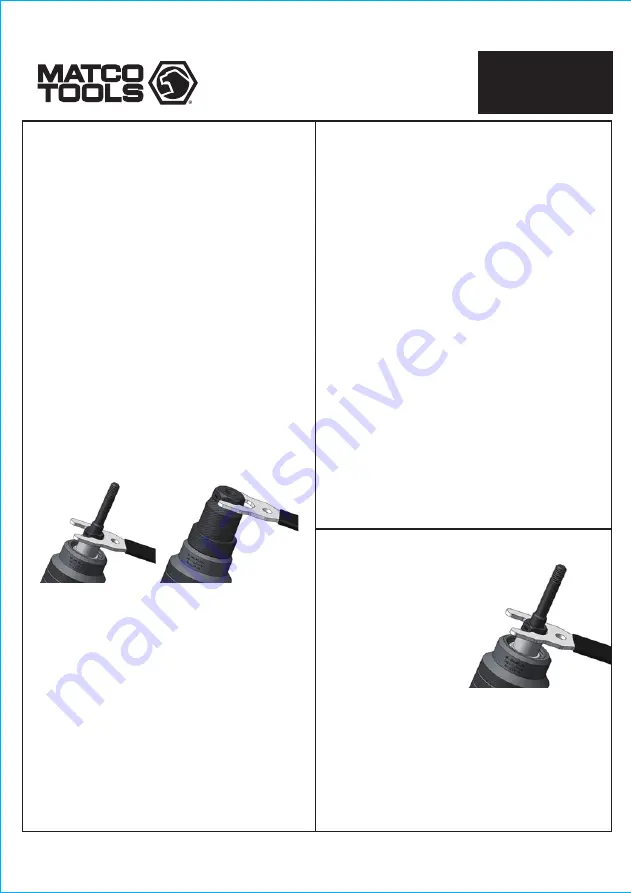
lll. OPERATION GUIDE:
lV. MAINTENANCE:
1. The nut riveting adapter is
lubricated before shipping.
Recommended: cleaning
the components of plunger
tube, and using lubricant
grease to re-lubricate its
parts on at least a yearly
basis.
2. Threaded mandrel
replacement:
life span of threaded mandrel varies with usage
frequency and the uses of different rivet nut
sizes/types. Recommended: replacing the threaded
mandrel with new spare and its nosepiece before it
is worn-out.
WARNING: WEAR WORK GLOVES (RUBBER COATED
PREFERRED) FOR GRIPPING THE ADAPTER
IMPORTANT
: Ensure the threads on mandrels are clean
and the loaded rivet nut has full thread engagement with
threaded mandrel during riveting. It is strongly
recommended to clean and lubricate (ex. silicone spray,
dry lube) the threads on mandrels before and after use.
CRITICAL
: Before using the tool on your intended work
piece, it is REQUIRED that you test the tool with a rivet nut
on a test piece to determine the adequate torque needed
for your rivet nut size, rivet nut material, and sheet metal
thickness and material.
• Ensure drill is in "driver" mode and not drill mode.
Different drills will require different torque, limiting
settings for the same material.
• On the test piece, set your drill to a low clutch setting and
work up to higher settings until the torque level is enough
to fully set the rivet nut but not over set. WARNING: Over
setting rivet nuts may permanently damage the mandrel
or tool.
• Once the torque level is determined, test again on a new
hole at your intended setting to confirm. The knurled part
of the rivet nut should look mushroomed, starting to
become flat on the other side of the work piece and
should not rotate when you install a bolt.
2.4 Ensure the rivet nut has adequate engaged thread
and that there is no cross threading. Check and
confirm the objects to be riveted are SECURE.
2.5 Some small amount of clearance between nose
piece and the flange of rivet nut may be beneficial to
operation, but keep adequate thread engagement on
the nut.
2.6 Refer to Section III. for determining the proper drill
torque settings (REQUIRED).
2.7 Put the fully threaded rivet nut onto the tools
mandrel into the proper size hole (see Sizing Chart
on page 2).
2.8 Align the adapter with the hole angle as best you
can. While gripping the adapter firmly with one
hand (wear work gloves), operate the drill in the
FWD direction until you feel or hear the drills torque
clutch catching. The adapter should not rotate while
the drill is working. Release your grip on the adapter
and reverse the drill out of the rivet nut. Depending
on the material, you may need to manually help the
adapter thread out of the rivet nut with your off
hand.
Tip 1: If setting M10 or 3/8" and especially on stainless,
high grip strength is required. Not all rivet nuts are the
same--some require more force.
Tip 2: Make a note of the torque setting of your
application for future use.
1. Tool Installation:
Install a new mandrel and nosepiece to match your
intended rivet nut thread size. Use the included wrench to
install the new mandrel into the #2 Plunger Tube. Ensure
that the mandrel and other components are tightly fixed in
position. After installing the front bushing cover and lock
bushing, lightly tighten the new nosepiece onto the end of
the tool. Install the hex shank drive end of the tool into
your drill and affix tightly into its chuck.
2. Riveting:
2.1 While holding the adapter with your hand (
WEAR
GLOVES
), operate the drill in the REV direction until
you hear the adapter start to click. This means it has
fully exposed the mandrel.
2.2 Switch the drill to the FWD setting.
2.3 Manually thread the selected rivet nut onto threaded
mandrel or hold the rivet nut in one hand and use
another hand to pull the drill trigger slightly to have the
nut threaded on by the tool.
RIVET NUT
ADAPTER KIT
RN9
Página 3
1802030-14