's Manual (Object Dictionary).
Servo
parameter
Symbol
Name
Outline
PA06
CMX
Electronic gear - Numerator
Set the electronic gear numerator.
Initial value: 1
PA07
CDV
Electronic gear - Denominator
Set the electronic gear denominator.
Initial value: 1
Index
Sub
Object
Name
Description
6091h
0
ARRAY
Gear ratio
Gear ratio
1
Motor revolutions
Number of revolutions of the servo motor shaft (numerator)
This corresponds to [Pr. PA06].
2
Shaft revolutions
Number of revolutions of the drive shaft (denominator)
This corresponds to [Pr. PA07].
+
-
M
Servo motor
Position command
[Command unit]
Electronic gear
conversion
Deviation counter
Position feedback
[Command unit]
Electronic gear
reverse conversion
Encoder
Содержание MELSERVO-JET MR-JET-G-N1 Series
Страница 1: ...MR JET User s Manual Function MR JET _G MR JET _G N1 Mitsubishi Electric AC Servo System ...
Страница 2: ......
Страница 161: ......