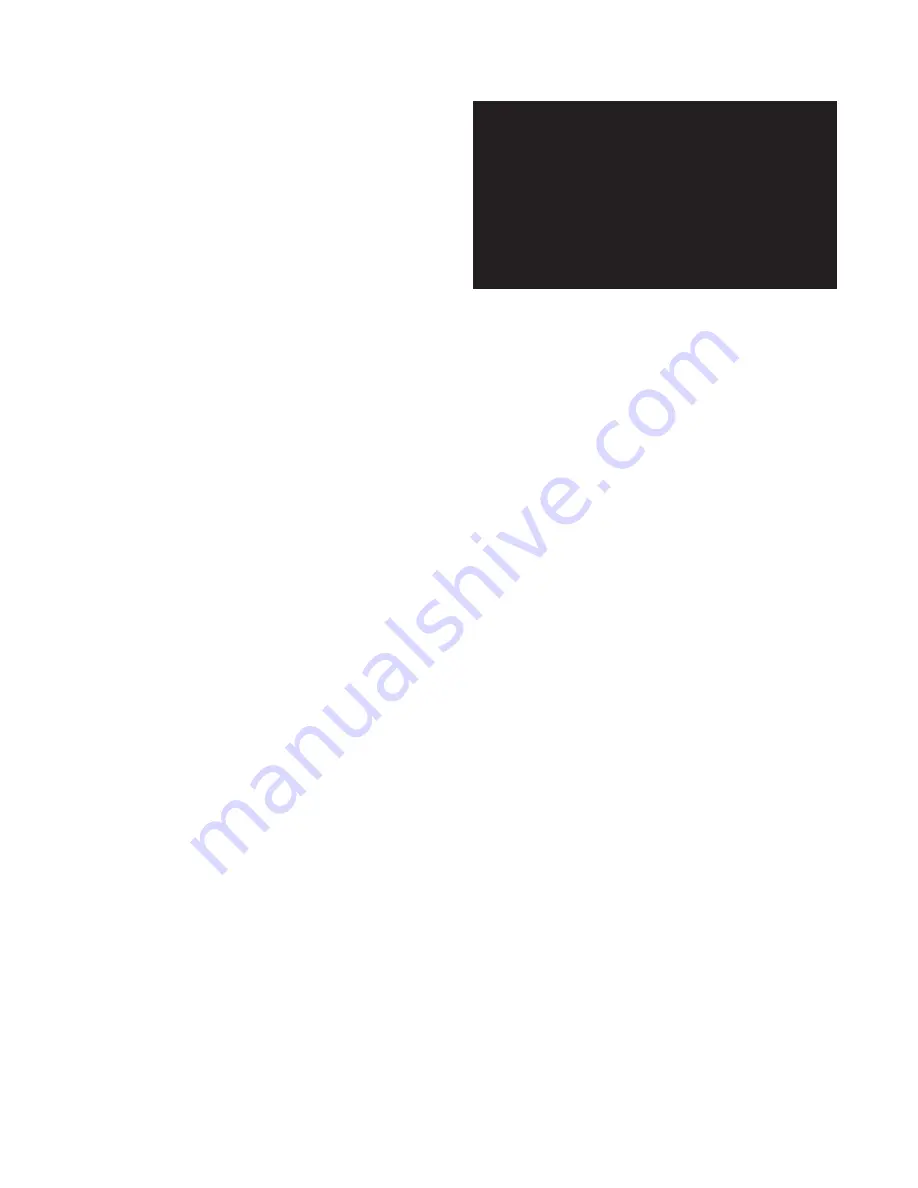
– 7 –
SECTION IV - PRE START-UP
Pre Start-Up
The owners representative or equipment operator
should be present during start-up to receive instructions
on care and adjustments of the equipment.
All equipment has been factory tested, adjusted, metered
and inspected to meet conditions set at the time the
order was placed. Only minimal adjustments should be
required. All information in this service manual is typical.
All products are semi-custom and changes may occur.
CAUTION: Line side of disconnect may be energized.
Follow proper “lockout/tagout” procedures.
Perform a visual inspection, internally and externally,
to make sure no damage has occurred, that unit is
level, and that everything is secure. This inspection is
very important and should be completed with greatest
care given to detail. A good pre-start inspection will
insure against possible unit damage on start-up and
will save valuable analysis time.
1. Check that the physical condition of the unit
exterior is acceptable.
2. Check all terminals for loose connections and
inspect all wiring terminations to insure that all
crimped connections are tight.
3. Check voltage supplied to disconnect switch; the
maximum voltage variation should not exceed ± 10%.
4. Check thermostat(s) for normal operation.
5. Check that system duct work is installed and free
from obstructions.
6. Check that the area in and around the unit is clear
of debris or containers of flammable liquids.
7. Check that all piping connections, particularly
unions, are tight and installed correctly.
8. Check that all accessories requiring field wiring
have been properly installed and wired.
9. Do not run the pump without water in the sump of
the direct evaporative cooling section.
10. All float and liquid levels and bleed off rate are pre-
set at the factory during final equipment testing and
quality control inspection. However, these settings
should be verified at the job site.
11. Depending on local water pressure, a pressure
regulating valve may be required to stabilize the
make-up water flow and the operation of the
water fill and level control valve in the unit’s direct
evaporative section.
This equipment has been tested prior to shipment.
However, during transit control setpoints can change,
and wiring can come loose. Do not assume controls
are defective until all associated setpoints and wiring
are checked.
SECTION V - UNIT START-UP
WARNING: During installation, testing,
servicing and troubleshooting of this product,
it may be necessary to work with live electrical
components. Have a qualified licensed
electrician or other individual who has been
properly trained in handling live electrical
components to perform these tasks. Failure
to follow all electrical safety precautions when
exposed to live electrical components could
result in death or serious injury.
Make sure all doors and service panels have been
closed or replaced.
A. UNIT START-UP
After completing all prestart-up checks and proce-
dures, the unit may now be operated. The following
checks and adjustments should be made during the
initial start-up:
1. Turn on pump motor disconnect and check for
proper operation of the water distribution system.
2. Measure the pump motor voltage and amperage
to ensure proper operation. The readings should
fall within the range given on the unit nameplate.
If voltage is over ± 10% of nameplate rating, notify
contractor or power company.
3. Turn disconnect switch on.
B. COOLING OPERATION
The evaporative cooling module works by drawing out-
side air through specially designed cooling media. Due
to the media’s unique design, a turbulent mix of air and
water is created which optimizes heat transfer. An air
washing effect is also created which removes most
dust and dirt from the airstream providing a clean, cool
environment.
1. Turn optional system switch to the Cool position.
2. Adjust water regulator valve: