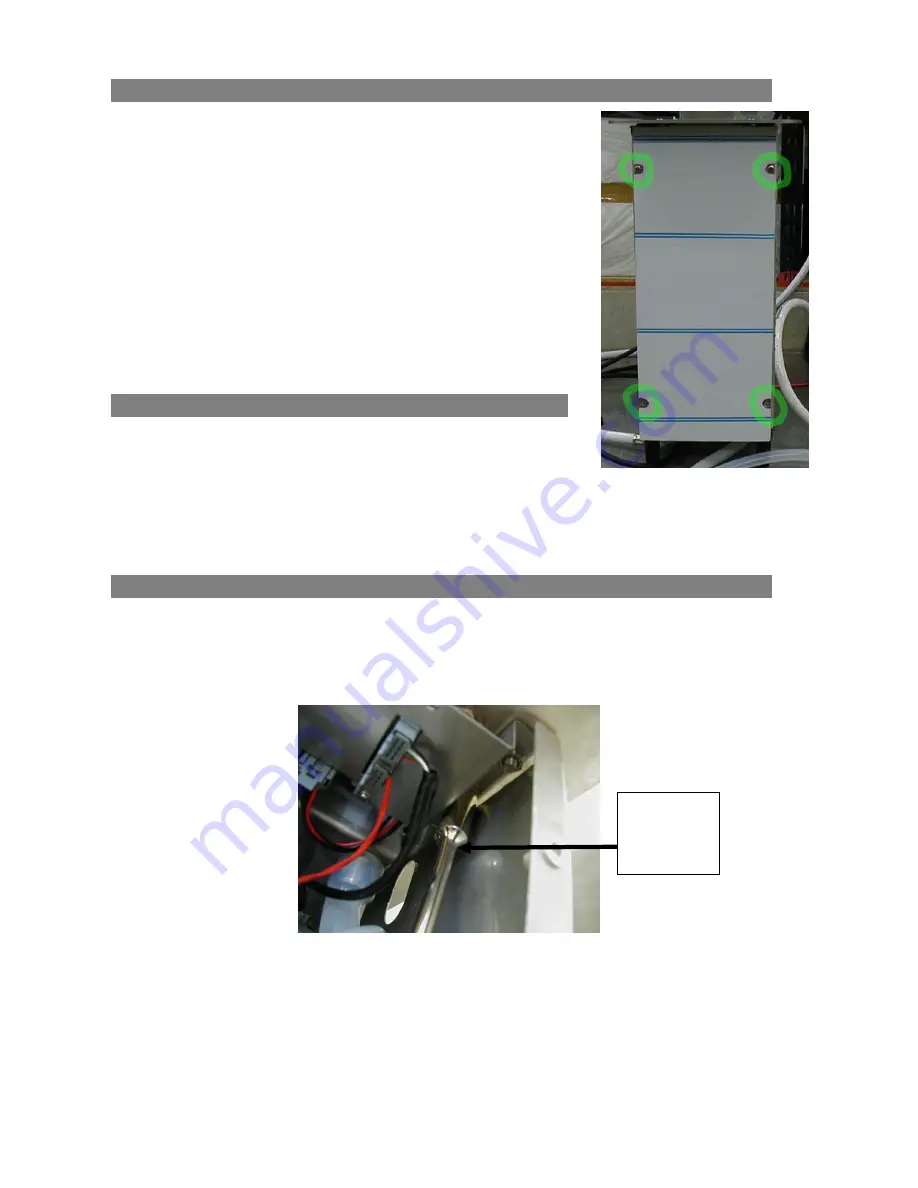
26
Service manual April 2017 Uber boiler
3.5 DISPLAY BOARD REPLACEMENT PROCEDURE
Note:
Prior to replacing the Display, it is recommended that the
current settings for the Uber Boiler are recorded so that they
may be reset with the new Display. The New Display contains
factory settings which may or may not have been changed by
the user. Special notice should be made of the Temp Offset
settings. These should be the factory settings, as they are to do
with the optimum operation of the Boiler and should not be
changed by the user.
See Service Setup Section for details of how to review the
boiler settings.
3.5.1 Disconnecting the Machine:
Turn off the machine and unplug it at the mains and allow it to
cool
completely. Remove the front service panels, unscrew the 4 screws on each panel and they
should drop off.
3.5.2 Removing and Replacing the Display Board Bracket:
Unplug all 5 connections from the PCB, you must gently push the plastic tabs back and then
pull the connections out. Unscrew the 4 M6 nuts using a 10mm socket driver, be careful as
the screen will fall away when all screws are removed.
Remove the transparent protective plastic from the PCB screen. Attach the new screen
using the same nuts making sure the orientation is the same but do not fully tighten the nuts
yet. There may have been washers on the old display bracket but these are not essential
and would be difficult to replace, so you can just use the M6 nuts.
Front Boiler panel
Access screws highlighted
10mm
Socket
Driver
Содержание Marco 1000680
Страница 7: ...7 Service manual April 2017 Uber boiler 1 1 6 Installation Template ...
Страница 8: ...8 Service manual April 2017 Uber boiler Uber Boiler Front View ...
Страница 9: ...9 Service manual April 2017 Uber boiler Uber Boiler Top View ...
Страница 10: ...10 Service manual April 2017 Uber boiler Uber Boiler Side View ...
Страница 36: ...36 Service manual April 2017 Uber boiler ...
Страница 39: ...39 Service manual April 2017 Uber boiler 4 1 Uber Boiler Functional Diagram ...
Страница 42: ...42 Service manual April 2017 Uber boiler 4 3 Electrical Schematic ...
Страница 43: ...43 Service manual April 2017 Uber boiler ...