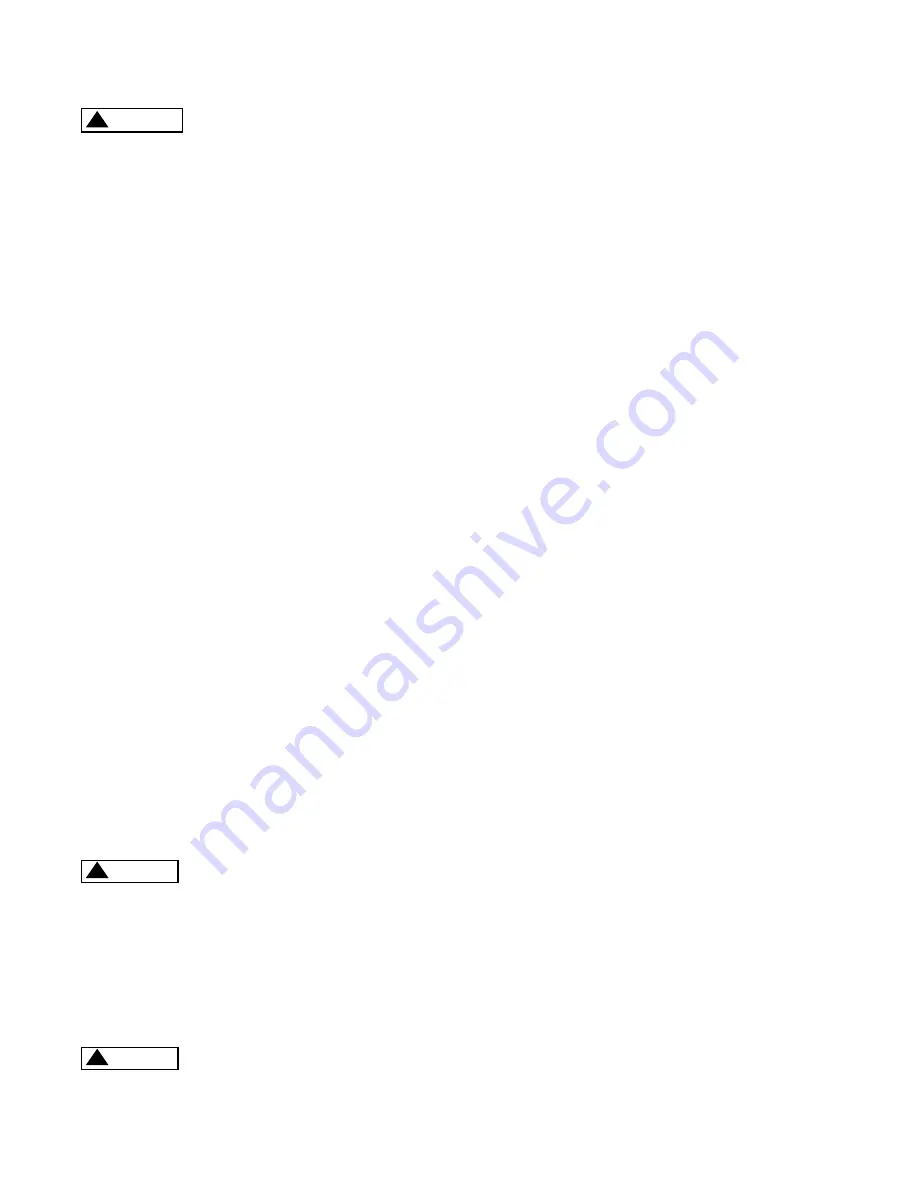
9
Accidental starting of the engine can
result in severe personal injury or death. Disconnect
the 110 VAC power cord from the starter switch junction
box or disconnect the negative (-) battery cable on 12
VDC starter models. Also disconnect the spark plug
wire while servicing the engine, controls, or associated
equipment.
HOURLY CHECK
Due to the large amount of dust that can be encountered in
floor care applications, the recoil dust filter should be
checked after each hour of operation. Remove and clean
the filter.
DAILY CHECKS
The operator should make a complete visual and audible
inspection of the engine daily. Check the following before
starting the engine for the first time each day.
1. Check all fuel lines and fitting for possible leakage.
2. Check crankcase oil level with the engine off. If engine
has been run, allow a minimum of 10 minutes for the
oil to drain down before checking. Check oil level with
machine in operating position. Do not operate engine
with the oil level below the ADD mark or above the FULL
mark.
3. Inspect exhaust system for possible leakage and
cracks. Locate leaks in muffler and piping while the
engine is operating. Repair leaks immediately.
4. Inspect air cleaner system for leaks. Make certain all
clamps and fittings are tight and free of potential leaks.
5. Check the engine cooling system to make sure the
cooling fins and ducting area are clean. Remove dust,
dirt or oil from the cooling surfaces.
DAILY (8 HOUR) MAINTENANCE
The operator should check the following before the first
start of the day and after every eight hours of operation:
1. Inspect fuel lines and fittings for leaks. Repair leaks
immediately.
2. Look and listen for exhaust system leaks while the
engine is running. Look for cracks and severe rusting
in the muffler and tailpipe. Have all leaks repaired before
continuing to operate the equipment.
Hot exhaust parts can cause severe
burns. Allow the engine time to cool before
servicing the exhaust system.
3. Check the engine for dirt and debris and clean the
flywheel air inlet screen and cylinder cooling fins as
necessary. On floorcare equipment engines, remove
the cooling air precleaner element every 4 to 8 hours of
operation and wash it in warm water and mild detergent.
Rinse it thoroughly and let it dry before reusing it. Do
not oil the element.
A clogged flywheel air inlet precleaner
or screen or dirty cooling fins can cause overheating
and engine damage. Keep the cooling fins and air inlet
screen clean.
MAINTENANCE PROCEDURES
4. Check the engine oil level. The equipment must be
parked on a level surface and the engine stopped. To
get an accurate reading, wait a minute or so to allow
the oil to settle in the crankcase if the engine has been
running.
ENGINE MAINTENANCE
1. Cooling Fin Maintenance: Remove the blower housing
and other cooling shrouds. Clean the cooling fins as
necessary using compressed air or pressure washer.
Reinstall all housings and shrouds.
2. Head Bolt Maintenance: Refer to Engine Manufacturer’s
Service manual.
BELT MAINTENANCE
NOTE: To inspect the belt it is necessary to turn the machine
over. The machine should be turned to the operator’s right
side for all Briggs & Stratton models. If the belt is badly
cracked or worn, it should be replaced. To check for the
proper tightness, squeeze the belt together. The belt should
depress between 1/4 and 1/2 inch. To change belt follow
these instructions:
•
Turn burnisher over on the right side.
•
Remove the pad holder by holdng the end of the
shaft on the top of the machine with a 3/4 inch
wrench and turn the pad holder counter-clockwise.
•
Using the 3/4 inch wrench to turn the end of the
spindle shaft on the top of the machine while
removing the old belt from the spindle pulley.
•
Check engine pulley for correct alignment with the
spindle pulley. Check hardware attaching pulleys
for correct tightness.
•
Install the new belt onto the engine pulley.
•
Reinstall the new belt onto the spindle pulley using
the 3/4 inch wrench to turn the spindle clockwise.
Make sure the belt is correctly placed on the idler
pulley.
•
Check belt for correct operation.
•
Check all hardware for correct tightness.
WARNING
!
CAUTION
!
CAUTION
!
FUEL SYSTEM
The fuel system works from vacuum created by the engine
running. Turning the cylinder service valve on pressurizes
the system for flow to the carburetor once the engine starts
to crank.
1. Engine Dust Filter:
FAILURE TO MAINTAIN A CLEAN
ENGINE FILTER MAY CAUSE THE EXHAUST
EMISSIONS TO ELEVATE TO DANGEROUS LEVELS.
ALSO, IT WILL CAUSE THE ENGINE TO OVERHEAT,
AND EVENTUALLY DAMAGE THE ENGINE. The
engine dust filter should be cleaned each hour and
after each use by shaking out the dust and then rinsing
with soapy water. Allow filter to air dry, do not wring
out water, this could damage the filter, (squeeze out).
2. Fuel System Adjustment:The carburetor and regulator
have been pre-set at the factory and do not require any
modification. Only authorized, trained personnel should
work on the fuel system of a propane buffer.
Содержание M220021H13
Страница 1: ...Mirage Propane Burnisher OPERATION SERVICE PARTS CARE Model M220021H13...
Страница 2: ......
Страница 16: ...13 ENGINE 13HP HONDA...
Страница 18: ...15 ENGINE 13HP HONDA...
Страница 20: ...17 WIRING DIAGRAM 13HP HONDA...