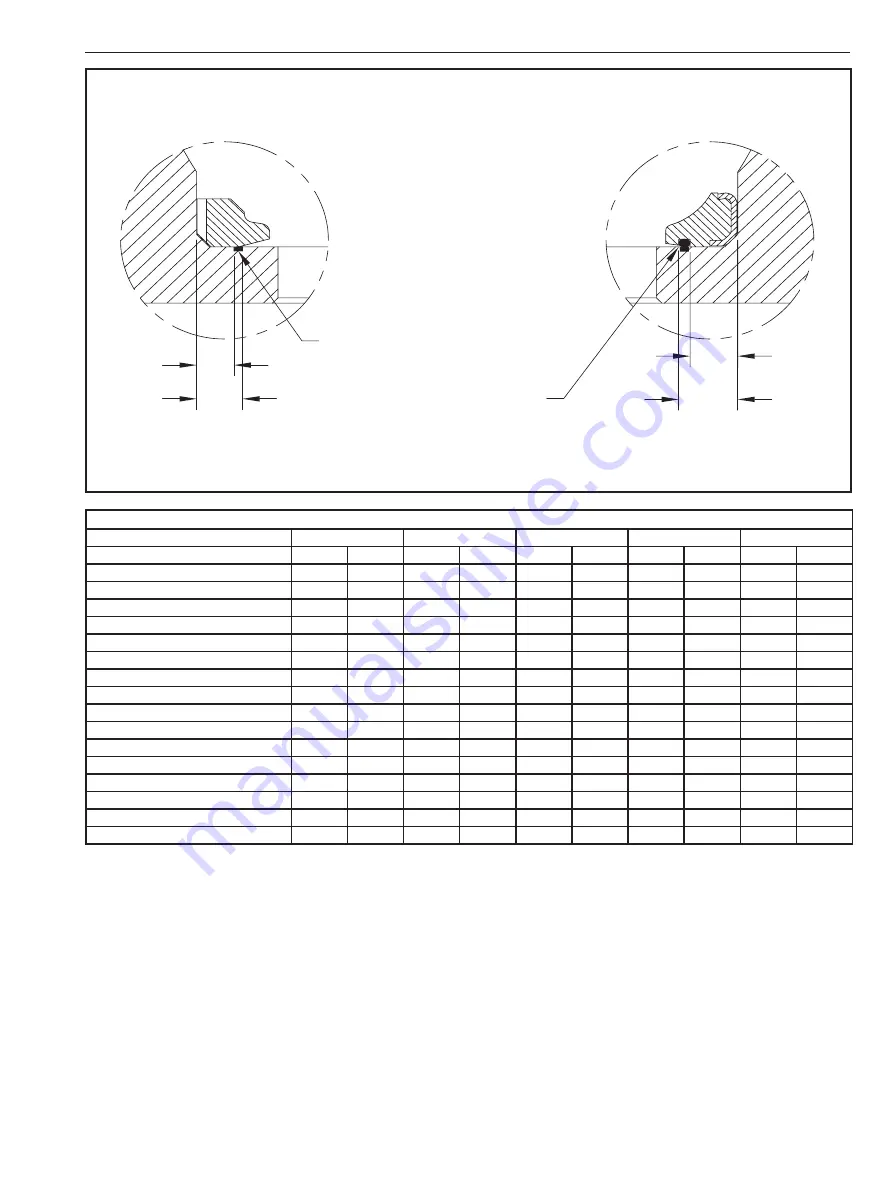
IMO
2/19
IMO-R26 EN
7
Figure 6: Seat Sealing Critical Area
Seat Sealing Area
A
B
A
B
Seat Sealing Area
Xtreme® (-9J), PTFE (-50),
MTFE (-49)
Sulphur Valve Barrier Seat
Material Code -47
(9RETS, 9RELS, SUZRC, SUZRL, SUZRS)
Table 1: Dimensions for ball valve seat cavity sealing location
Jamesbury
Size
PTFE (-50)
Xtreme
(-9J)
MTFE (-49)
W-Barrier (-47)
Railroad Ball Valves
Full
STD
Amin
Bmax
Amin
Bmax
Amin
Bmax
Amin
Bmax
6RFT
1
-
0.212
0.292
-
-
0.212
0.292
-
-
6RA3
2
-
0.180
0.260
-
-
0.180
0.260
-
-
9RFT/9FRT/9150RRR
2
-
0.181
0.259
0.176
0.264
-
-
-
-
9RFT/9FRT/9150RRR
3
-
0.274
0.356
0.274
0.356
-
-
-
-
6RIB3
4
-
0.411
0.493
-
-
0.411
0.493
-
-
9RET/9REL/9150RR
4
-
0.400
0.483
0.400
0.483
-
-
-
-
9RETS/9RELS (Sulphur Service)
4
-
-
-
-
-
-
-
0.461
0.651
5RRR/5RFF/5RFT
-
1
0.097
0.176
-
-
0.097
0.176
-
-
7RRT/7150RR
-
1
0.097
0.176
0.145
0.224
-
-
-
-
5RRU/5FRF/5ATR/5RRF/5RRT/5RNT
-
2
0.174
0.260
0.266
0.352
0.174
0.260
-
-
7RRT/7150RR
-
2
0.174
0.260
0.266
0.352
-
-
-
-
5RRF/5RRT
-
3
0.209
0.290
-
-
0.209
0.290
-
-
7RRT/7150RR
-
3
0.210
0.293
0.209
0.289
-
-
-
-
5REB3
-
4
0.249
0.330
-
-
-
-
-
-
5RET/AZFRS/AZFRC/AZFRL
-
4
0.361
0.443
-
-
0.361
0.443
-
-
SUZRS/SUZRC/SUZRL (Sulphur Service)
-
4
-
-
-
-
-
-
0.320
0.398
6.4.2 Remediating Damage
Body and Cap/Insert sealing areas may be dressed by hand
with 600 grit (minimum) sandpaper or equivalent so long as
it is applied concentric to the seal and not across the sealing
area.
For seat sealing areas that cannot be restored by hand
dressing, a one-time machining allowance of 0.010 inches
is provided on the overall seat cavity. This allowance may be
used on a single cavity or shared between the 2 seat cavities
(i.e. remove 0.010 inches on a body seat cavity or 0.005
inches on both the body and cap/insert set cavities).
When machining, care should be taken to keep the sealing
area flat and parallel with respect to the valve body joint and
provide a 125 RA maximum surface finish with a circular lay.
Bodies and caps/inserts that have been machined should
be stamped, “MCH” next to the valve tag to indicate that the
one-time machining allowance is no longer available for
repair of the valve.
The repair facility must use their own judgement and
experience when evaluating damage severity in sealing
areas. Metso recommends that all repairs be confirmed by
gas testing for shell and seat leakage. Metso’s recommend
gas test procedure is provided in
Section 7
.