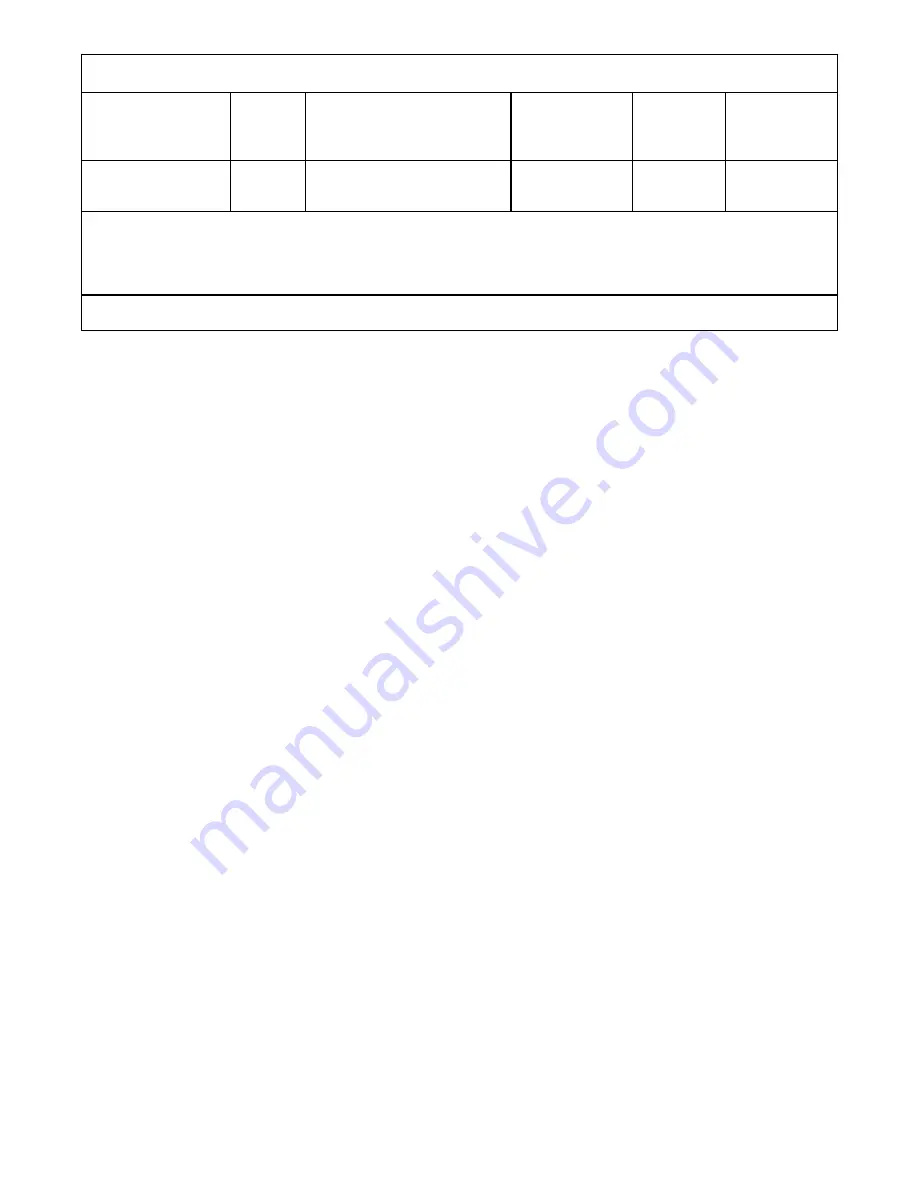
OM-246 466 Page 42
Flux Core
Process
Wire Size
in (mm)
Rolling Pipe/In Position
Wire Feed Speed
IPM (mpm)
Voltage
— —
Shielding Gas
Flux Core/GMAW
.045 (1.1)
175-300 w/200 Nominal
(4.4-7.6 w/5.1 Nominal)*
23-27 w/25
Nominal
— —
75/25*
Note: Arc Control is arc width and Arc Adjust/Trim is arc length. Wire feed speed and voltage are synergic for the
RMD and ProPulse processes. Therefore, when adjusting wire feed speed, the voltage is automatically adjusted so it
is not necessary to adjust Arc Adjust/Trim. These are only starting parameters, the operator must make final
adjustments depending on material and conditions.
*See wire manufacturer for recommended wire feed speed and gas mixture.
4-14. Welding Stainless Steel With And Without Backing Gas Using PipePro 300
When welding stainless steel with or without backing gas, the following guidelines are recommended:
1. Only use stainless steel wire with a high silicon content as it helps the flow of the weld puddle and the silicon acts as
a de-oxidizer.
2. It is important to have proper joint preparation and fit up. Use a bevel at the pipe joint of 35-37.5 degrees (70-75
degrees inclusive) with a land of a knife edge to 1/16 in. (1.6 mm) and a minimum gap of 1/8 in. (3.2 mm).
3. Be sure that any mill scale is remove from inside the pipe joint before welding the root weld. This can be done by
grinding the inside of the joint area.
4. Use Tri-H (90% helium/7.5% Argon/2.5% CO
2
shielding gas). A 98/2 Argon/ is available, but the Tri-H mixture is
the optimal choice for the application.
5. Always use a down hill technique when welding with the RMD process for the root pass weld.
6. It is very important to feather tack welds to ensure these are consumed when completing the root pass weld.
7. Always use a tapered nozzle when welding out the root especially with no backing gas to assist in providing
adequate shielding gas coverage.
Following these guidelines should result in successful welding of stainless steel using the PipePro 300. Contact the
nearest factory-authorized Distributor with any questions about this application.
Содержание OM-246 466B
Страница 14: ...OM 246 466 Page 10...
Страница 63: ...OM 246 466 Page 59 Notes...
Страница 64: ...OM 246 466 Page 60 SECTION 8 ELECTRICAL DIAGRAMS Figure 8 1 Circuit Diagram For Welding Power Source...
Страница 65: ...OM 246 466 Page 61 243 024 B...
Страница 74: ...Notes...