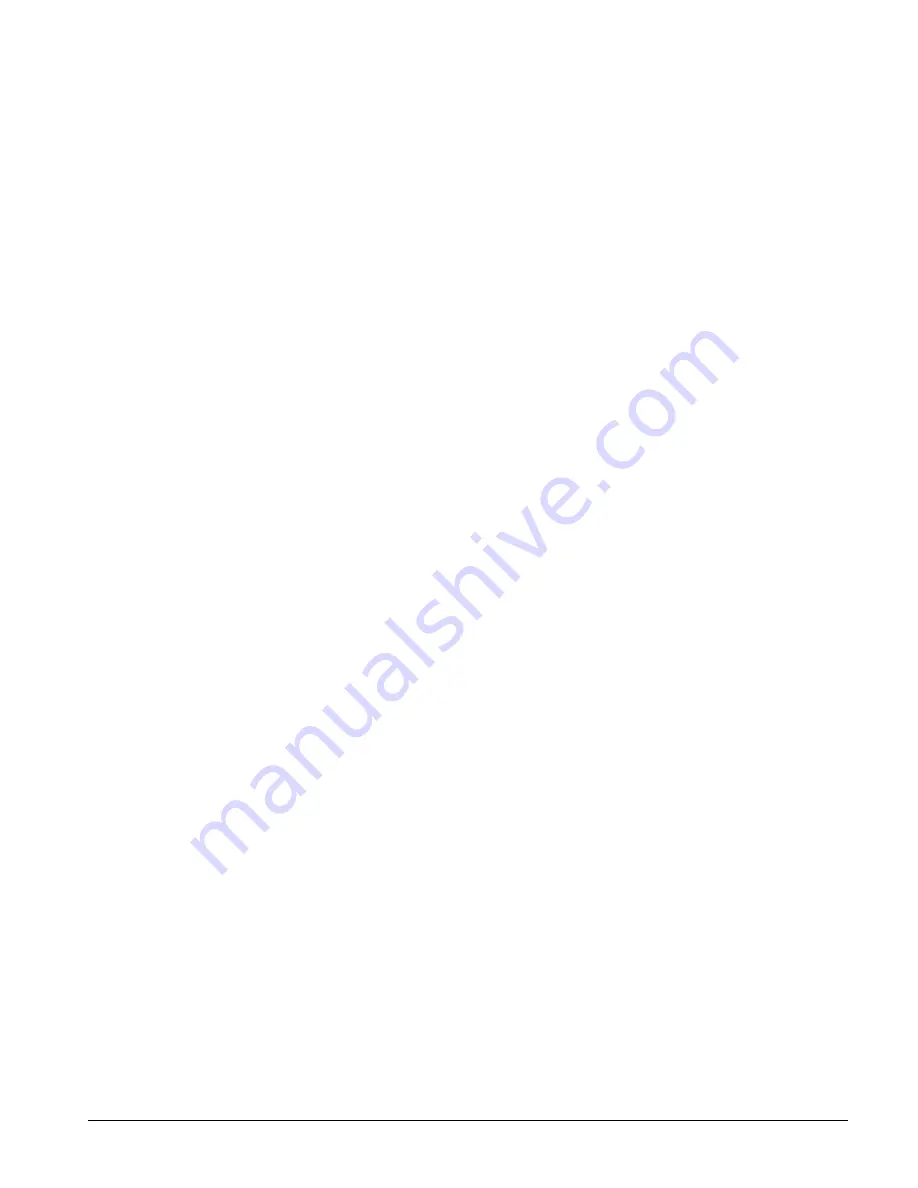
IM 1128-2
7
8.
Figure 6
) using the same procedure as the liquid injection line.
9.
Piping for the optional hot gas bypass is shipped mounted on the unit except for models WSC100,
WSC113 and WSC126 with vessel stacks sizes E36C30, E36C36, E42C36, E42C42, E48C42 and
E48C48. These units have the piping assembly shipped loose for field mounting. See Figure 7.
10.
Install the compressor lubrication lines. There are four lines as shown in
11.
Figure
8
:
a.
Thrust pump return, injects lubricant from the compressor thrust pump (thrust bearing) into the
lubricant supply line.
b.
Oil drain, drains lubricant from the compressor to the sump.
c.
Vent line, vents refrigerant from the sump back to the compressor suction.
d.
Oil supply, supplies lubricant from the pump in the sump to the compressor.
There is a variety of fitting types employed on the oil lines. Reconnect the compression fittings, bolt
on the flanges using new gaskets furnished, and re-sweat the sweat connections.
12.
Install the four-way solenoid on the compressor suction housing.
13.
Install compressor wiring using Figure 9 (including notes) as a guide. Figure 9 shows connections for
both Type I and Type II arrangements. Only the connections listed below are required to be made for
Type I. The wire end that has been disconnected, and its attachment point on the compressor, will each
have a label attached (VC for the vane close switch, for example) for matching purposes.
a.
Guardistor
, G1 (and G2 on some units), terminal box located on side of motor housing.
b.
Compressor heaters, CP1 (and CP2 on some units), located on the bottom of the compressor.
c.
Vane load/unload solenoids, SA and SB, located on the four-way solenoid assembly.
d.
Vane close switch, VC, located on compressor next to the discharge housing.
e.
Vane open switch, VO, located on suction end of compressor.
f.
High pressure switch, HPS, located on compressor discharge nozzle.
14.
If the unit has been ordered with a starter or VFD as unit mounted, brackets for mounting it and
interconnection cables to the compressor motor will be included as ship loose items. Control wiring as
shown in Figure 9 and Figure 13 (field wiring diagram), will also be required. The field wiring
diagram located on the control panel door should also be consulted as it will be current. If the unit has
a free standing starter, use normal field procedures for mounting and wiring.
Normal procedure of leak testing, triple evacuation, and charging with refrigerant and lubricant must be
followed prior to the start up procedure.
15.
Insulate the compressor motor, suction line, and other miscellaneous areas with the included insulation
and adhesive after leak testing. See Field Insulation Guide on page 29.
This completes the reassembly procedure.
Содержание WMC-B 145D
Страница 17: ...IM 1128 2 17 Figure 18 Unit panel wiring and connections Figure 15 Unit panel detail ...
Страница 25: ...IM 1128 2 25 Figure 18 Compressor Control Box ...
Страница 26: ...26 IM 1128 2 Figure 19 Unit Control Box ...
Страница 27: ...IM 1128 2 27 Figure 20 Flow Switch Wiring ...
Страница 28: ...28 IM 1128 2 Unit Photographs Figure 21 WSC 087 Photo Figure 22 WSC 100 Photo ...
Страница 29: ...IM 1128 2 29 Figure 23 WSC 126 Photo ...
Страница 31: ...IM 1128 2 31 Field Insulation Guide Figure 24 Insulation Requirements ...
Страница 32: ...32 IM 1128 2 ...
Страница 51: ...IM 1128 2 51 Figure 32 Type IV Liquid Line Removal Figure 33 Type V Liquid line Removal ...
Страница 52: ...52 IM 1128 2 Figure 34 Type V Vessel Separation ...