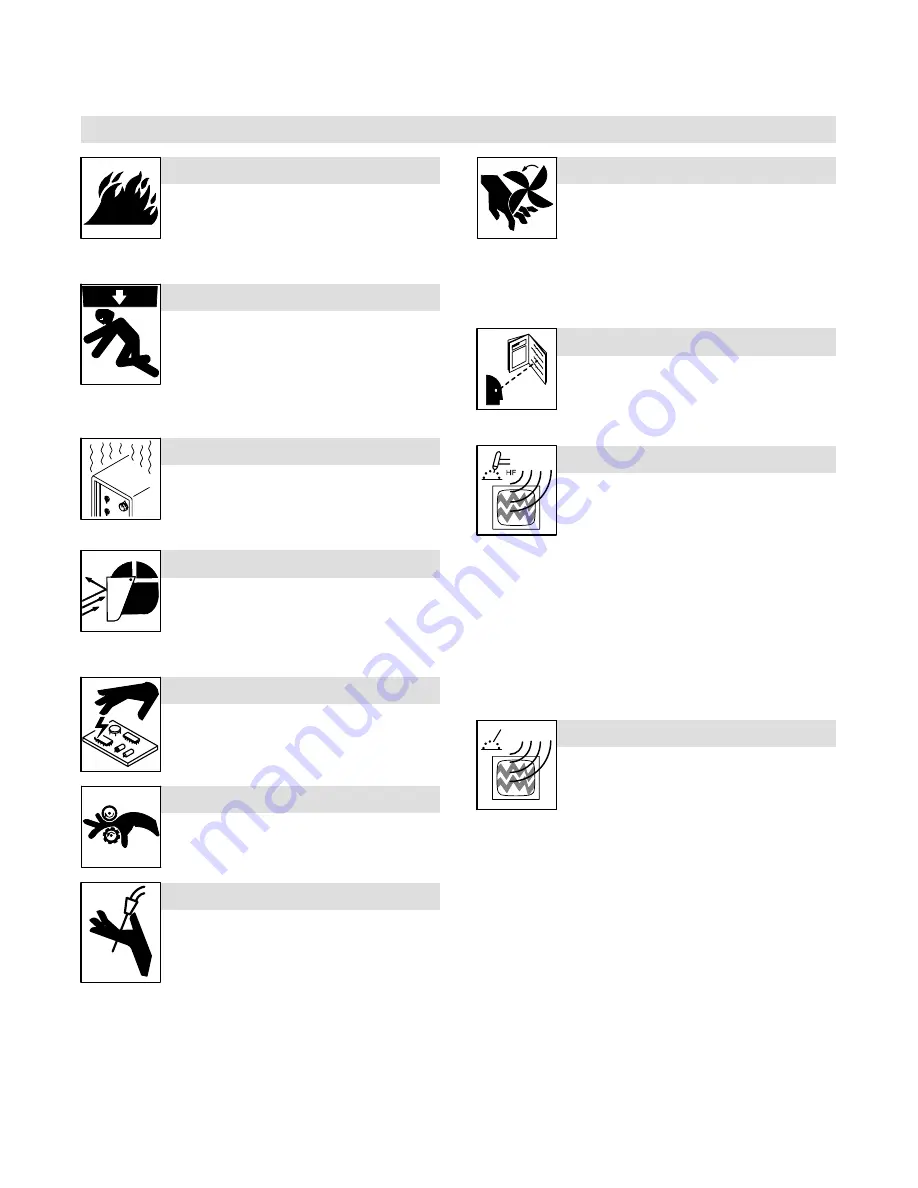
OM-239 210 Page 3
D
Read and follow instructions on compressed gas cylinders,
associated equipment, and Compressed Gas Association (CGA)
publication P-1 listed in Safety Standards.
1-3. Additional Symbols For Installation, Operation, And Maintenance
FIRE OR EXPLOSION hazard.
D
Do not install or place unit on, over, or near
combustible surfaces.
D
Do not install unit near flammables.
D
Do not overload building wiring
−
be sure power supply system is
properly sized, rated, and protected to handle this unit.
FALLING UNIT can cause injury.
D
Use lifting eye to lift unit only, NOT running
gear, gas cylinders, or any other accessories.
D
Use equipment of adequate capacity to lift and
support unit.
D
If using lift forks to move unit, be sure forks are
long enough to extend beyond opposite side of
unit.
OVERUSE can cause OVERHEATING
D
Allow cooling period; follow rated duty cycle.
D
Reduce current or reduce duty cycle before
starting to weld again.
D
Do not block or filter airflow to unit.
FLYING SPARKS can cause injury.
D
Wear a face shield to protect eyes and face.
D
Shape tungsten electrode only on grinder with
proper guards in a safe location wearing proper
face, hand, and body protection.
D
Sparks can cause fires — keep flammables away.
STATIC (ESD) can damage PC boards.
D
Put on grounded wrist strap BEFORE handling
boards or parts.
D
Use proper static-proof bags and boxes to
store, move, or ship PC boards.
MOVING PARTS can cause injury.
D
Keep away from moving parts.
D
Keep away from pinch points such as drive
rolls.
WELDING WIRE can cause injury.
D
Do not press gun trigger until instructed to do
so.
D
Do not point gun toward any part of the body,
other people, or any metal when threading
welding wire.
MOVING PARTS can cause injury.
D
Keep away from moving parts such as fans.
D
Keep all doors, panels, covers, and guards
closed and securely in place.
D
Have only qualified persons remove doors, panels, covers, or
guards for maintenance as necessary.
D
Reinstall doors, panels, covers, or guards when maintenance is
finished and before reconnecting input power.
READ INSTRUCTIONS.
D
Read Owner’s Manual before using or servic-
ing unit.
D
Use only genuine replacement parts from the
manufacturer.
H.F. RADIATION can cause interference.
D
High-frequency (H.F.) can interfere with radio
navigation, safety services, computers, and
communications equipment.
D
Have only qualified persons familiar with
electronic equipment perform this installation.
D
The user is responsible for having a qualified electrician prompt-
ly correct any interference problem resulting from the installa-
tion.
D
If notified by the FCC about interference, stop using the
equipment at once.
D
Have the installation regularly checked and maintained.
D
Keep high-frequency source doors and panels tightly shut, keep
spark gaps at correct setting, and use grounding and shielding to
minimize the possibility of interference.
ARC WELDING can cause interference.
D
Electromagnetic energy can interfere with
sensitive electronic equipment such as
computers and computer-driven equipment
such as robots.
D
Be sure all equipment in the welding area is
electromagnetically compatible.
D
To reduce possible interference, keep weld cables as short as
possible, close together, and down low, such as on the floor.
D
Locate welding operation 100 meters from any sensitive elec-
tronic equipment.
D
Be sure this welding machine is installed and grounded
according to this manual.
D
If interference still occurs, the user must take extra measures
such as moving the welding machine, using shielded cables,
using line filters, or shielding the work area.
Содержание XR-ALUMAFEED
Страница 4: ......
Страница 14: ...OM 239 210 Page 10...
Страница 35: ...OM 239 210 Page 31 Notes...
Страница 36: ...OM 239 210 Page 32 SECTION 9 ELECTRICAL DIAGRAMS Figure 9 1 Circuit Diagram For Wire Feeder...
Страница 37: ...OM 239 210 Page 33 239 209 B...