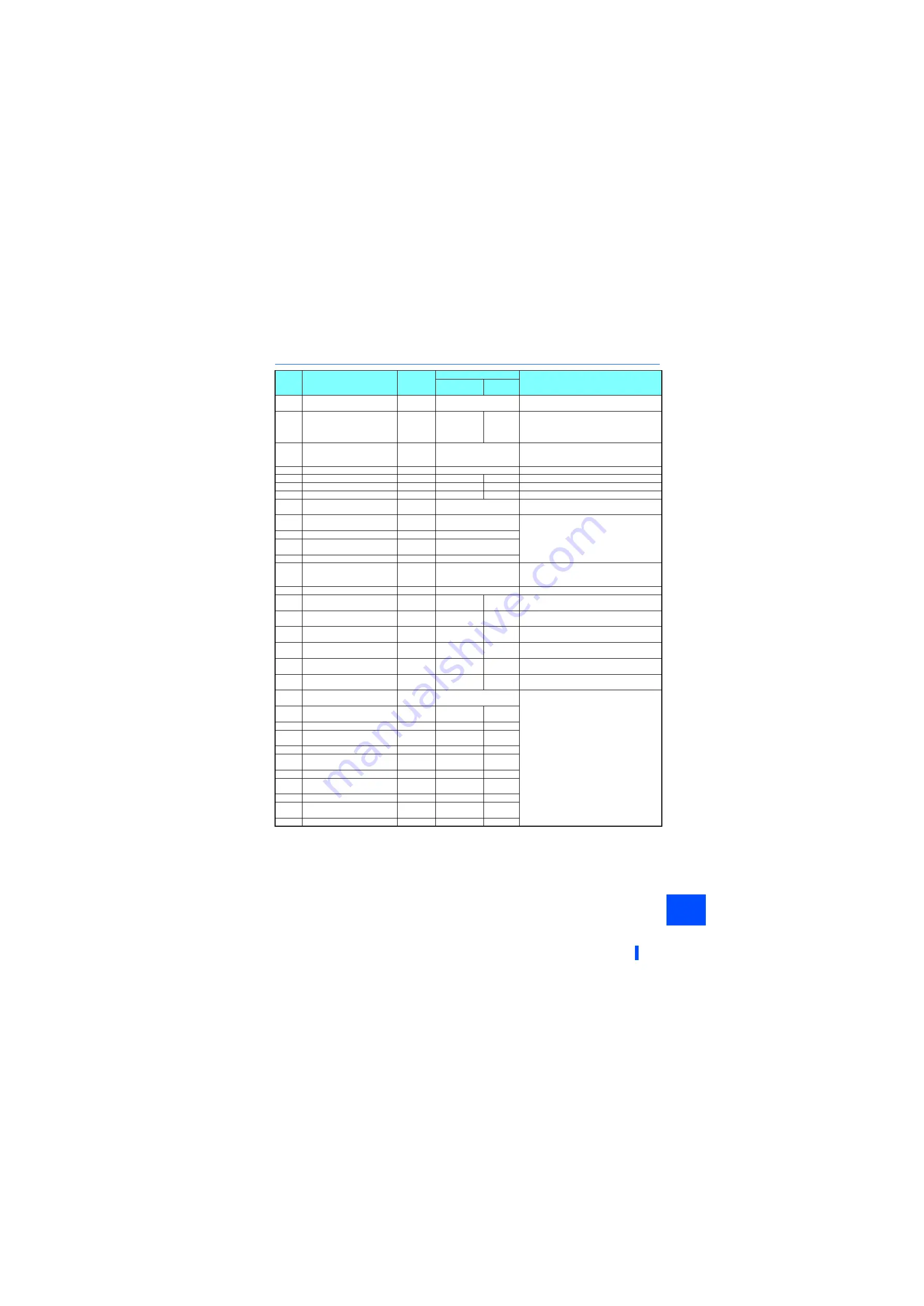
Application examples
211
10
∗1
Adjustment parameter for adjusting the setting of another parameter.
1246
Line speed at winding diameter
calculated value activation
1 m/min
1 m/min
Set the line speed command value to start the roll
diameter calculation.
1247
Winding diameter change
increment amount limit
9999
9999
1 mm
Setting
Pr.1247
= "9999 (initial value)" disables
the roll diameter calculation.
Be sure to change the setting from the initial value
for the roll diameter calculation.
1249
Number of averaging for
winding diameter calculation
4
4
Use this parameter to enable the primary delay
filter relative to the result of the roll diameter
calculation.
1255
Accumulated amount
9999
9999
9999: Initial roll diameter calculation disabled.
1284
Taper mode selection
0
0
1
1 (for winding roller): Linear taper profile
1286
Winding diameter at taper start
9999
9999
240 mm
Set the roll diameter to start taper control.
1287
Taper ratio setting
0%
0%
20%
Set the taper ratio.
1401
Tension command increment
0
1
1: Setting increment: 0.1 N, setting range: 0 to
1000 N
1402
Tension command input voltage
bias
0%
0%
Set the tension command in the range of 0 to 300
N.
1403
Tension command bias
0 N
0 N
1404
Tension command input voltage
gain
100%
100%
1405
Tension command gain
1000 N
300 N
1406
Commanded tension reduction
scaling factor during stall
condition
20%
20%
Commanded tension during stall mode = Tension
command value ×
Pr.1406
1407
Speed limit during stall condition 1 Hz
1 Hz
Set the speed limit to be used during stall mode.
1410
Motor inertia
0
0
0.01
Set the motor inertia for the inertia compensation
function.
1411
Empty reel inertia
0
0
0.01
Set the empty reel inertia for the inertia
compensation function.
1412
Roll width
0
0
50 mm
Set the roll width for the inertia compensation
function.
1413
Material specific gravity
0
0
1.4
Set the specific gravity of the material for the
inertia compensation function.
1414
First acceleration time for inertia
compensation
15 s
15 s
5 s
Set the acceleration time for the inertia
compensation function.
1415
First deceleration time for inertia
compensation
15 s
15 s
5 s
Set the deceleration time for the inertia
compensation function.
1419
Mechanical loss setting
frequency bias
1000%
1001.5%
Set the frequency and the compensation value for
each setting of mechanical loss.
For setting, start measuring mechanical loss with
an empty reel attached at low speeds, and
gradually increase the set speed to find the speed
requiring mechanical loss compensation.
1420
Mechanical loss setting
frequency 1
9999
9999
1.33 Hz
1421
Mechanical loss 1
1000%
1000%
1001.5%
1422
Mechanical loss setting
frequency 2
9999
9999
2 Hz
1423
Mechanical loss 2
1000%
1000%
1002%
1424
Mechanical loss setting
frequency 3
9999
9999
4.67 Hz
1425
Mechanical loss 3
1000%
1000%
1002.5%
1426
Mechanical loss setting
frequency 4
9999
9999
23.33 Hz
1427
Mechanical loss 4
1000%
1000%
1003%
1428
Mechanical loss setting
frequency 5
9999
9999
50 Hz
1429
Mechanical loss 5
1000%
1000%
1004%
Pr.
Parameter name
Initial
value
Setting value
Remarks
Intermediate
roller
Winding
roller
Содержание A800 Plus Series
Страница 240: ...239 MEMO ...