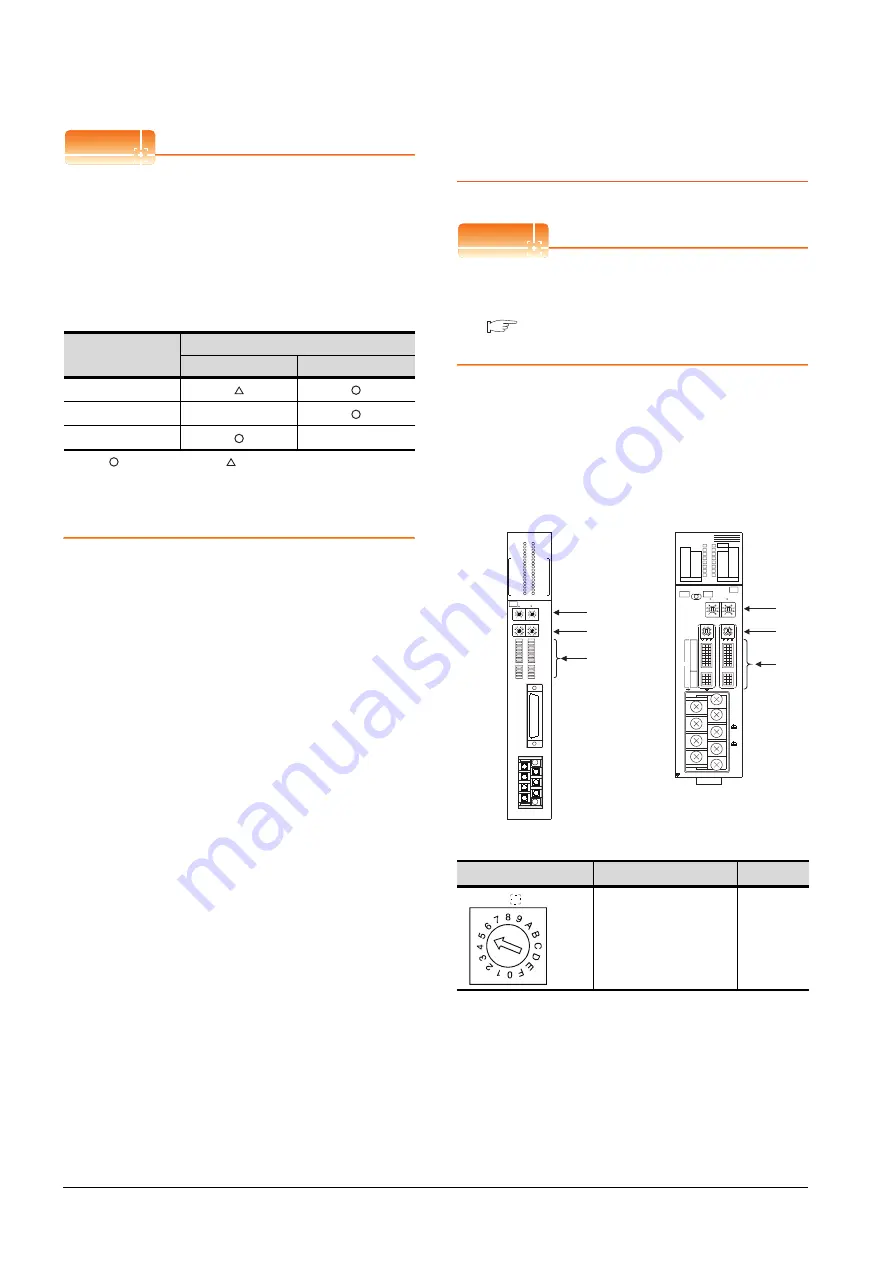
7 - 26
7. COMPUTER LINK CONNECTION
7.5 PLC Side Setting
POINT
POINT
POINT
(1) When the [intelligent function module switch
setting] has been set
After writing PLC parameters to the PLC CPU,
turn the PLC CPU OFF then back ON again, or
reset the PLC CPU.
(2) Connection of multiple GOTs
To some serial communication module models,
two GOTs can be connected using both CH1 and
CH2.
: 2 GOTs connectable, : 1 GOT connectable, -: Not applicable
(3) When connecting to the modem interface module
When the modem interface module is connected,
only CH2 can be used.
7.5.3
Connecting serial
communication module (QnA
Series)
POINT
POINT
POINT
Serial communication module (QnA Series)
For details of the serial communication module (QnA
Series), refer to the following manual.
Serial Communication Module User's Manual
(Modem Function Additional Version)
Switch setting on serial communication
module
Set the Station number switches, the Mode setting
switch for the channel used for GOT connection, and
the Transmission specifications switches.
(1) Mode setting switch
*1
The mode switch in the figure is for the AJ71QC24 (N) (-R2/
R4).
Model
Connection of 2 GOTs
Function version A
Function version B
QJ71C24(-R2)
QJ71C24N(-R2/R4)
-
LJ71C24(-R2)
-
Mode setting switch
*1
Description
Set value
Dedicated protocol (Format 5)
(Binary mode)
5
A
J71QC24N
RUN
CPUR/W
NEU
ACK
NAK
C/N
P/S
PRO
SIO
SD.WAIT
SD
RD
CH1.ERR.
CH2.ERR.
NEU
ACK
NAK
C/N
P/S
PRO
SIO
SD.WAIT
SD
RD
CH.1
CH.2
1
CH1
CH2
STATION
No.
MODE
SW
01
02
03
04
05
06
07
08
09
10
11
12
RDA
RDB
SG
SDA
SDB
NC
FG
CH1
RS-232C
CH2
RS422
RS485
8
4
0
C
8
4
0
C
5
0
5
0
10
AJ71QC24N, AJ71QC24N-R2,
AJ71QC24N-R4,AJ71QC24,
AJ71QC24-R2, AJ71QC24-R4
(3)
(1)
(2)
A
1SJ71QC24N
CH1
ERR.
C/N
P/S
PRO
SID
CH2
ERROR
RD
SW.E
NEU
ACK
NAK
SD.W.
SD
STS
ERR.
DISPLAY
5
0
5
0
CH1
CH2
10
1
STATION NO.
MODE
A1SJ71QC24N
RUN
RD
C.R/W
NEU
ACK
NAK
SD.W.
SD
ERR.
C/N
P/S
PRO
SIO
AB
CH1 RS-232-C
CH2 RS-422/RS-485
SG
(FG)
(NC)
SDA
SDB
RDA
RDB
8
4
0
C
8
4
0
C
ON
2
1
4
3
6
5
8
7
10
9
12
11
SW
(1)
(3)
(2)
A1SJ71QC24N1, A1SJ71QC24N1-R2
A1SJ71QC24N, A1SJ71QC24N-R2,
A1SJ71QC24, A1SJ71QC24-R2
MODE
CH
Содержание GT15
Страница 2: ......
Страница 34: ...A 32 ...
Страница 92: ......
Страница 110: ...2 18 2 DEVICE RANGE THAT CAN BE SET 2 9 MELSEC WS ...
Страница 134: ...3 24 3 ACCESS RANGE FOR MONITORING 3 7 Connection to the Head Module of CC Link IE Field Network System ...
Страница 186: ...5 10 5 BUS CONNECTION 5 2 System Configuration ...
Страница 218: ...5 42 5 BUS CONNECTION 5 4 Precautions ...
Страница 254: ...6 36 6 DIRECT CONNECTION TO CPU 6 6 Precautions ...
Страница 286: ...7 32 7 COMPUTER LINK CONNECTION 7 6 Precautions ...
Страница 350: ...8 64 8 ETHERNET CONNECTION 8 5 Precautions ...
Страница 368: ...9 18 9 MELSECNET H CONNECTION PLC TO PLC NETWORK 9 5 Precautions ...
Страница 420: ...11 26 11 CC Link IE CONTROLLER NETWORK CONNECTION 11 5 Precautions ...
Страница 440: ...12 20 12 CC Link IE FIELD NETWORK CONNECTION 12 5 Precautions ...
Страница 490: ...13 50 13 CC Link CONNECTION INTELLIGENT DEVICE STATION 13 5 Precautions ...
Страница 510: ......
Страница 564: ...15 54 15 INVERTER CONNECTION 15 7 Precautions ...
Страница 668: ......
Страница 712: ...21 12 21 MULTIPLE GT14 GT12 GT11 GT10 CONNECTION FUNCTION 21 5 Precautions ...
Страница 713: ...MULTI CHANNEL FUNCTION 22 MULTI CHANNEL FUNCTION 22 1 ...
Страница 714: ......
Страница 760: ...22 46 22 MULTI CHANNEL FUNCTION 22 5 Multi channel Function Check Sheet ...
Страница 761: ...FA TRANSPARENT FUNCTION 23 FA TRANSPARENT FUNCTION 23 1 ...
Страница 762: ......
Страница 860: ...REVISIONS 4 ...
Страница 863: ......