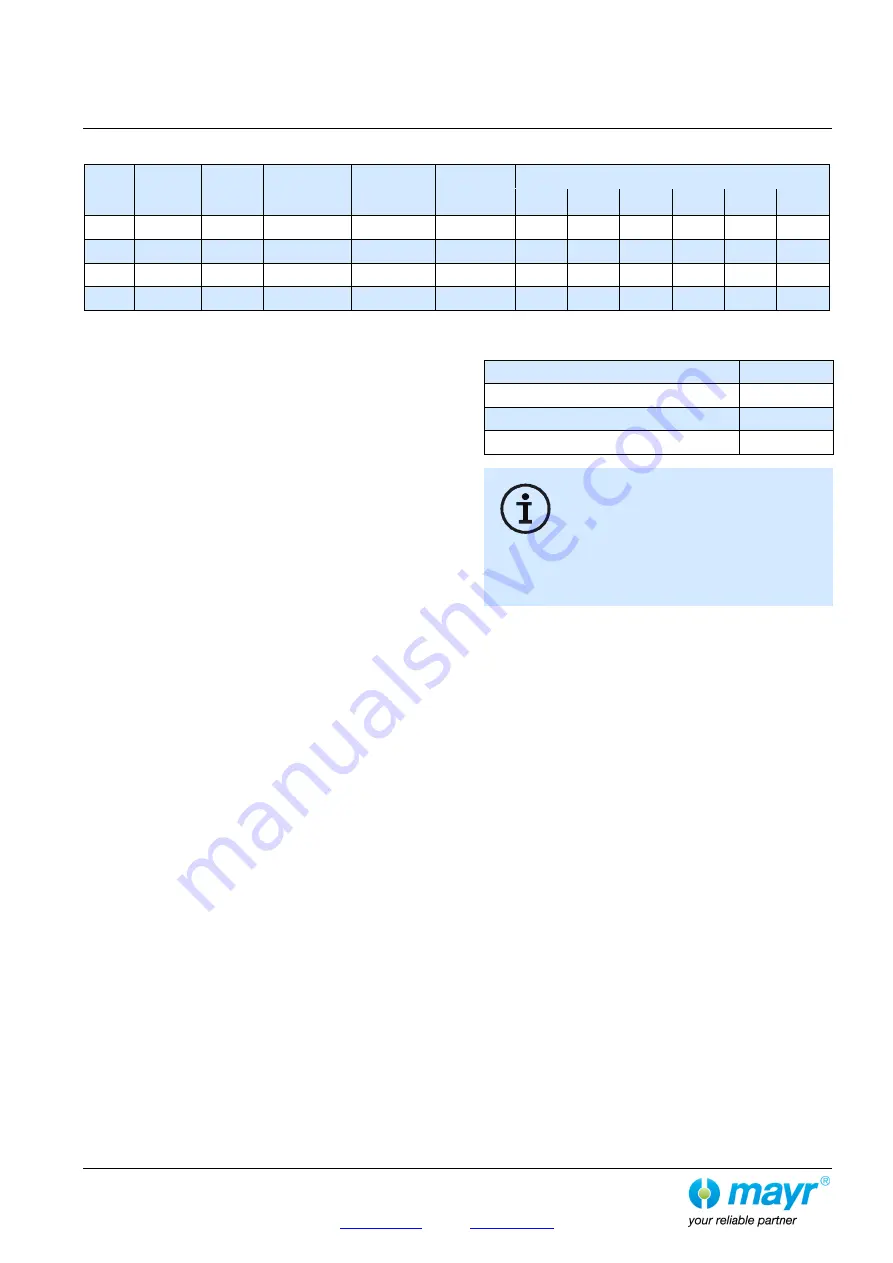
Installation and Operational Instructions for
EAS
®
-HT clutch Type 405_._ _400
Sizes 7
– 10
(B.4050.1.EN)
16/04/2019 TK/GH/SU
Chr. Mayr GmbH + Co. KG
Eichenstraße 1, D-87665 Mauerstetten, Germany
Tel.: +49 8341 804-0, Fax: +49 8341 804-421
Page 9 of 9
Table 3: Technical Data and Screw Tightening Torques
Size
Air gap
a
1
[mm]
Dimension
p
[mm]
Bolt
pre-tension
[mm]
Max.
radial forces
[kN]
Max.
axial forces
[kN]
Screw tightening torques [Nm]
Item 6
Item 8
Item 16 Item 20 Item 24 Item Z
7
2
8.0
0.5
+0.2
22.5
16
44
9
160
160
32
9
8
2
8.0
0.5
+0.2
30
21
76
9
240
240
32
9
9
2
8.0
0.5
+0.2
45
31.5
182
9
240
240
32
9
10
2
10.5
0.6
+0.2
60
42
182
19
490
490
63
9
Maintenance and Maintenance Intervals
Re-greasing of the overload elements (2), the bearing, the
thrust pieces (4) and the ball bearing track via the cone
lubricating nipples (Items 11, 12 and 13 / Fig. 3) at least
every 20 overload occurrences or 1x per year, see Table 4.
Maintenance work, which should be carried out after approx.
2000 operating hours, after 100 disengagements or at the
latest after 1 year, includes:
Visual inspection
Functional inspection
Inspection of the shaft-hub connection
Inspection of the screw tightening torques
The specified tightening torques (see table 3) must be
maintained.
Inspection of the set torque
Clutch release inspection
Inspection of the bearing or bearing pre-tension
Re-greasing of the overload elements (2) via the cone
lubricating nipples (11) on each overload element (2),
see Fig. 3.
Re-greasing of the bearings via the cone lubricating
nipples (Item 12 / Fig. 3) in the pressure flange (3),
2 x 180° offset.
Re-greasing of the thrust pieces (4) and the ball bearing
track via the cone lubricating nipples (Item 13 / Fig. 3) in
the pressure flange (3), 2 x 180° offset.
Clutch re-greasing must only be carried out by specially
trained personnel.
For greasing, please use NLGI Class 1.5 grease with a basic oil
viscosity of 460 mm
2
/s at 40 °C, e.g. Mobilith SHC460.
When re-installing the clutch, please secure all screws with
Loctite 243 (medium hard).
If large amounts of dirt or dust are present or in extreme ambient
conditions, it may well be necessary to carry out inspections at
shorter intervals.
We recommend that maintenance work is carried out at the
site of manufacture.
Table 4: Greasing
Lubrication points
Quantity
Item 11
2 ccm
Item 12
8 ccm
Item 13
10 ccm
On balanced clutches, please observe:
Maintaining the exact angular position between
the clutch components is absolutely necessary
for maintaining the balance quality.
On balanced clutches, the components are
therefore marked and are, on re-installation, to
be screwed together again in the
marked
angular position
to the tightening torque
according to Table 3.
Disposal
Electronic components
(Limit switch):
Products which have not been disassembled can be disposed of
under Code No. 160214 (mixed materials) or components under
Code No. 160216, or can be disposed of by a certified disposal
firm.
All steel components:
Steel scrap
(Code No. 160117)
Seals, O-rings, V-seals, elastomers:
Plastic
(Code No. 160119)