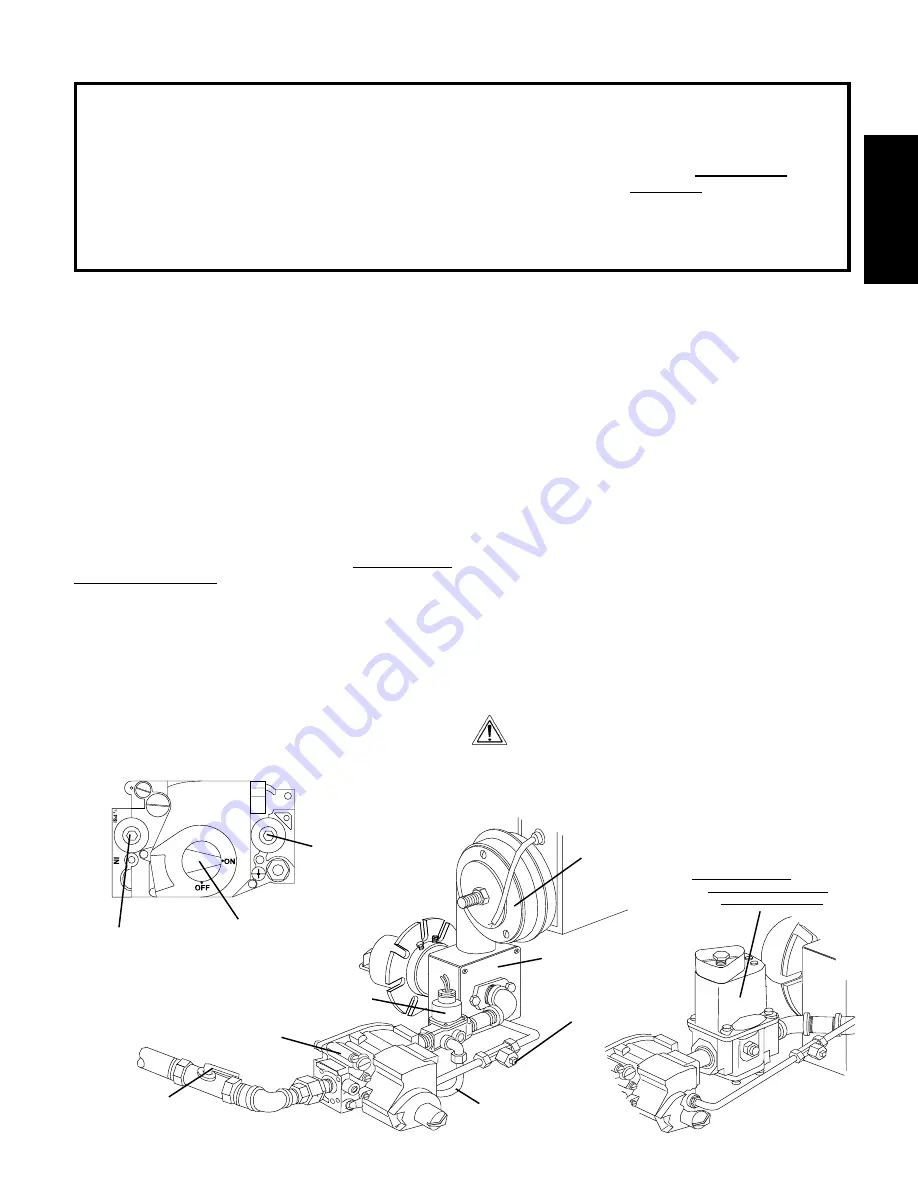
ENGLISH
15
IX. GAS SUPPLY (gas ovens only)
Figure 2-26 - Gas Burner and Piping Assembly
Manual
shutoff valve
Pilot pressure tap
(where pilot gas
pressure is measured)
Combination Gas
Control Valve
(Safety Regulator)
Inlet pressure tap
(where incoming
gas pressure is
measured)
Manifold pressure tap
(where manifold gas
pressure is measured)
On/Off Knob
Always leave in
ON position
Low Flame
Bypass Line
High Flame
Solenoid Valve
Burner
Blower
Gas Burner
Model PS360EWB Only
Modulating gas valve
NOTE:
PS360EWB ovens use a
modulating gas valve INSTEAD OF
a high flame solenoid valve and
low-flame bypass line.
SECTION 2 - INSTALLATION
A. Gas Utility Rough-In Recommendations
The following gas system specifications are STRONGLY
RECOMMENDED. Deviating from these recommendations
may affect the baking performance of the oven.
Gas Meter
One or two oven cavities: 750 cfh meter
Three or four oven cavities: 1200 cfh meter
Gas Line
DEDICATED LINE from the gas meter to the oven
2" (50.8mm) pipe for natural gas
1-1/2" (38.1mm) pipe for propane
Maximum length: 200' (61m). Each 90° elbow equals 7'
(2.13m) of pipe.
B. Connection
Check the ovens gas supply requirements before making the
gas utility connection. Gas supply requirements are listed on the
ovens serial plate (Figure 2-23) and in the Gas Orifice and
Pressure Specifications table (Page 5 of this manual).
Check the serial plate to determine the type of gas (Propane or
Natural) to be used with the oven.
Refer to the instructions in the gas hose package (included in the
Installation Kit) before connecting the gas line. One gas line
connection method is shown in Figure 2-25; however, compliance
with the applicable standards and regulations is mandatory.
Inlet, regulated, and pilot gas pressure readings can be taken
using a U tube manometer at the tap locations shown in Figure
2-26.
CAUTION
DURING PRESSURE TESTING NOTE ONE OF THE FOLLOWING:
1. The oven and its individual shutoff valve must be discon-
nected from the gas supply piping system during any pres-
sure testing of that system at test pressure in excess of 1/
2 psi (3.45 kPa).
2. The oven must be isolated from the gas supply piping
system by closing its individual manual shutoff valve during
any pressure testing of the gas supply piping system at test
pressure equal to or less than 1/2 psi (3.45 kPa).
3. If incoming pressure is over 14 W.C. (35mbar), a sepa-
rate regulator MUST be installed in the line BEFORE the
individual shutoff valve for the oven.
WARNING:
To prevent damage to the control valve regula-
tor during initial turn- on of gas, it is very important to open
the manual shutoff valve very slowly.
After the initial gas turn-on, the manual shutoff valve must
remain open except during pressure testing as outlined in
the above steps or when necessary during service mainte-
nance.
NOTE
The installation must conform with local codes or in the absence
of local codes, with the National Fuel Gas Code, ANSI Z223.1-
latest edition.
In Australia, the installation must conform with AGA Code AG601
and with any requirements of the appropriate statutory authority.
CANADIAN:
CAN/CGA-B 149.1 Natural Gas Installation Code
CAN/CGA-B 149.2 Propane Installation Code
Certain safety code requirements exist for the installation of gas
ovens; refer to the beginning of Section 2 for a list of the
installation standards. In addition, because the oven is equipped
with casters, the gas line connection shall be made with a
connector that complies with the Standard for Connectors for
Movable Gas Appliances, ANSI Z21.69 (in U.S.A.), or, if appli-
cable, Connectors for Movable Gas Appliances, CAN/CGA-6.16
(in Canada), as well as a quick-disconnect device that complies
with the Standard for Quick-Disconnect Devices for Use With
Gas Fuel, ANSI Z21.41 (in U.S.A.), or, if applicable, Quick-
Disconnect Devices for Use With Gas Fuel, CAN1-6.9 (in Canada).
C. Gas Conversion
Where permitted by local and national codes, it is possible to
convert ovens from natural to propane gas, or from propane to
natural gas. Use the appropriate Middleby Marshall Gas
Conversion Kit for the specific oven model.
WARNING
The terms of the oven's warranty require all start-ups,
conversions and service work to be performed by a Middleby
Marshall Authorized Service Agent.