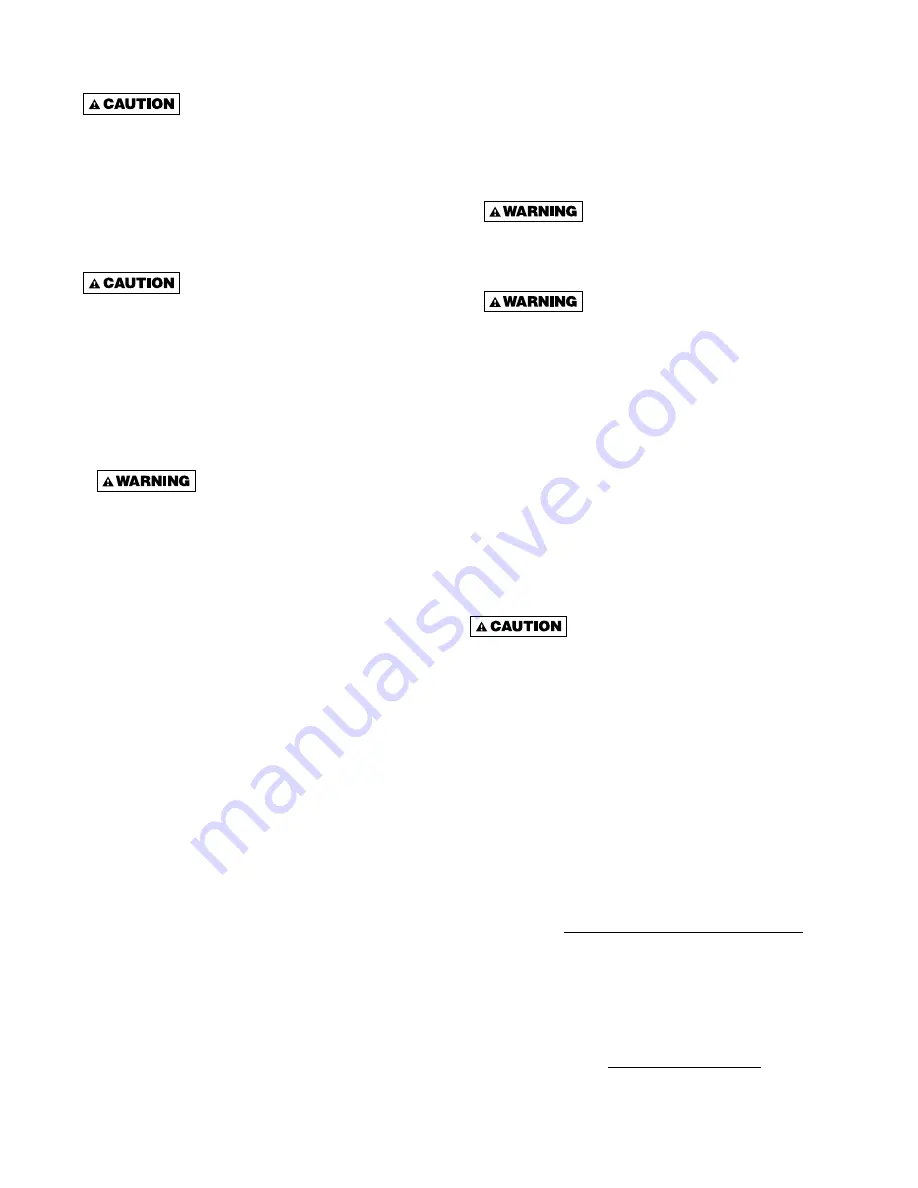
18
OPERATION
Never operate the unit beyond the
specifi ed limits or severe damage to and or premature
failure of the unit will result!
EXPLANATION OF CONTROLS (see Figure 12)
1. Each Separated Combustion Unit Heater comes
equipped with a power vent system that consists of a
power venter motor and blower, pressure switch and
sealed fl ue collector.
The addition of external draft hoods
or power venters is not permitted. Addition of such
devices may cause severe unit malfunction or failure!
2. The power venter motor is energized by the room
thermostat when a demand for heat is sensed. The
pressure switch measures the pressure differential
between the air inlet and exhaust vent systems. If
the differential is correct the indirect spark ignition
system is energized.
Under no conditions is the unit
to be fi red if the power venter is not operable or
severe personal injury or death may occur!
3. The indirect spark ignition system consists of an
ignition module, a dual combination valve, and a
spark-ignited pilot burner. When the pressure switch is
closed, the pilot valve opens as a spark is generated
to light the pilot. When the flame is sensed by the
flame sensing circuit the spark ceases and the
main gas valve is opened to supply gas to the main
burners. Once the thermostat has been satisfied,
the vent system and gas valve are simultaneously
deenergized stopping all gas fl ow to the unit.
4. The limit switch interrupts the fl ow of electric current
to the main gas valve if the unit heater becomes
overheated.
5. The fan switch delays the operation of the fan for 60
to 90 seconds once the thermostat is closed and
continues fan operation for 60 to 90 seconds after
the thermostat opens.
NOTICE: The start-up fan delay must not exceed 90
seconds from a cold start.
6. The wall ther mostat, supplied optionally, is a
temperature sensitive switch that operates the vent
and ignition systems to control the temperature of
the space being heated.
NOTICE: The thermostat must be mounted on a
vertical, vibration-free surface free from air currents
and in accordance with the furnished instructions.
INITIAL LIGHTING
1. Open the manual gas valve, in the gas supply line to
the unit heater. Loosen the union in the gas supply
line to purge it of air. Tighten the union and check for
leaks.
Check all pipe joints for leakage
using a soap solution or other approved method.
Never use an open fl ame or severe personal injury
or death may occur.
Before attempting to light or
relight pilot, wait 5 minutes to allow gas which
may have accumulated in the burner compartment
to escape.
2. Turn on the electrical power. The unit heater should
now be under the control of the thermostat. Set the
thermostat to its highest setting, the power venter
motor should start and burner ignition occur. Allow
the unit heater to operate until the fan starts then
set the thermostat to its lowest setting. The burners
and power venter motor should stop operating
immediately while the fan continues to operate until
the fan time delay times out, shutting it off. Reset the
thermostat to the desired operational setting.
CHECKING UNIT HEATER RATE
Never overfi re the unit heater, as this
may cause unsatisfactory operation or shorten the
life of the heater.
Gas appliances are rated based on sea level operation
with no adjustment required at elevations up to 2000 feet.
At elevations above 2000 feet, input ratings should be
reduced by 4 percent for each 1000 feet above sea level.
Check the input rate as follows:
1. Turn off all other gas appliances that utilize the same
gas meter as the unit heater.
2. Let the unit heater run for 15 minutes.
3. Using the gas meter, clock the time that it takes to
burn 1 cubic foot of gas.
4. Insert the time, in seconds, into the formula below.
RATE
in
= HEATING VALUE(BTU/FT
3
)(3600S/HR)
Time (s/ft
3
)
EXAMPLE: If: heating value = 1000 BTU/ft
3
time/ft
3
= 18 s/ft
3
RATE
in
= (1000 BTU/ft
3
) (3600 s/hr)
18 s/ft
3
RATE
in
= 200,000 BTU/hr
Содержание SEPARATED COMBUSTION GAS FIRED PROPELLER UNIT HEATER
Страница 10: ...10 Figure 6 ...
Страница 11: ...11 Figure 7 ...
Страница 12: ...12 Figure 8 ...
Страница 13: ...13 Figure 9 ...
Страница 30: ...30 NOTES ...
Страница 31: ...31 NOTES ...