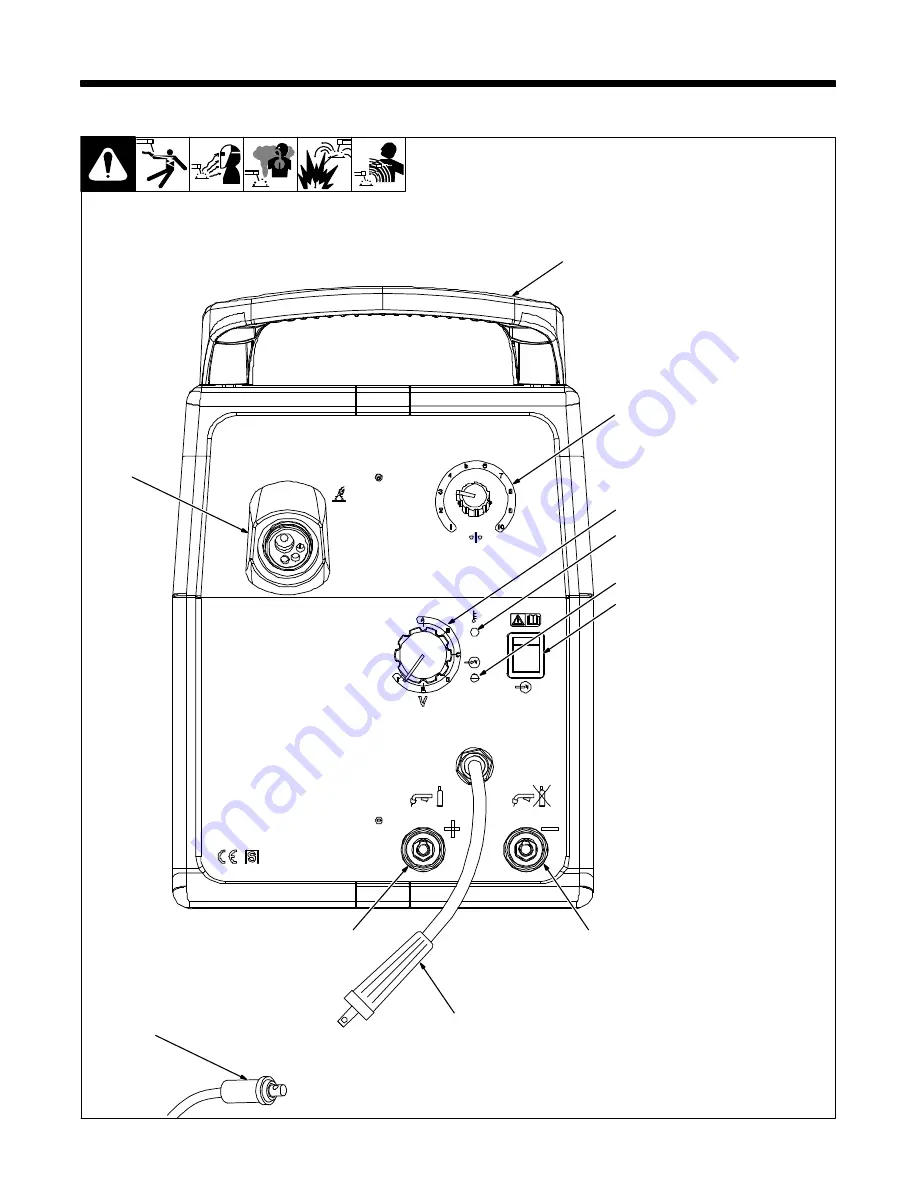
OM-259 158 Page 16
SECTION 4 − OPERATION
4-1.
Controls
1
Handle
2
Wire Speed Control
3
6 Position Voltage Control
4
Thermal Overload Pilot Light
5
Input Voltage Pilot Light
6
Power Switch
7
Negative Power Source
Terminal
8
Positive Power Source
Connector
9
Polarity Change Over Cable
10 Work Connection
11 Torch Connector
1
4
3
2
10
5
6
9
7
8
Ref. 956142985_2-A
11