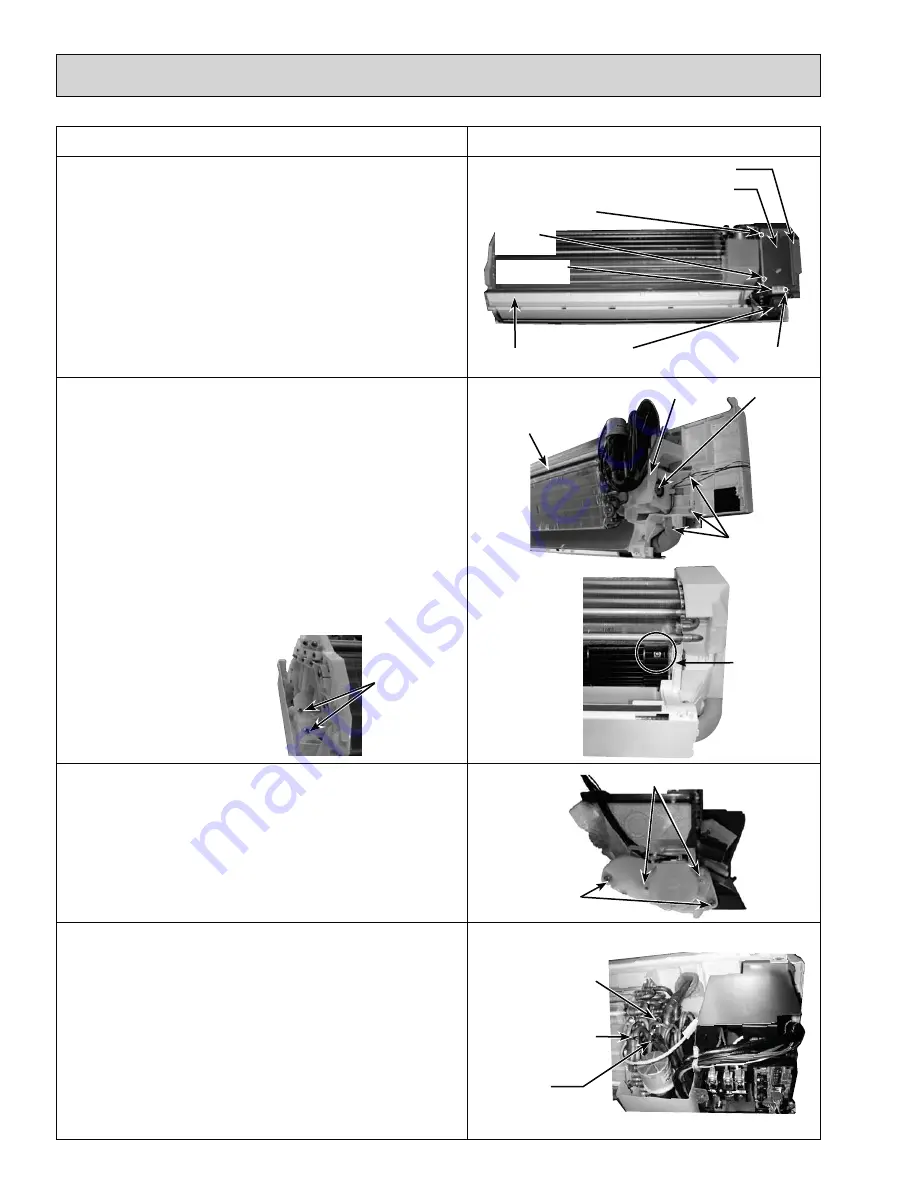
PHOTOS
OPERATION PROCEDURE
24
5. REMOVING THE NOZZLE ASSEMBLY (with VANE
and VANE MOTOR) AND DRAIN HOSE
(1) Remove the front panel (Refer to procedure 2).
(2) Remove the electrical box cover.
(3) Disconnect the vane motor connector (CN151) on the
indoor controller board.
(4) Remove the corner box.
(5) Pull the nozzle assembly and detach.
(6) Push the fixture and remove the drain hose.
6. REMOVING THE INDOOR FAN MOTOR AND THE
LINE FLOW FAN
(1) Remove the front panel (Refer to procedure 2) and the
corner box at right lower side.
(2) Remove the electrical box (Refer to procedure 4) and the
nozzle assembly (Refer to procedure 5).
(3) Remove the screws fixing the motor bed. (See Photo 8)
(4) Loosen the screw fixing the line flow fan. (See Photo 9)
(5) Remove the motor bed together with fan motor and motor band.
(6) Release the hooks of the motor band. Remove the motor
band. Pull out the indoor fan motor.
(7) Remove the screws fixing the left side of the heat exchanger.
(See Photo 10)
(8) Lift the heat exchanger, and pull out the line flow fan to the
lower-left.
Photo 8
Photo 9
7. REMOVING THE VANE MOTOR
(1) Remove the nozzle assembly. (Refer to procedure 5)
(2) Remove the screws of the vane motor unit, and pull out
the vane motor unit.
(3) Remove the screws of the vane motor unit cover.
(4) Remove the vane motor from the vane motor unit.
(5) Disconnect the connector from the vane motor.
8. REMOVING THE LIQUID PIPE THERMISTOR AND
GAS PIPE THERMISTOR
(1) Remove the front panel. (Refer to procedure 2)
(2) Remove the electrical box cover.
(3) Remove the motor band.
(4) Cut the wiring fixed band.
(5) Remove the liquid pipe thermistor and gas pipe thermistors.
(6) Disconnect the connector (CN44) (CN2G) on the indoor
controller board. (TH22 and TH23/CN44, TH24/CN2G)
Photo 12
Gas pipe thermistor
(TH24)
Liquid pipe
thermistor (TH22)
Photo 7
Screw of the
line flow fan
Photo 10
Screw of the
left side of the
heat exchanger
Gas pipe thermistor
(TH23)
Electrical box cover (top)
Electrical box cover (side)
Screw (side cover)
Screw
(top cover)
Switch board
cover
Holder of wireless
controller board
Nozzle assembly
Screws of the vane motor unit
Screws of the vane
motor unit cover
Photo 11
Screw
(side cover)
Screw of the
motor bed
Heat exchanger
Fan motor
Motor band
OCH515