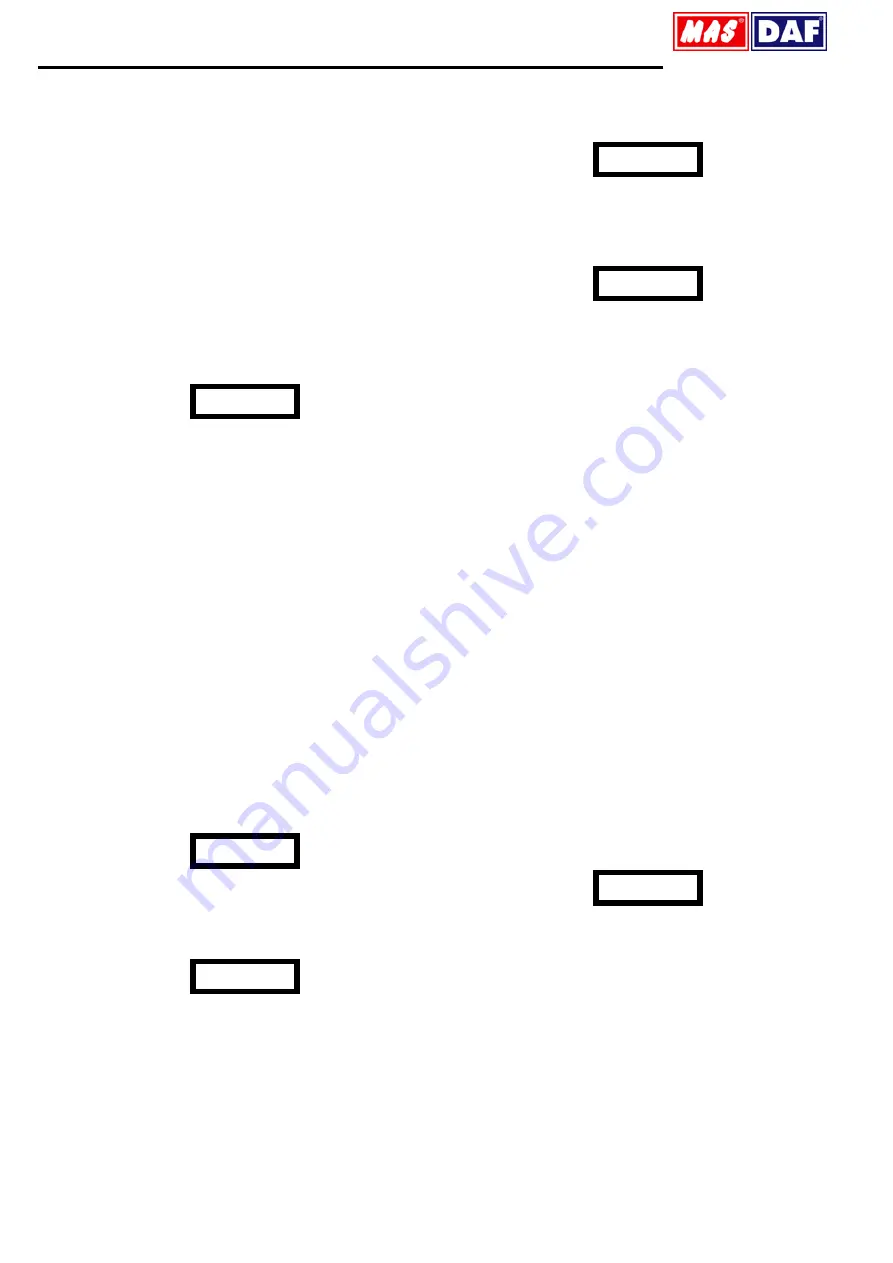
Mas Grup
6
7. COMMISSIONING, START UP AND OPERATING
7.1. Preparations Before Start Up
OIL CHECK:
ENM type pumps are provided with self-greased rolling
bearings requiring no servicing in life long. Therefore, it is not necessary
to check the oil.
Check pump seals
Make sure that the pump and the suction pipe is completely filled with
water before the starting. If the pump operates on a positive suction
head, no problem will be encountered. Suction valve is opened and air
drains are un-tightened.
Pumps with foot valve are filled with water by opening the pump filling
tap or, one takes advantage of the water accumulated in the discharge
pipe and by using a small valve the check valve is bypassed and the
pump is filled.
In vacuum pump driven pumps, by operating the vacuum pump one
achieves to fill the pump via increasing the water level in the suction
pipe.
CAUTION
Do not start your pump dry (WITHOUT WATER).
7.2. Start up Procedure
Check if the suction valve is open and the discharge valve is closed.
Start the motor
Wait until the motor reaches sufficient speed. (In Star-delta
connections, wait until the engine passes to delta connection.)
Keeping an eye on the amperage shown on the panel, open the
discharge valve slowly.
In the primary operation, if the discharge pipe is empty, do not open the
valve completely. By keeping an eye on the amperage, open the valve
with care regarding that it should not exceed the value indicated on
p
ump’s label.
After opening the valve completely, check the pressure from the pump
exit manometer and make sure that this value is the pump operating
pressure value and is indicated on pump’s label.
If the value one reads is less than the pump label value when the valve
is completely open, it means that the height is miscalculated. Increase
the value by narrowing the valve and bring it to pump’s label value.
If the value one reads is greater than the pump label value when the
valve is completely open, it means that the height is calculated less
than what it should be in reality. The device is pumping less than what
is requested. Check the installation and the calculations.
Minimum flow rate:
If the pump is working with zero flow rates (closed
valve) from time to time during its operation, the water inside the pump
may endanger the pump by getting warmed up. In such cases, a
minimum flow valve must be connected to the pump exit.
CAUTION
Stop the motor if the pump gets too hot. Wait until it gets cold.
Then start the system up again carefully.
7.3. Shut Down Procedure
CAUTION
During sudden start ups and stops, a pressure reducing valve must be
placed at the exit section of high flow rate pumps whose discharge
pipelines are long, in order to reduce water hammer effect. Water
hammer may explode the pump.
In normal conditions (apart from sudden power shut down, etc), stop the
pump as below:
•
Close the discharge valve slowly
•
Switch the power off, stop the motor. Notice that the rotor slows down.
•
Do not start up the motor at least before 1 to 2 minutes.
•
If the pump will be out of use for a long time, close the suction valve
and auxiliary circuits. If the pump is outside and if there exists a danger
of frost, remove all drain taps and empty all the water inside the pump.
(5.2. Storage)
CAUTION
If the pump is outside and if there exists a danger of frost, remove
all drain taps and empty all the water inside the pump.
8. MAINTENANCE
CAUTION
Maintenance operations must be done by authorized personnel with
protective clothing only. The personnel must also beware of high
temperatures and harmful and/or caustic liquids. Make sure that the
personnel read carefully the manual.
•
The instructions in Safety Precautions must be executed during
maintenance and repair
•
Continuous monitoring and maintenance will increase the engine’s and
pump’ s lives.
The instructions below should be applied.
8.1. The Checks During the Operation
Pump must never be operated without water.
Pump must not be operated for a long time with the discharge valve
closed (zero capacity).
Bearing temperature must never exceed 80
C if the ambient
temperature is 30
C
Precautions must be taken against flare up when the component
temperatures are over 60
C.
“Hot Surface”
warnings must be placed
over necessary areas.
All the auxiliary systems must be in use while the pump is operating.
Gland nuts must not be tightened too much. If the amount of water
increases after a long operation time, the nuts may be tightened by 1/6
turns
If the pump has mechanical sealing, there is no need for excessive
maintenance. Water leakage from the mechanical sealing indicates the
fact that the sealing is worn out and therefore needs to be replaced.
If the system consists of a substitute pump, keep it ready by operating it
once a week. Check also the auxiliary systems of the substitute pump.
Check the elastic components of the coupling. Replace them when
necessary.
8.1.1. Component Check
CAUTION
To make possible the visual control, one must be able to reach the pump
from any direction. Especially, to be able to dismount the internal units of
the pump and the engine, sufficient free space must be created around
them for maintenance and repair. Furthermore, one must make sure that
the piping system can easily be dismounted.
8.1.2. Bearing and Lubrication
ENM type pumps are provided with two (lifelong) carefree rolling bearings
in accordance to DIN 625. The usual service life of the rolling bearings
attains at least the operating hours indicated in the technical
specifications of DIN ISO 5199.