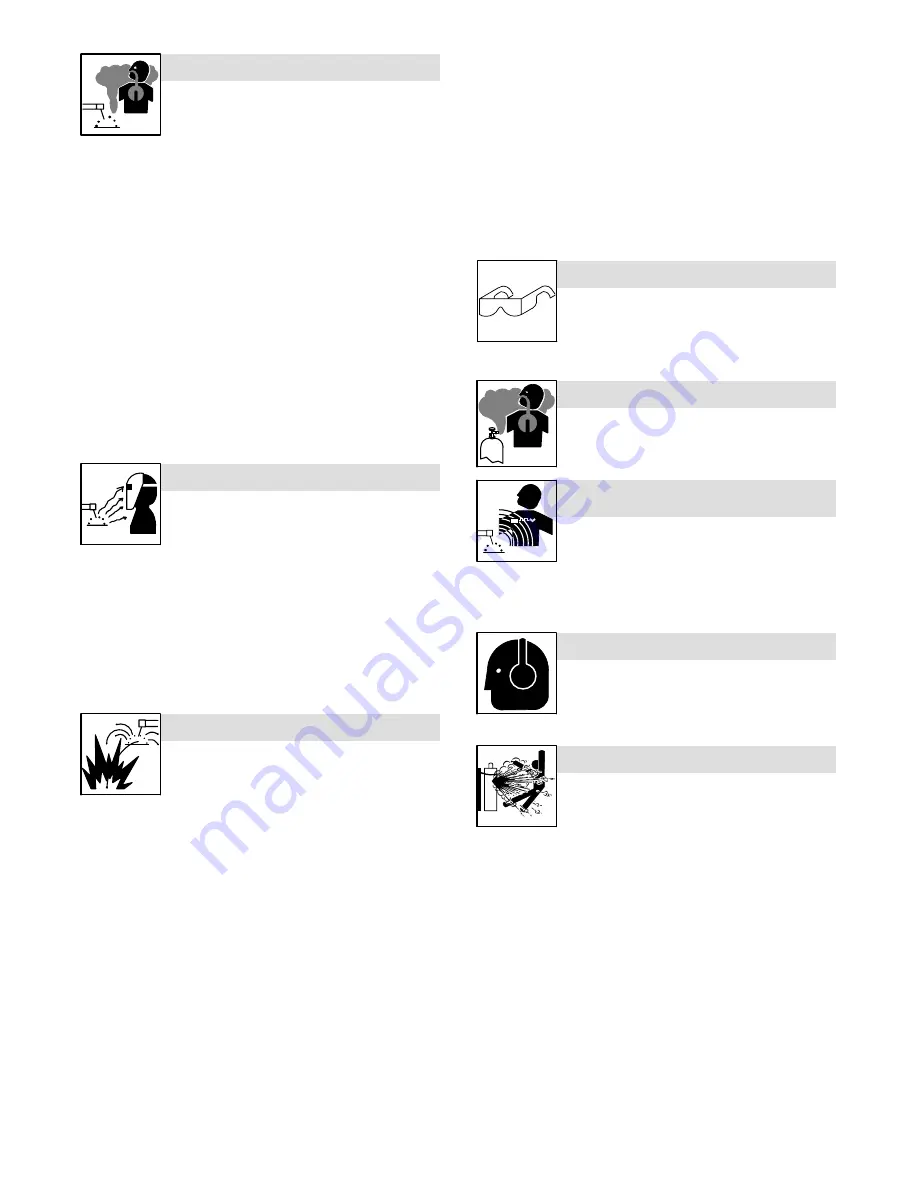
OM-212 296 Page 2
Welding produces fumes and gases. Breathing
these fumes and gases can be hazardous to your
health.
FUMES AND GASES can be hazardous.
D
Keep your head out of the fumes. Do not breathe the fumes.
D
If inside, ventilate the area and/or use local forced ventilation at the
arc to remove welding fumes and gases.
D
If ventilation is poor, wear an approved air-supplied respirator.
D
Read and understand the Material Safety Data Sheets (MSDSs)
and the manufacturer’s instructions for metals, consumables,
coatings, cleaners, and degreasers.
D
Work in a confined space only if it is well ventilated, or while
wearing an air-supplied respirator. Always have a trained watch-
person nearby. Welding fumes and gases can displace air and
lower the oxygen level causing injury or death. Be sure the breath-
ing air is safe.
D
Do not weld in locations near degreasing, cleaning, or spraying op-
erations. The heat and rays of the arc can react with vapors to form
highly toxic and irritating gases.
D
Do not weld on coated metals, such as galvanized, lead, or
cadmium plated steel, unless the coating is removed from the weld
area, the area is well ventilated, and while wearing an air-supplied
respirator. The coatings and any metals containing these elements
can give off toxic fumes if welded.
Arc rays from the welding process produce intense
visible and invisible (ultraviolet and infrared) rays
that can burn eyes and skin. Sparks fly off from the
weld.
ARC RAYS can burn eyes and skin.
D
Wear an approved welding helmet fitted with a proper shade of fil-
ter lenses to protect your face and eyes when welding or watching
(see ANSI Z49.1 and Z87.1 listed in Safety Standards).
D
Wear approved safety glasses with side shields under your
helmet.
D
Use protective screens or barriers to protect others from flash,
glare and sparks; warn others not to watch the arc.
D
Wear protective clothing made from durable, flame-resistant mate-
rial (leather, heavy cotton, or wool) and foot protection.
Welding on closed containers, such as tanks,
drums, or pipes, can cause them to blow up. Sparks
can fly off from the welding arc. The flying sparks, hot
workpiece, and hot equipment can cause fires and
burns. Accidental contact of electrode to metal objects can cause
sparks, explosion, overheating, or fire. Check and be sure the area is
safe before doing any welding.
WELDING can cause fire or explosion.
D
Remove all flammables within 35 ft (10.7 m) of the welding arc. If
this is not possible, tightly cover them with approved covers.
D
Do not weld where flying sparks can strike flammable material.
D
Protect yourself and others from flying sparks and hot metal.
D
Be alert that welding sparks and hot materials from welding can
easily go through small cracks and openings to adjacent areas.
D
Watch for fire, and keep a fire extinguisher nearby.
D
Be aware that welding on a ceiling, floor, bulkhead, or partition can
cause fire on the hidden side.
D
Do not weld on closed containers such as tanks, drums, or pipes,
unless they are properly prepared according to AWS F4.1 (see
Safety Standards).
D
Do not weld where the atmosphere may contain flammable dust,
gas, or liquid vapors (such as gasoline).
D
Connect work cable to the work as close to the welding area as
practical to prevent welding current from traveling long, possibly
unknown paths and causing electric shock, sparks, and fire
hazards.
D
Do not use welder to thaw frozen pipes.
D
Remove stick electrode from holder or cut off welding wire at
contact tip when not in use.
D
Wear oil-free protective garments such as leather gloves, heavy
shirt, cuffless trousers, high shoes, and a cap.
D
Remove any combustibles, such as a butane lighter or matches,
from your person before doing any welding.
D
After completion of work, inspect area to ensure it is free of sparks,
glowing embers, and flames.
D
Use only correct fuses or circuit breakers. Do not oversize or by-
pass them.
D
Follow requirements in OSHA 1910.252 (a) (2) (iv) and NFPA 51B
for hot work and have a fire watcher and extinguisher nearby.
FLYING METAL or DIRT can injure eyes.
D
Welding, chipping, wire brushing, and grinding
cause sparks and flying metal. As welds cool,
they can throw off slag.
D
Wear approved safety glasses with side
shields even under your welding helmet.
BUILDUP OF GAS can injure or kill.
D
Shut off shielding gas supply when not in use.
D
Always ventilate confined spaces or use
approved air-supplied respirator.
MAGNETIC FIELDS can affect Implanted
Medical Devices.
D
Wearers of Pacemakers and other Implanted
Medical Devices should keep away.
D
Implanted Medical Device wearers should consult their doctor
and the device manufacturer before going near arc welding, spot
welding, gouging, plasma arc cutting, or induction heating
operations.
NOISE can damage hearing.
Noise from some processes or equipment can
damage hearing.
D
Wear approved ear protection if noise level is
high.
Shielding gas cylinders contain gas under high
pressure. If damaged, a cylinder can explode. Since
gas cylinders are normally part of the welding
process, be sure to treat them carefully.
CYLINDERS can explode if damaged.
D
Protect compressed gas cylinders from excessive heat, mechani-
cal shocks, physical damage, slag, open flames, sparks, and arcs.
D
Install cylinders in an upright position by securing to a stationary
support or cylinder rack to prevent falling or tipping.
D
Keep cylinders away from any welding or other electrical circuits.
D
Never drape a welding torch over a gas cylinder.
D
Never allow a welding electrode to touch any cylinder.
D
Never weld on a pressurized cylinder
−
explosion will result.
D
Use only correct shielding gas cylinders, regulators, hoses, and fit-
tings designed for the specific application; maintain them and
associated parts in good condition.
D
Turn face away from valve outlet when opening cylinder valve.
D
Keep protective cap in place over valve except when cylinder is in
use or connected for use.
D
Use the right equipment, correct procedures, and sufficient num-
ber of persons to lift and move cylinders.
D
Read and follow instructions on compressed gas cylinders,
associated equipment, and Compressed Gas Association (CGA)
publication P-1 listed in Safety Standards.
Содержание HDC 1500DX CE
Страница 6: ......
Страница 42: ...OM 212 296 Page 36 SECTION 11 ELECTRICAL DIAGRAM 238 416 A Figure 11 1 Circuit Diagram...
Страница 43: ...OM 212 296 Page 37 Notes...