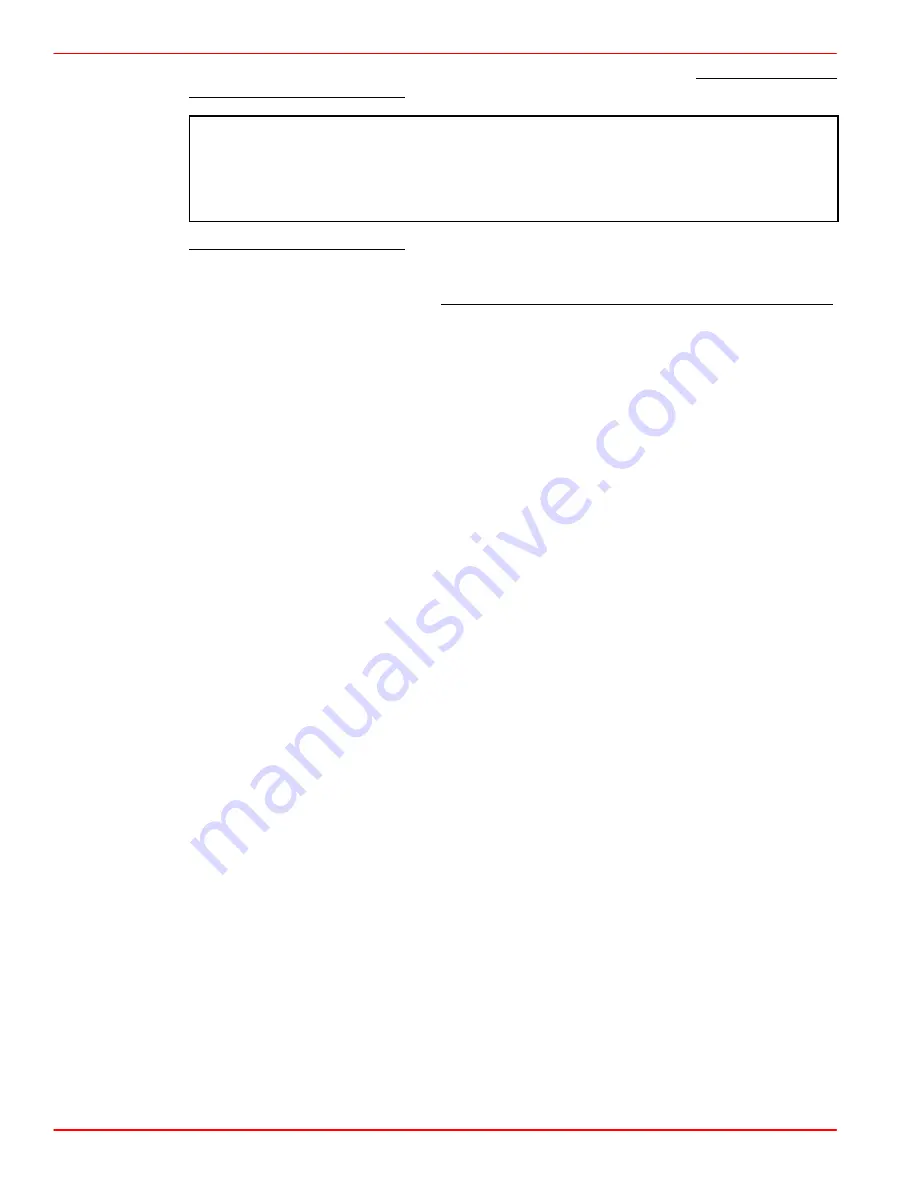
D7.3L D-TRONIC DIESEL ENGINES - BRAVO MODELS
Page 10 of 90
Multiplying the engine air flow (cfm) by 0.1 will
generally determine the combustion air vent
size requirement (per engine). Therefore:
Engine Combustion
Air Flow (cfm)
X
0.1
= Combustion Air Vent Area Per Engine
(Square Inches)
OR
Engine Combustion Air Flow (m
3
/min.)
X
22.8
= Combustion Air Vent Area Per Engine
(Square Centimeters)
D7.3 D-Tronic Example:
1000
X
0.1 = 100 Square Inches
1
OR
28.2
X
22.8 = 642.9 Sq. Cm.
1
1
: For engine combustion air only -
NOT
total engine compartment ventilation requirement.
IMPORTANT: The amount of vent area required, according to Boating standards
(NMMA, ABYC, etc.) and Coast Guard regulations, for
complete (total) engine
compartment ventilation must include the engine vent area, determined by the above
formula, plus the engine compartment ventilation requirements.
Compartment Temperature - Specifications
Too high an inlet air temperature lowers the engine performance. Therefore:
Engine compartment temperature shall not exceed outside air temperature by more than
30
°
F (17
°
C).
Since many factors influence engine compartment temperature, temperature measure-
ments should always be carried out.
Compartment Temperature - Testing
Test as follows:
1. The boat being tested shall be a standard production boat fitted as it would be for deliv-
ery to a dealer.
2. Temperature test meter used shall be of the type that can be read without opening the
engine cover.
3. During the test, in Step 4, engine compartments are to remain closed. No outside air is
to be forced into the engine compartment during the test and the bilge blower should not
be running.
4. Engine Running and Heat Soak Test:
a. Use 1 meter and 1 thermal couple. Position the thermal couple at the engine air inlet
(air filter).
b. Start engine to warm it up. After engine is at its normal operating temperature, run
engine at WOT rpm for 20 minutes. Record temperature readings at 5 minute inter-
vals.
IMPORTANT: If the temperature at the engine air inlet (air filter) exceeds specifica-
tions, the engine compartment will need additional engine combustion air openings,
or an increase in engine compartment ventilation area, until the temperature remains
within specification.