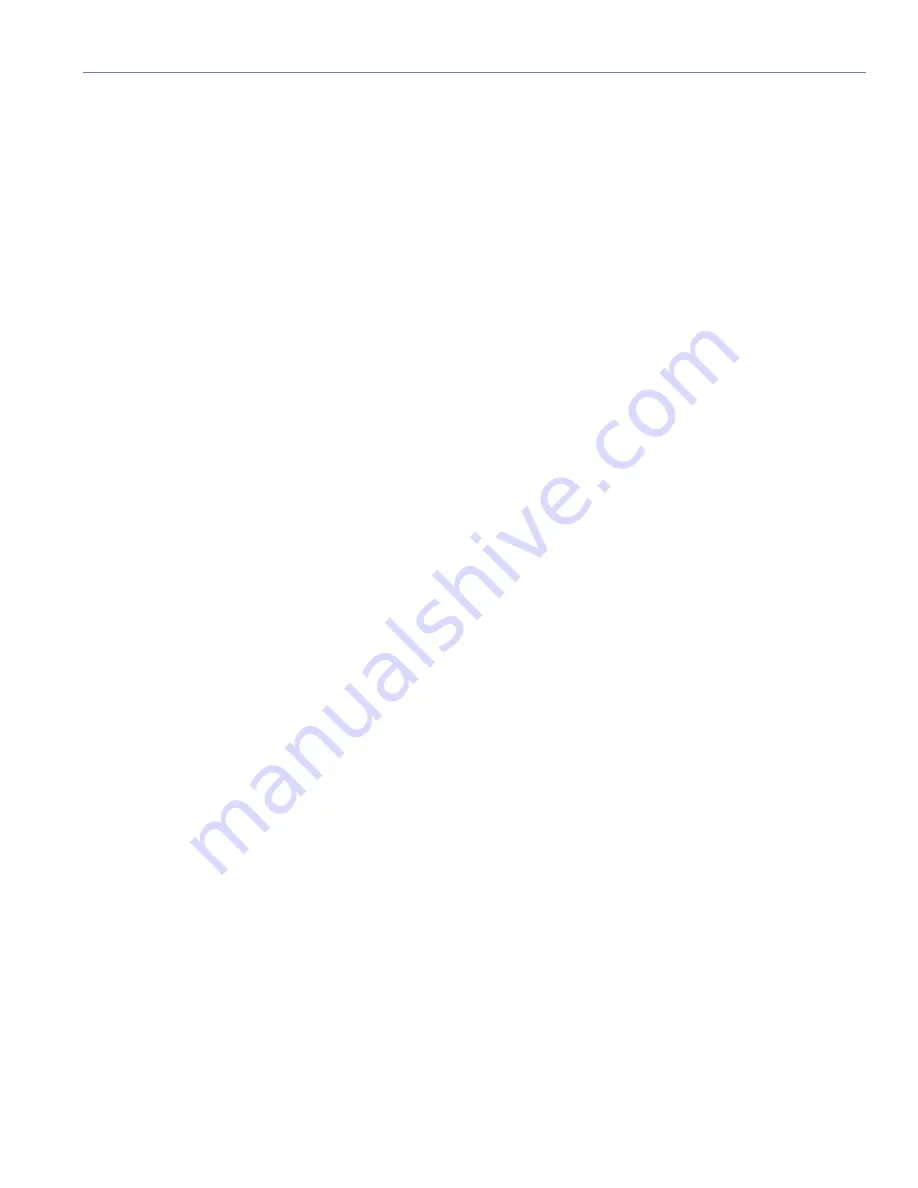
vi
vii
Advisory Note: Safety Responsibilities “Above
the Hook”
In most touring applications of rigging systems, the
touring sound provider is normally responsible for
ensuring the safety of the suspension system only below
the attachment point. The safety and suitability of the
attachment point is generally seen as the responsibility
of the venue owner or operator. However, this distinction
(“above the hook” versus “below the hook”) can be open
to interpretation. Touring system operators are advised
to double-check to make certain that attachment points
are approved and suitably load rated, and that the points
used are those identified as such by the venue owner
or operator. AS AN EXTRA PRECAUTION, CAREFUL
INSPECTION OF THE ATTACHMENT POINTS IS ADVISED
BEFORE FLYING, PARTICULARLY IN OLDER VENUES OR
THOSE HOSTING FREQUENT EVENTS USING LARGE
SOUND AND LIGHTING SYSTEMS. In any case, Meyer
Sound QuickFly systems are intended only for suspension
from approved rigging points, each known to have ample
SWL margins for the system components suspended
below them.
INSPECTION AND MAINTENANCE
The Meyer Sound QuickFly systems are an assembly of
mechanical devices, and are therefore subject to wear and
tear over prolonged use, as well as damage from corrosive
agents, extreme impact, or inappropriate use.
BECAUSE OF THE SAFETY ISSUES INVOLVED, USERS
MUST ADOPT AND ADHERE TO A SCHEDULE OF
REGULAR INSPECTION AND MAINTENANCE. IN
TOURING APPLICATIONS, KEY COMPONENTS MUST
BE INSPECTED BEFORE EACH USE. Such inspection
includes examination of all load-bearing components
for any sign of undue wear, twisting, buckling, cracking,
rusting, or other corrosion. In regard to rust and corrosion,
the main components of a QuickFly system are either
protected by an exterior coating or made from stainless
steel, which is impervious to rust and resistant to most
corrosive fluids. Nevertheless, normal use and shipping
vibrations can wear through the protective coatings,
and extremely corrosive fluids (such as battery acid)
can cause severe damage with prolonged exposure
even to protected parts. Particular attention should be
given to screws, bolts, and other fasteners to make
certain the fittings are tight and secure. Metal seams and
welds should be examined for any sign of separation or
deformation. Meyer Sound strongly recommends that
written documentation be maintained on each QuickFly
system, noting date of inspection, name of inspector,
points of system checked, and any anomalies discovered.
In addition to routine checks on the road for touring
systems, Meyer Sound also recommends a careful,
comprehensive system examination and testing “at
home” in the warehouse or other appropriate location at
regular intervals. At this time, each component should be
carefully inspected under ideal lighting conditions, and
then the entire system should be flown as used for a final
comprehensive check.
If any anomalies or defects are discovered that could
possibly affect the safety or integrity of the system, any
affected parts or subsystems should be replaced in their
entirety before that part of the system is flown again.
REPLACEMENT PARTS
Any component found to be defective, or any safety-
related component you even suspect might be defective,
should be replaced with the equivalent, approved part.
Parts specific to a QuickFly system should be ordered
directly from Meyer Sound. No attempt should be made
to substitute what appears to be equivalent or “mostly the
same” generic replacements. Some parts used in QuickFly
systems are identical to those used in other rigging
applications. To the best of our knowledge, most of these
suppliers are reputable and their products are reliable.
However, Meyer Sound has no way of assuring the quality
of products made by these various suppliers. Therefore,
Meyer Sound is not responsible for problems caused by
components that were not supplied by Meyer Sound.
TRAINING
Considering their sophistication and flexibility, QuickFly
systems are relatively straightforward and easy to use.
Nevertheless, key points of assembly, rigging, and flying
that must be fully mastered before a system is flown.
Users should read this manual in its entirety before
attempting to deploy any QuickFly system. You may make
additional copies of this manual as necessary for in-house
use; copies may not be made for any other purpose.
Содержание M3D
Страница 1: ...QUICKFLY RIGGING MANUAL M SERIES M3D and M3D Sub...
Страница 6: ...viii...
Страница 42: ...34 Figure 43 MTG 3D Top Grid physical dimensions...