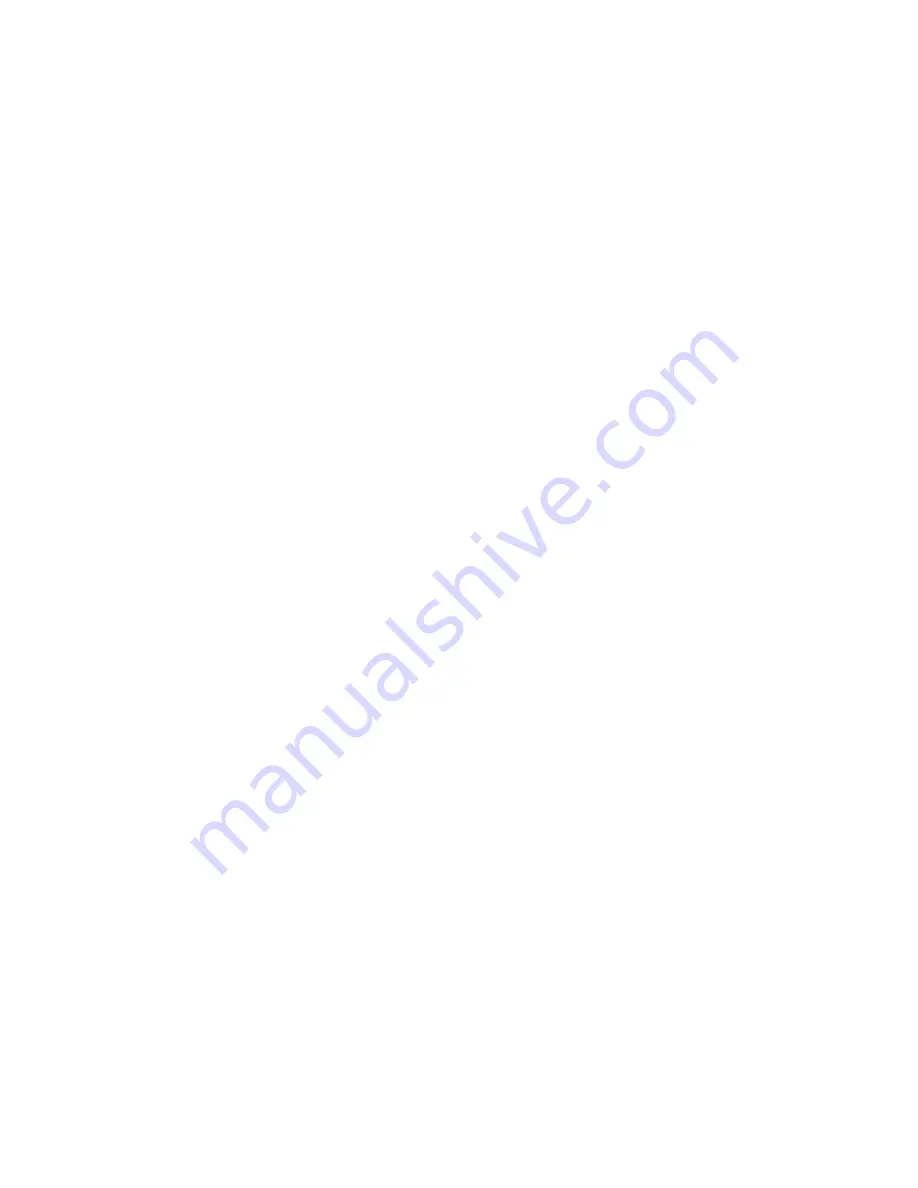
SECTION III. PREPARATION
18). Lowrangeairpressuregauge.
A. Major System Components
19). Bicycle hand air pump.
The following components comprise the R.O.
20). Small bottle of liquid chlorine bleach.
Drinking Water System. (Refer to Fig. 1. page 3
21). Graduated measuring cylinder.
for general system layout.)
up materials.
22). Paper towels, wisk broom and assorted clean
1). An R.O. Manifold assembly consisting of the
manifold, sumps, sump nuts, sump O-rings
and mounting bracket.
C. Site Selection for Maior Svstem Components
2). A Drinking Water Holding Tank.
3). An Air Gap Faucet kit.
The R.O. System was designed to fit under a
4). A self-piercing Saddie Valve kit
sink, however, because of space limitations or
5). A Drain Clamp kit.
other reasons, the system's flexible design allows
6). Plastic Tubing and tube connectors.
for other locations. When determining the loca
7). A Reverse Osmosis Membrane sealed in a
tions remember that access to a cold water tap
plastic bag.
line, the household drain, and ease of filter
8). A Sediment/Carbon Prefilter Cartridge
replacement are important considerations.
shrink wrapped.
9). An Activated Carbon Post Filter Cartridge,
shrink wrapped.
All components and tubing should be located in an
10). A T.D.S. Monitor Kit (optional*) with feed
area that does not see freezing ternperatures. If
water and product water test cells.
winter temperatures are severe, the area should
11). Other items necessary for installation may
not see temperatures below the minimum temper
include wood screws or machine screws and
ature listed in Table B page 4 for proper perfor
nuts for mounting the manifold, or concrete
mance. Do not expose unit or tubing to direct sun
anchors for hanging on basement wall, addi-
Iight.
tional tubing or tube connectors, plastic wire
ties for organizing tubing.
1.
Air Gap Faucet
- The faucet should be
* The T.D.S. Monitor may be necessary to conform to
placed near the sink where drinking water is
state or local codes, check with the local plumbing
normally obtained. Convenience of use (fill
authority.
ing of water pitchers and glasses), and an
open area beneath the faucet under the sink
B. Tools Recommended for Installation
for attaching product and drain tubing are
considerations. A 2" diameter flat surface
The following tools will cover most of the installa-
required above and below the mounting si`,
tion sites encountered:
The thickness of the mounting surface should
not exceed 1-1/4". Watch for strengthening
1). 3/8" variable speed electric drill.
webbing on the underside of cast iron sinks.
2). Extension work light with outlet.
2.
Drinking Water Holding Tank
--The Holding
3). Safety glasses.
Tank may be placed where it is convenient
4). 1-1/4" porcelain hole cutter kit.
within 10 feet of the faucet, under the sink or
5). 1-1/4" Greenlee hole punch and 1/8" and
in an adjacent cabinet are best choices. If
1/2" metal drill bits for pilot hole.
Ionger run of tubing is required, the tubing
6). Center punch and hammer.
should be the 3/8" diameter O.D. size to pre
7). 1-1/4" wood bit.
vent a high pressure drop. Remember, these
8). Concrete drill bits.
tanks can weigh up to 30 pounds when full of
9). Assorted wood and metal drill bits including
water,afirm,levelareaisrequired.
7/32" metal drill bit.
3.
R.O. Manifold Assembly
-The manifold
10). Phillips head and flat blade screw drivers.
has a reversible panel mounting bracket that
11). 1/2", 9/16" and 5/8" open end wrenches.
allows mounting on either the right or left
12). 10" Crescent wrench with jaws taped to hold
side of the under-sink area or a cabinet
faucet.
Mounting in the basement is also an option,
13). Basin wrench or 10" p~pe wrench.
one location is near the laundry/utility sink
14). Teflon tape.
where cold potable water and drain access is
15). Wide masking tape or duct tape.
handy. The mounting location should allow
will extend the life of the R O. Membrane.
adeauate clearance and accessibility for car
16). Plastic tubing cutter.
tridge changes.
17). Extra plastic tubing.
4.
Feed Water Connection
- The self-piercing
feed water shut off valve should be located
as close to the manifold assembly as possi
ble. USE A POTABLE COLD WATER SU
PLY ONLY. Softened water is preferred as
will extend the life of the R.O. Membrane.
Содержание RO-25T
Страница 16: ......