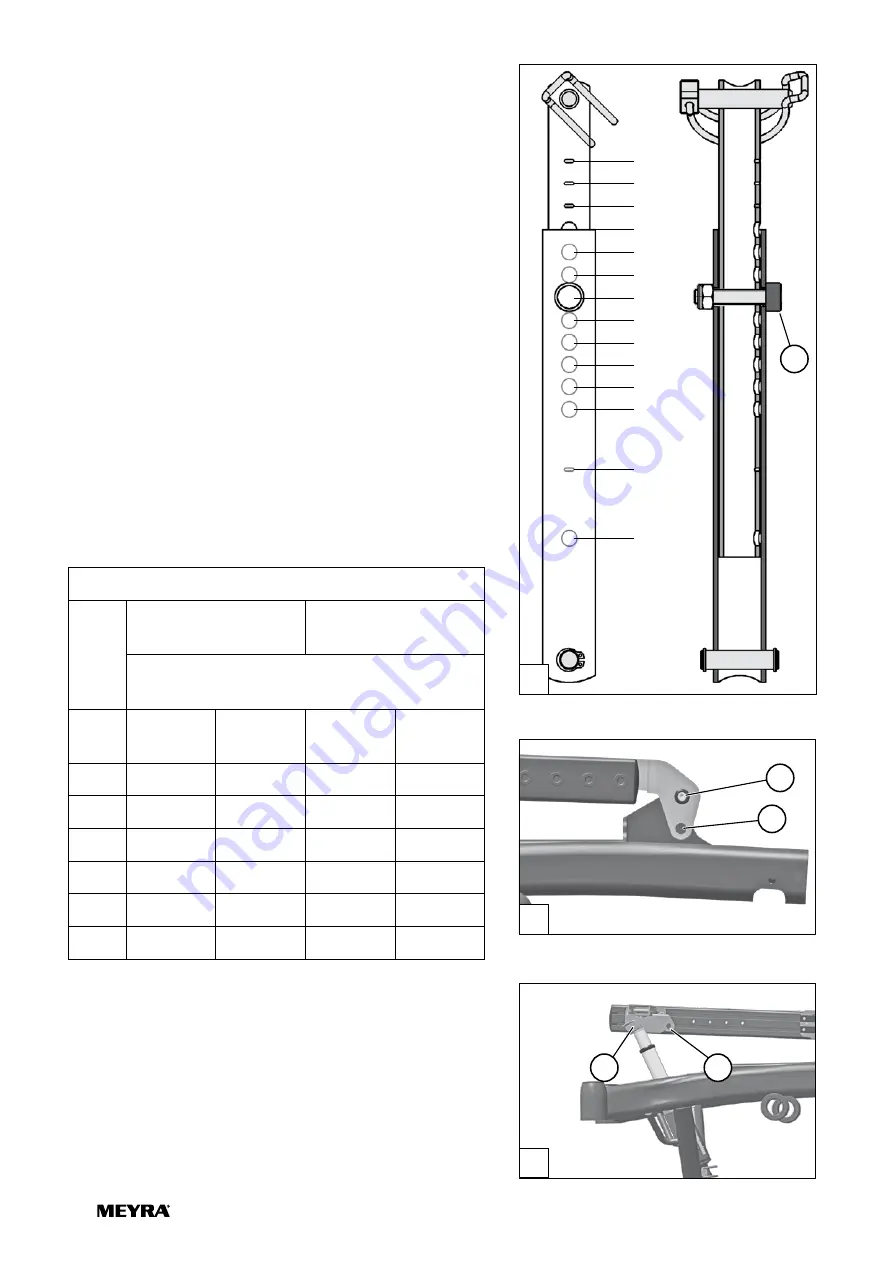
88
Adjusting the front seat height, model 1.616
In order to adjust the front seat height the corresponding
screw (Z) needs to be removed.
The hole in the telescopic tube [1] (column Pos.) for the
screw [Z] can be determined from the table <
Front seat
height
>, depending on the steering wheel size, the rear seat
frame position [2] and the position of the telescopic tube [3]
for the corresponding front seat height.
The bold printed figures for height (in mm) within the table
correspond to the manufacturer setting.
Pic. [1] shows the telescopic tube with marks and holes for
an exact adjustment.
☞
Symbol descriptions:
=
Mark for the hole ( )
( )
Pos. of the hole
= (S) Mark for the service setting
(S)
Hole for the service setting
Table: Front seat height
Front seat height in (mm) with 4° seat inclination
Steering wheel 8"
ø 203 mm
Steering wheel 9"
ø 229 mm
rear seat frame position [2] – position
telescopic tube [3]
Pos.
[1]
A - a
B - b
A - a
B - b
1
2
3
435
4
420
470
5
455
6
A
B
a
b
= (1)
= (2)
= (3)
(1) / = (4)
(2) / = (5)
(3) / = (6)
(4) / = (7)
(5) / = (8)
(6) / = (9)
(7)
(8)
(9)
= (S)
(S)
Z
1
2
3
Содержание 1.610
Страница 11: ...11 OVERVIEW Model 1 610 Model 1 611 1 614 Model 1 612 ...
Страница 12: ...12 Model 1 616 Model 1 615 Model 1 617 ...
Страница 82: ...82 Seat height 48 cm The attachment plate 1 is mounted to the topmost attach ment hole 4 5 6 4 1 4 4 1 6 6 5 ...
Страница 101: ...101 NOTES ...
Страница 102: ...102 NOTES ...
Страница 103: ...103 NOTES ...