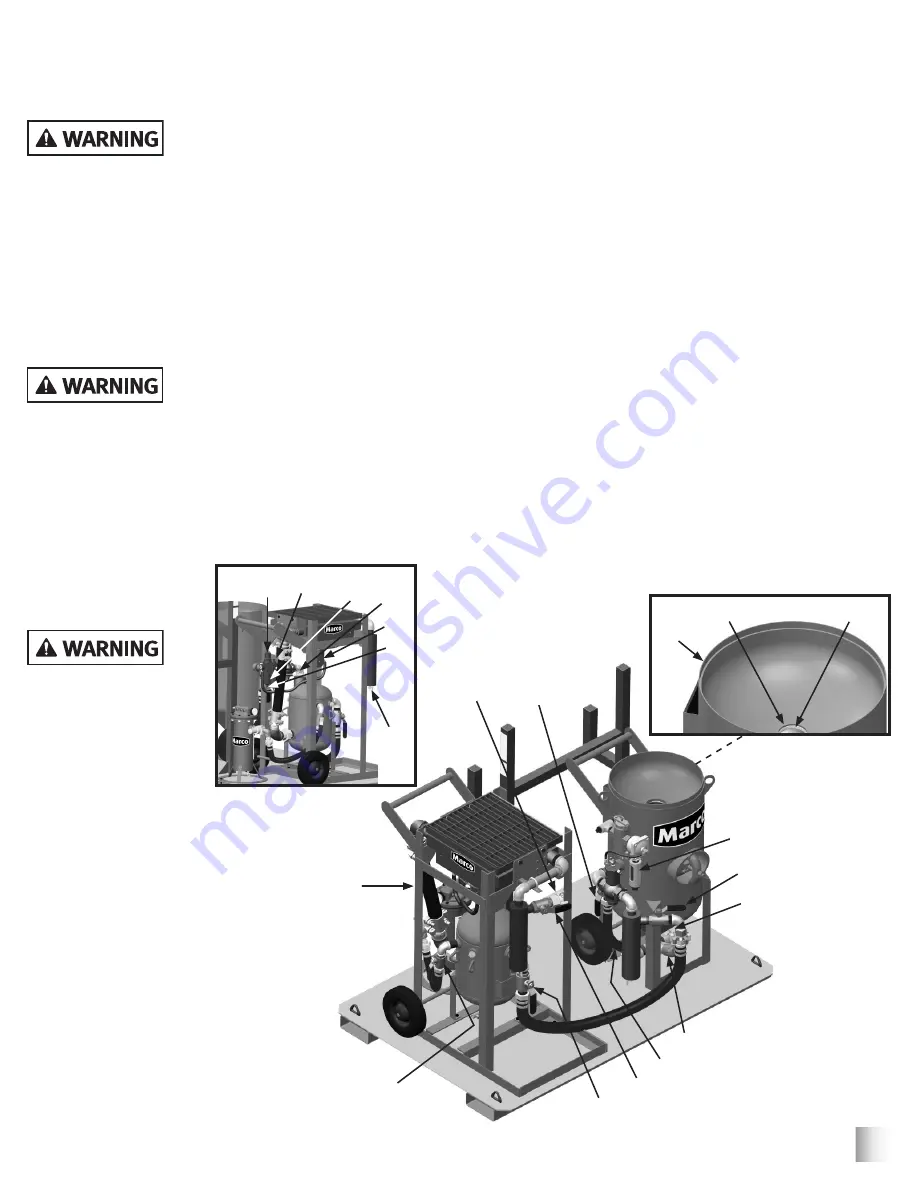
Blastmaster
®
Mobile Blasting Systems
10
OPERATING INSTRUCTIONS
Before use - AFTERCOOLER:
• Using a screwdriver or similar device, gently rotate Fan Blades to confirm free movement.
If the Fan Blades do not move freely, remove obstruction or replace Fan Blade and Motor
Assembly before use. See Aftercooler Operators Manual.
• Open Drain Valves (15,16) to release any liquid. Close Drain Valves once liquid stops
flowing.
• Fill Air Motor Lubricator (17) with SAE 10 oil or air tool anti-freeze lubricant.
• Close Ball Valves (7,11).
• Turn on compressor air supply.
• Slowly open Inlet Ball Valve (7), looking and listening for leaks.
• If leaks are found, turn off air supply, open Drain Valve (15), allow air pressure to
completely release. Repair leaks as needed.
• Slightly open Drain Valve (15) to release collected moisture.
• Slowly open Air Supply Ball Valve (18) to Air Motor (19).
• Adjust Air Motor Pressure Regulator (20) to 60 psi for proper Cooling Fan speed. Do not
exceed 60 psi.
• Watch the lubricant flow through the combination Control Knob/ Sight Dome (21) on
top of the Air Motor Lubricator, adjust the flow to one drop per minute. NOTE: Failure to
maintain lubrication will cause the motor to fail.
Always depressurize
the entire system,
disconnect all power
sources and lockout/
tagout all components
before any maintenance
or troubleshooting is
attempted. Failure to
comply with the above
warning could cause
electrical shock and
inadvertent activation of
equipment resulting in
death or serious injury.
W-562
1
2
3
5
10
7
9
11
6
8
4
13
12
14
15
16
17 18
19
20
21
This product is
not for use in wet
environments. Always
use a Ground Fault
Interrupter Circuit (GFIC)
for all electrical power
source connections.
Use of this product
in wet environments
could create a shock or
electrocution hazard.
Failure to comply with
the above warning
could result in death or
serious injury.
W-519
You must comply
with all OSHA, local,
City, State, Province,
Country and jurisdiction
regulations, ordinances
and standards, related
to your particular work
area and environment.
Keep unprotected
individuals out of the
work area. Failure to
comply with the above
warning could result in
death or serious injury.
W-503