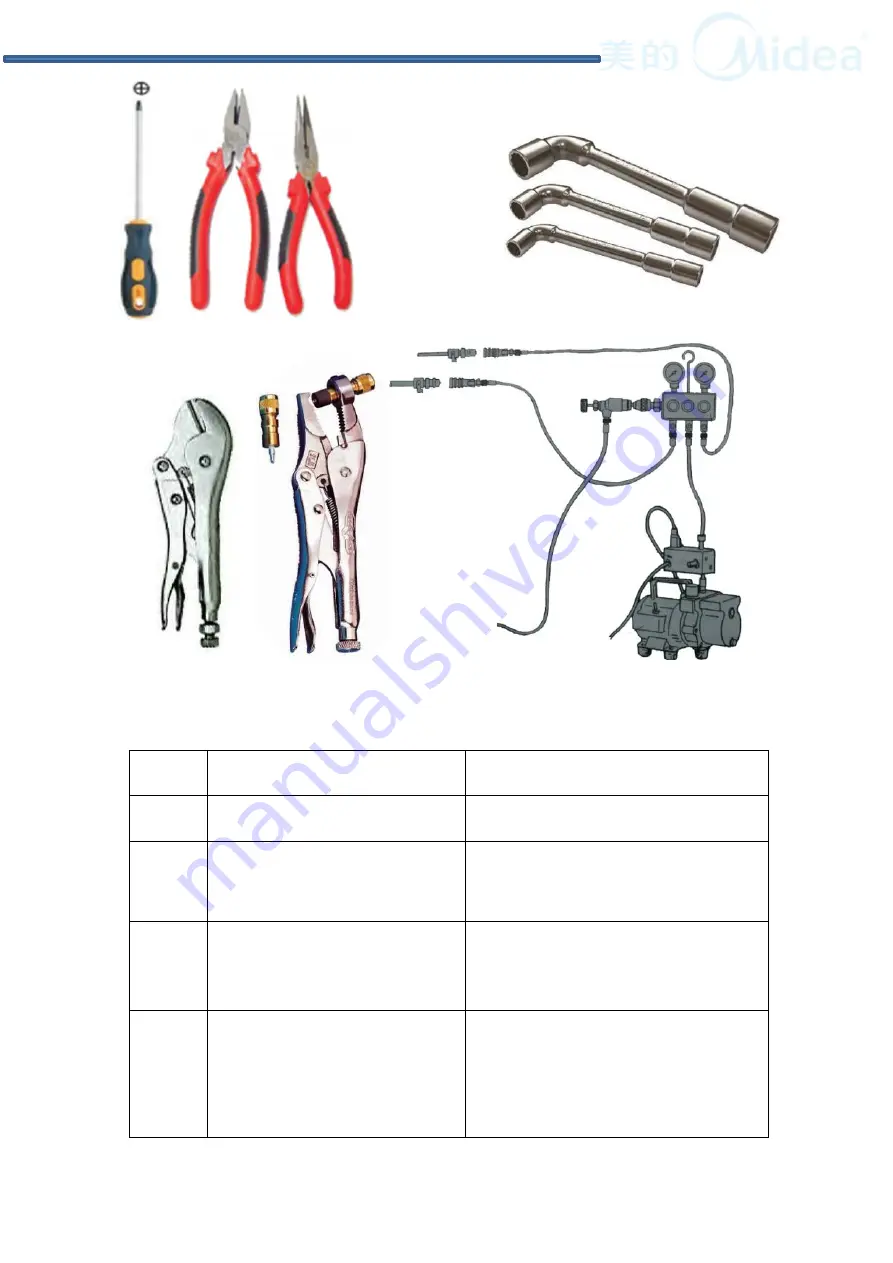
42
7 Service tools
Number
Tools
Suitable kit
1
Sleeve
(
M14
)
or spanner
drum tub assembly
2
Sleeve
(
M10
)
and pliers
Wheel Assembly
3
Other tools
(cross head screwdriver,
pliers and so on)
Common service tools
4
Vacuum pump, welding torch,
exhaust plier, sealing plier,
electronic scale, butane and
oxygen carrier, pipe cutter
and so on.
Weld and cut the pipe
Vacuum and charge.
M14
M10
M6
Exhaust plier
Vacuum and charge kits
Sealing pliers
Содержание MDC100-CH21B/B05E-US
Страница 26: ...Circuit diagram of dryer 26 The circuit program 5 Troubleshooting...
Страница 44: ...44 The end...