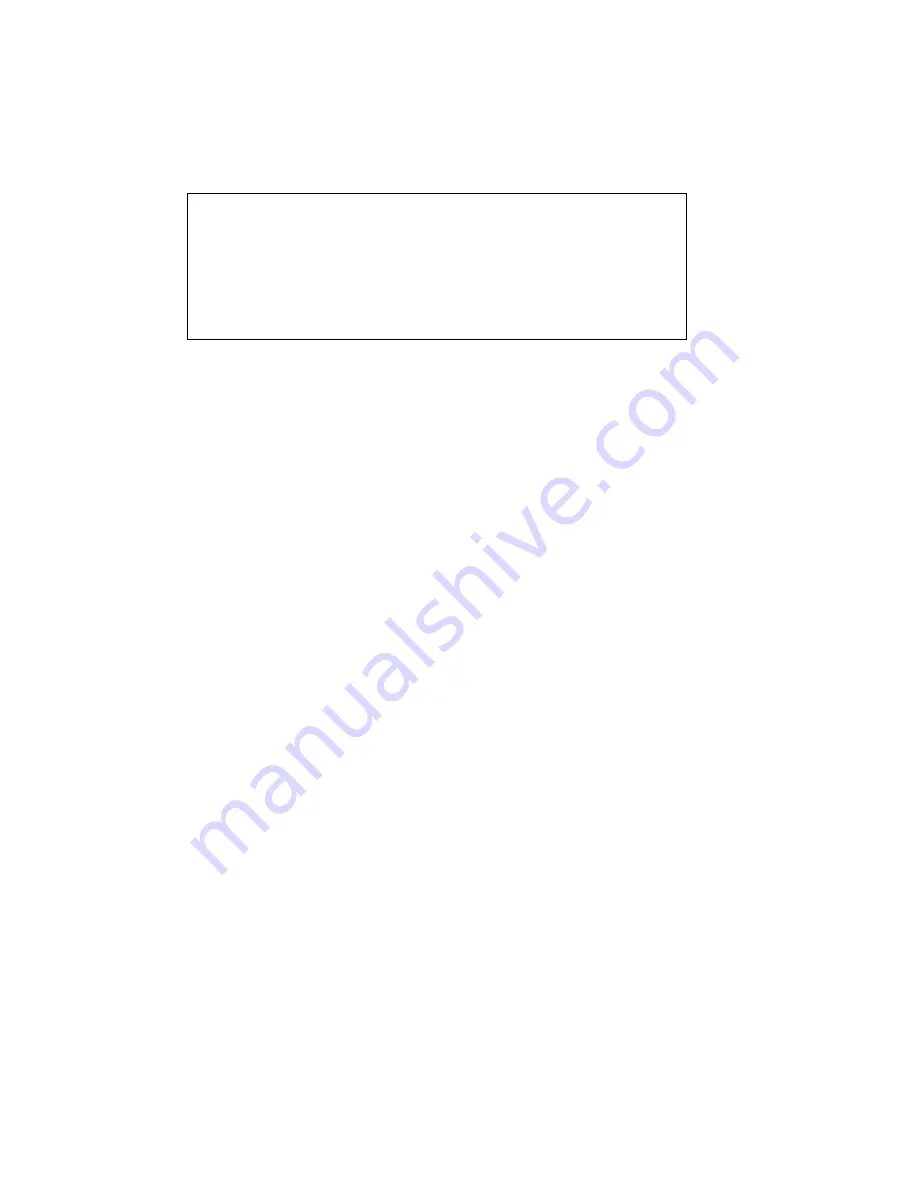
202
Part Number 80-1230-9 10/10
System Contamination Clean-Up
General
This section describes the basic requirements for
restoring contaminated systems to reliable service.
DETERMINING SEVERITY OF CONTAMINATION
System contamination is generally caused by either
moisture or residue from compressor burnout entering
the refrigeration system.
Inspection of the refrigerant usually provides the first
indication of system contamination. Obvious moisture
or an acrid odor in the refrigerant indicates
contamination.
If either condition is found, or if contamination is
suspected, use a Total Test Kit from Totaline or a
similar diagnostic tool. These devices sample
refrigerant, eliminating the need to take an oil sample.
Follow the manufacturer’s directions.
If a refrigerant test kit indicates harmful levels of
contamination, or if a test kit is not available, inspect
the compressor oil.
1. Remove the refrigerant charge from the ice
machine.
2. Remove the compressor from the system.
3. Check the odor and appearance of the oil.
4. Inspect open suction and discharge lines at the
compressor for burnout deposits.
5. If no signs of contamination are present, perform
an acid oil test.
Check the chart on the next page to determine the
type of cleanup required.
Important
Manitowoc Ice, Inc. assumes no responsibility for
the use of contaminated refrigerant. Damage
resulting from the use of contaminated refrigerant is
the sole responsibility of the servicing company.
Содержание QC0700
Страница 2: ......
Страница 12: ...12 Part Number 80 1230 9 10 10 This Page Intentionally Left Blank ...
Страница 22: ...22 Part Number 80 1230 9 10 10 This Page Intentionally Left Blank ...
Страница 36: ...36 Part Number 80 1230 9 10 10 This Page Intentionally Left Blank ...
Страница 42: ...42 Part Number 80 1230 9 10 10 This Page Intentionally Left Blank ...
Страница 80: ...80 Part Number 80 1230 9 10 10 11 Lift out ice damper 12 Lift out ice strainer ramp ...
Страница 87: ...Part Number 80 1230 9 10 10 87 9 Lift out ice damper ...
Страница 88: ...88 Part Number 80 1230 9 10 10 10 Lift out ice strainer ramp ...
Страница 89: ...Part Number 80 1230 9 10 10 89 11 Turn ice wiper counterclockwise to remove ...
Страница 93: ...Part Number 80 1230 9 10 10 93 16 Remove three thumbscrews then remove bin cover REMOVE THUMBSCREWS ...
Страница 96: ...96 Part Number 80 1230 9 10 10 19 Remove ice dispensing wheel by lifting straight out ...
Страница 97: ...Part Number 80 1230 9 10 10 97 20 Water Reservoir Cover Removal A Push up on cover to snap off ...
Страница 104: ...104 Part Number 80 1230 9 10 10 This Page Intentionally Left Blank ...
Страница 120: ...120 Part Number 80 1230 9 10 10 This Page Intentionally Left Blank ...
Страница 208: ...208 Part Number 80 1230 9 10 10 SV1406 FIG A PINCHING OFF TUBING FIG B RE ROUNDING TUBING USING PINCH OFF TOOL ...
Страница 209: ...Part Number 80 1230 9 10 10 209 This Page Intentionally Left Blank ...
Страница 211: ...Part Number 80 1230 9 10 10 211 8 6 9 3 ...
Страница 213: ...Part Number 80 1230 9 10 10 213 3 6 7 8 ...
Страница 215: ...Part Number 80 1230 9 10 10 215 3 7 6 8 ...
Страница 223: ...Part Number 80 1230 9 10 10 223 4 ...
Страница 225: ...Part Number 80 1230 9 10 10 225 4 ...
Страница 227: ...Part Number 80 1230 9 10 10 227 4 ...
Страница 228: ...228 Part Number 80 1230 9 10 10 ...
Страница 284: ...284 Part Number 80 1230 9 10 10 SN012 SN020 DRIER EXPANSION VALVE EVAPORATOR HEAT EXCHANGER COMPRESSOR AIR CONDENSER ...
Страница 288: ...288 Part Number 80 1230 9 10 10 This Page Intentionally Left Blank ...
Страница 289: ...Part Number 80 1230 9 10 10 289 This Page Intentionally Left Blank ...
Страница 290: ...290 Part Number 80 1230 9 10 10 This Page Intentionally Left Blank ...
Страница 291: ......