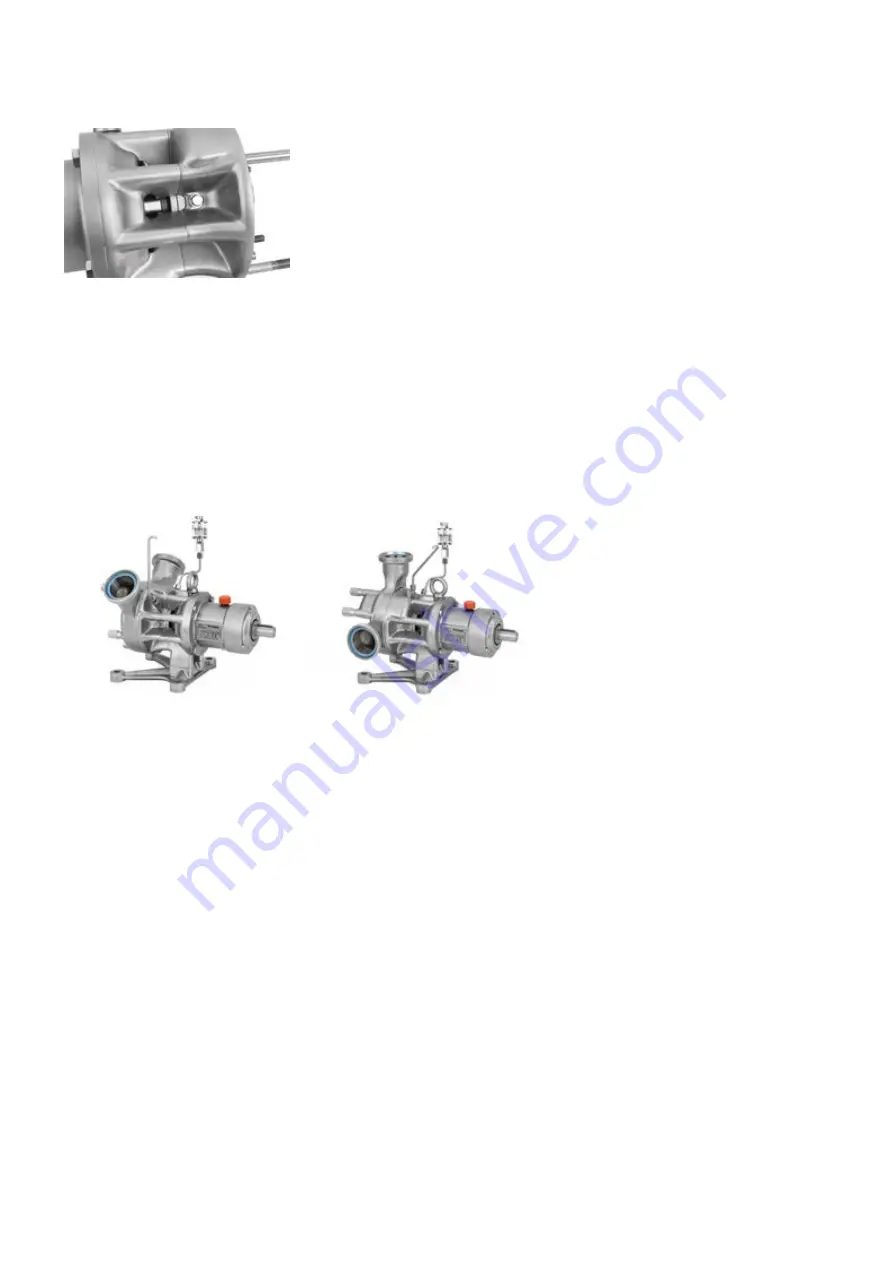
Plug all other possible connections on the frame, using the
threaded plugs supplied with the pump (see "Parts lists" on
page 43 for the part numbers). The other connections are
intended for use with different orientations of the pump's
nozzles (see "Possible pump orientations" on page 17).
14.2 Static flushing device
Before commissioning, fill the flushing device (if supplied) with a suitable flushing fluid, depending on the
product being pumped. Fill the sight glass with flushing fluid until the fluid level is just below the bend in
the outlet pipe.
Fitting the static flushing device
The static flushing device can be fitted to a Certa Plus pump with a flush ring or a double mechanical
seal. See also "Assembling the pump head" on page 34.
The connection with the vent pipe must be connected to the highest flush port.
l
For a 10/2 nozzle orientation this is the flush port located 45° off the vertical axis.
l
For all other nozzle orientations this is the flush port on top of the pump.
The connection with the sight glass must be fitted to the flush port which is offset by 45° from the
vertical axis.
Remove the threaded plug of the required flush port by using a 10mm Socket with extension.
Apply an appropriate sealing material (e.g. Teflon tape) to both threads of the double nipples and fit
them to the flush ports using a 14mm spanner.
Connect the sight glass and the vent pipe with the installed connectors using two 14mm spanners to
tighten them.
Check if the reservoir and the vent pipe are at the same height and close all flush ports.
Removing the static flushing device
The static flushing device must be emptied and removed before disassembling the pump. To do this,
open the flush port at the lowest point of the pump.
After the flushing device has been emptied, reverse the sequence of operations described above to
remove it.
14.3 Fitting a flush ring
See "Assembling the flush ring of a single mechanical seal system" on page 37.
20
m-certa-plus-en-02