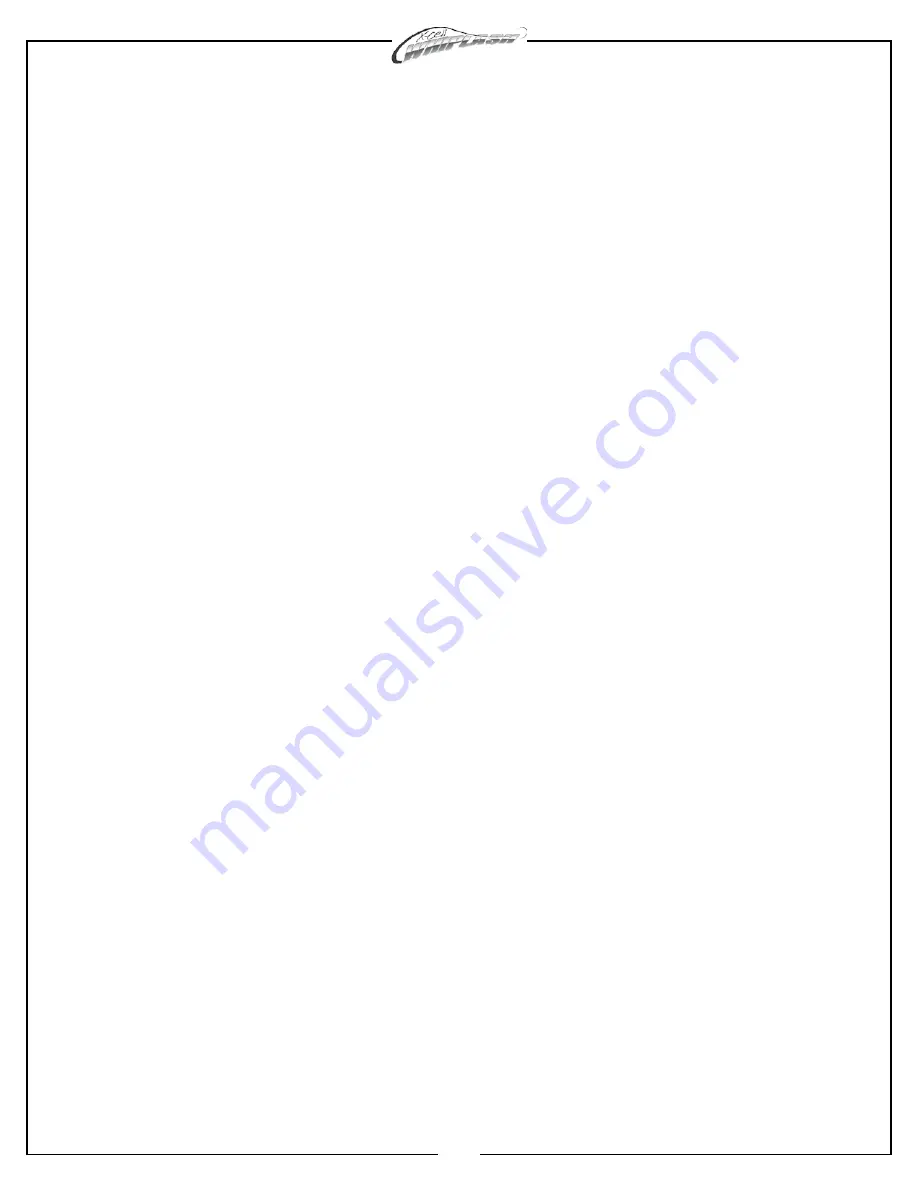
Swashplate eCCPM Set Up:
Now that you’ve built your new Whiplash helicopter, you have to make the servos work together. The Whiplash is an eCCPM
model, and requires a specific radio program for the servos that control the swashplate. eCCPM is a mix that is already
programmed in your transmitter, you just have to fine tune it to your Whiplash and here’s how:
The very first thing you need to do is tell your radio that a 120 degree eCCPM mix must be used. All modern transmitters
should have 120 degree eCCPM built programmed from the factory. Consult the manual that came with your radio! Before
you turn on your Transmitter and power up your servos, you need to make sure they are centered. With your transmitter
and receiver powered on, put collective stick in the exact center with all three swashplate servo horns removed. Then put
the horns on so they are 90 degrees to the linkage. This centers the servo horn on the servo and assures that there will be
equal travel on either side of the servo’s center point. If you find that you cannot get the servo horn exactly at center, you
have two choices. You can flip the horn 180 degrees, sometimes the splines will line up perfect, this is the preferred method.
You can also use a bit of “sub-trim” to center the servo. You really want to avoid using subtrim because it makes leveling the
swashplate a little more involved.
Now you need to make sure that your servos are all working together. What we mean is the three collective servos need to be
plugged into the appropriate channels, i.e. the elevator (which is the servo that controls the center ball on the swash) needs to
be plugged in to channel 3, the aileron and pitch servo (the ones that control the sides of the swashplate) need to be plugged
into channels 2 and 6 (it doesn’t matter which channel just either servo, into either 2 or 6 on the RX).
The channel assignments for ail, elev, rudder, throttle and pitch may vary depending upon the brand and model of your radio.
Consult the transmitter manual or use the TX servo monitor (if it has one) to ensure that the correct servo is receiving its signal
from the correct channel. Note: the position of the pitch and aileron servos in relationship to the elevator as indicated in your
radios setup manual are important. Make sure you connect them exactly as the radio manual shows when the swashplate is
viewed from above.
Then, using the servo reverse screen, you need to make sure that the servos are doing the proper function. All the servos
need to move up (or down) when the collective stick is moved up or down (it doesn’t matter if the collective is reversed, we’ll
fix that later). If it doesn’t, you need to (one at a time) reverse the channels on the servo reverse screen until all the servos
move in the same direction when the collective stick is moved.
Now the aileron and elevator functions need to be sorted out. When you move the right stick right and left, the swashplate
should tilt to the right and left (it doesn’t matter if it moves right when you push the stick left, we’ll fix that later). Also, when
you move the right stick forwards and aft, the elevator should tilt forward or back (at this point it doesn’t matter if the function is
reversed, proper direction will be addressed in the next step).
Now that the SERVOS are all moving in together, we need to be sure that the SWASHPLATE is moving correctly for a given
command. Pull up the Swash Mix screen. Futaba calls it “Swash AFR” There should be 3 functions and they’ll look like this:
Aileron: 60%
Elevator: 60%
Pitch: 60%
So, if the the swashplate tilts left when you move the cyclic (right) stick TO the right, make the value of 60% for Aileron
NEGATIVE or -60%, and likewise for the elevator. If the swash tilts forward when you pull the cyclic stick BACK, make the
value of 60% NEGATIVE or -60% to correct it.
The swashplate should move up and down with the collective stick, and if you RAISE the collective stick, the blades should
show POSITIVE PITCH. And if you LOWER the collective stick, the blades should show NEGATIVE pitch. IF that function is
reversed, again, make the value of 60%, NEGATIVE 60% or -60%.
To ensure that your Whiplash is set up as precise as possible, it is very important that you follow the pitch curve set up
guide and properly level the swashplate. There are several different tools for determining if your swashplate is level. We
recommend the MA3000-10 Swashplate Leveling Tool.
Place the swashplate leveler on the swashplate and ensure that it is level. The collective stick should be at the center with
zero degrees pitch on the blades. At this same time as described in the pitch curve set up guide, the swashplate should then
be in the center of its travel, and the midpoint of the pitch curve should read 50%. If the swashplate is not level, you can use
subtrim to level it, but the preferred method would be adjusting the linkages that connect the swashplate to the servos! If you
find that you have to use more than a couple of clicks of subtrim on any channel, you should put it back to zero, and adjust
mechanically by adjusting the linkages to the swashplate. After the swashplate is perfectly level at center stick, you need to
level it at the extreme pitch range, i.e. full positive pitch and full negative pitch.
Place the Collective stick at full positive stick with the swash leveling tool attached. If the swashplate is not level, you will
use the End Point screen or Travel Adjust screen. For instance, if the swashplate tilts slightly to the right at full positive pitch,
then you will need to increase the travel for the servo that controls that swashplate ball. Now put the collective stick at full
negative and repeat the same procedure with the end points. You do have to be careful that you don’t create any binding at
the extremes of the swashplate’s travel.
31