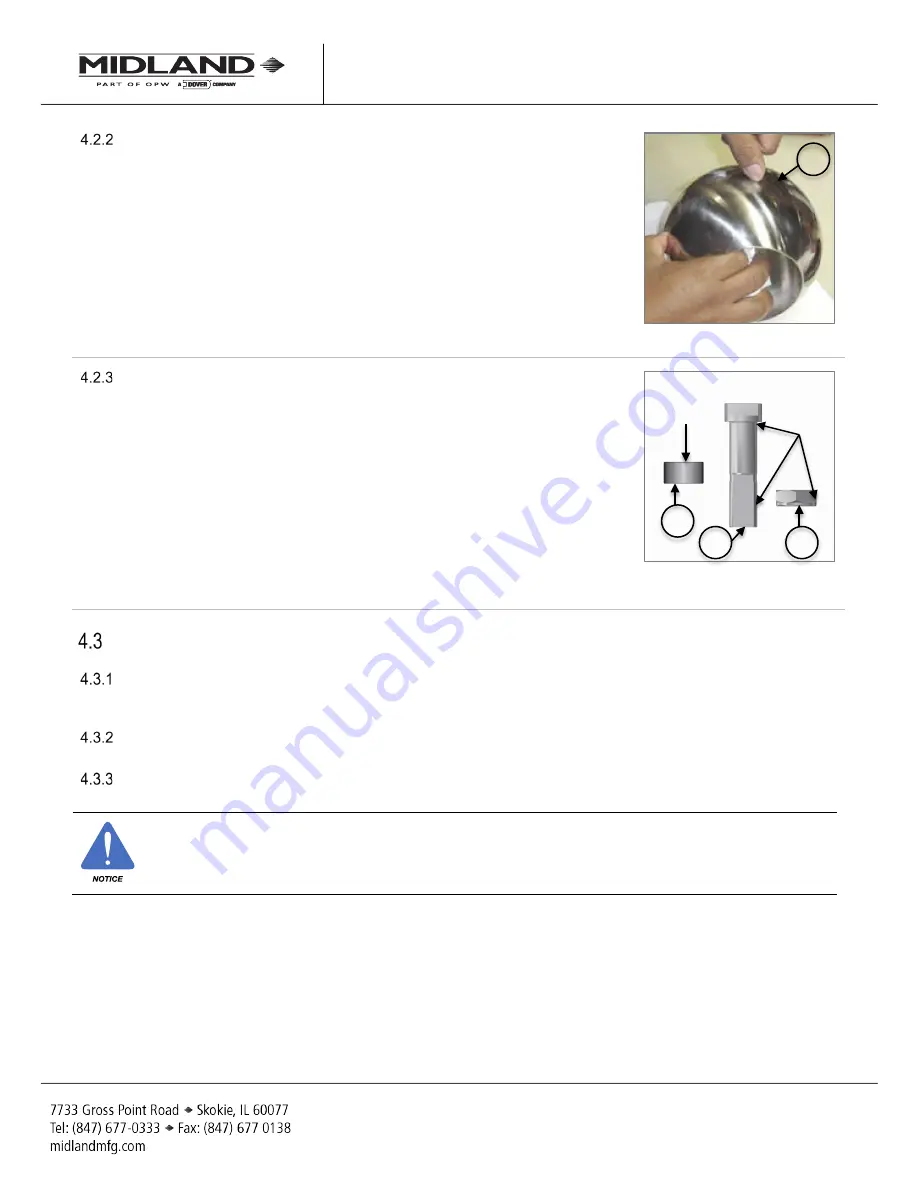
Page 19 of 28
Manual content is subject to change.
Visit midlandmfg.com for latest IOM revision and revision history.
Valve Ball Inspection
4.2.2.1 Clean the valve ball (item 3) with soap and water or in an ultrasonic bath, or
both, to remove adhering product.
4.2.2.2 Slide your fingernail over scratches to determine severity. If your fingernail
is unable to “catch” in an abrasion, it is not of a depth that would allow
leakage or affect the ball seals.
4.2.2.3 If any of the scratches fail the fingernail test, replace the ball. It cannot be
repaired.
Figure 4-14 Check Scratch Severity
Valve-Stem Components Inspection
4.2.3.1 The stem (item 2) 1-1/8”-12 UNF threads should pass a thread-ring Go-
Gauge test. If the threads exhibit stripping or irreparable damage, replace
the valve stem.
4.2.3.2 Inspect the surfaces of the spacer (item 6) bushing that contacts the stem
packing and thrust washer as shown in Figure 4-5. Also, inspect the surface
of the stem shaft. These surfaces should be smooth and clean.
4.2.3.3 Inspect the valve stem locknut for damage to the threads and the Nylon
®
locking insert. Replace the locknut if damage is observed and if the Nylon
®
insers is cracked, damaged or frayed.
Figure 4-15 Valve Stem and Spacer
Surfaces
Special Inspection Considerations
Previous procedures may not cover all conditions encountered in the field. Therefore, it is the responsibility of
the repair agency to contact an authorized Midland technical representative for recommendations regarding
unusual valve conditions or repair circumstances that may be encountered.
Evaluation of critical component metal surfaces of the valves after cleaning and inspection, by the repair facility
are the respsonsibility of the repair facility.
Where numerical tolerances cannot be provided, the disposition of the part or parts is under the jurisdiction of
the repair facility and dependent on its experience and judgment.
NOTICE:
To ensure best practices and consistency of your qualification procedure, gaskets, O-rings, valve
seats and wire seals should always be replaced.
3
13
Critical
Surfaces
2
6
Critical
Surface
A-520/A-522/A-522A
, Rev. 3.0