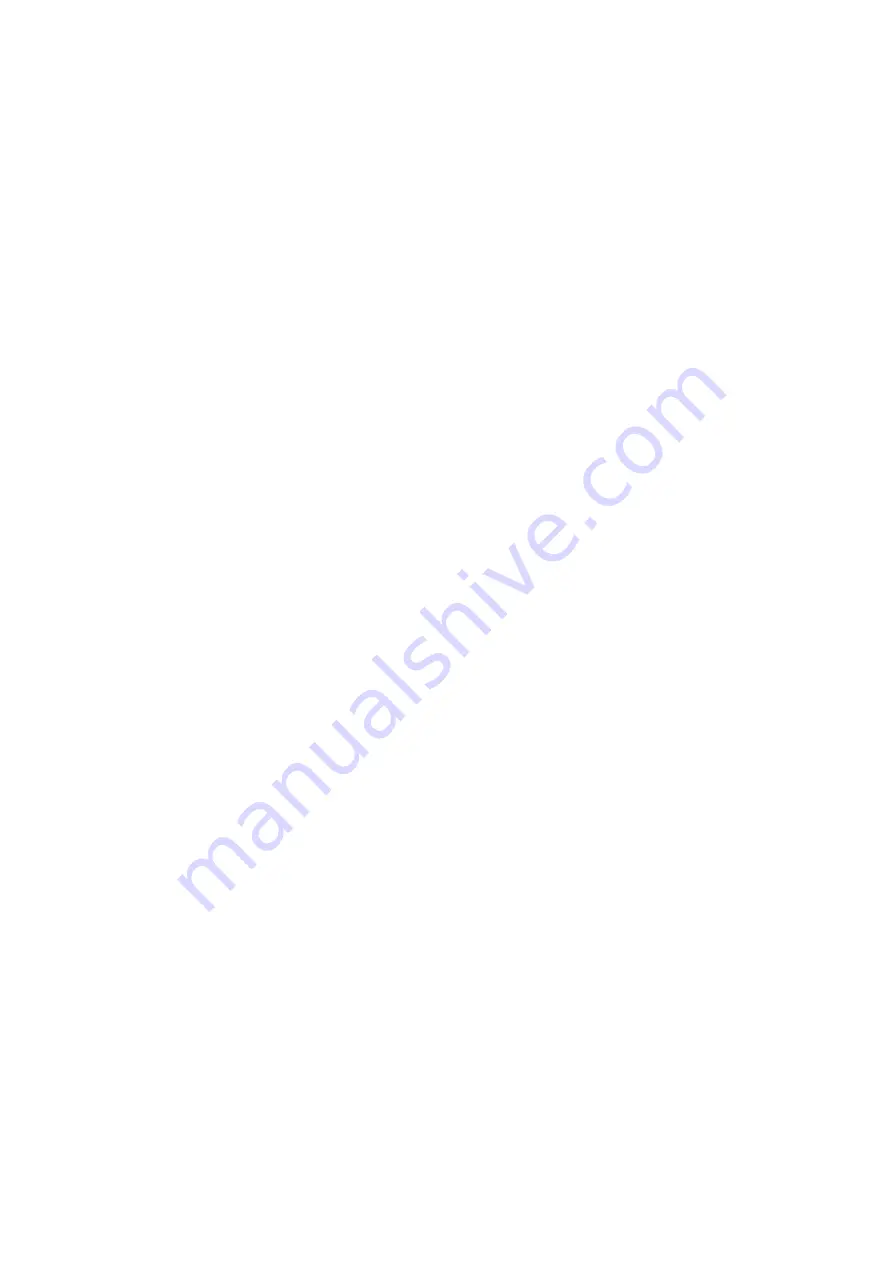
33
the amount of oil is greater or there are oil drops, shut down the implement for the period
required to repair the malfunction (damaged sealing).
Brake system (pneumatic system) maintenance
The three-range braking force distribution system is not adjustable in normal use.
It should be in the middle position. If the braking force differs from that of the tractor’s
braking force, the braking force distribution system may be adjusted to avoid incorrect
behaviour of the coupled set on the road. When making any alterations, be sure not to
cause an accident or damage to the implement.
The water condensed in the tank is drained using a valve located below the tank.
Press the pin down and water will be displaced by compressed air. When the pin is
released, the valve will automatically close. Unscrew the drain valve once a year (before
winter) and clean it.
The test of the pneumatic system consists in checking for leaks, especially at the
connection points (during the test the pressure in the system should not be lower than 6
atmospheres). Any hissing indicates the damage of hoses, gaskets and other components
of the system. In the case of small leaks, bubbles will appear (check with a washing liquid).
Damaged components must be replaced.
Brake control – compensation of the braking deceleration that has to be carried out when:
•
the braking force decreases during wear and tear of the brake pad lining during
operation and as a result of the resulting play,
•
wheel brakes brake unevenly and non-simultaneously.
To this end, change the position of the spreader arm to which the piston of the pneumatic
cylinder is acting by changing the initial angle of the spreader shaft at the multi-row end
of the shaft and adjust the length of the bar on the screw. Adjustments must be made for
each wheel separately.
6
Replacement procedures
Replacement of bearings
Replace the damaged bearings following the steps below:
•
place the machine on a horizontal surface,
•
unscrew the four bolts securing ball bearings on each side,
•
move the tubular roller away,
•
loosen both headless bolts in each bearing to be able to pull the bearings out with
the use of a puller,
•
place new bearings on the roller loosely,
•
draw the roller between the bearing plates and screw the bearings to the plates,
Drive the headless bolts with the use of a thread locking glue,
•
do not replace the ball bearings on the disc holders,
•
in case of damage, replace the entire disc holder.
Replacement of workpieces
Excessively worn workpieces hinder soil penetration by the tools and increase the
working resistance. Replace the discs when the diameter has been reduced to 510 mm.
Replace the workpieces on the implement when it is lowered to the ground with the
tractor engine stopped. Put sturdy and robust supports (e.g. approx. 20 cm thick wooden
blocks under the adjacent workpieces or the roller) to prevent contact between the