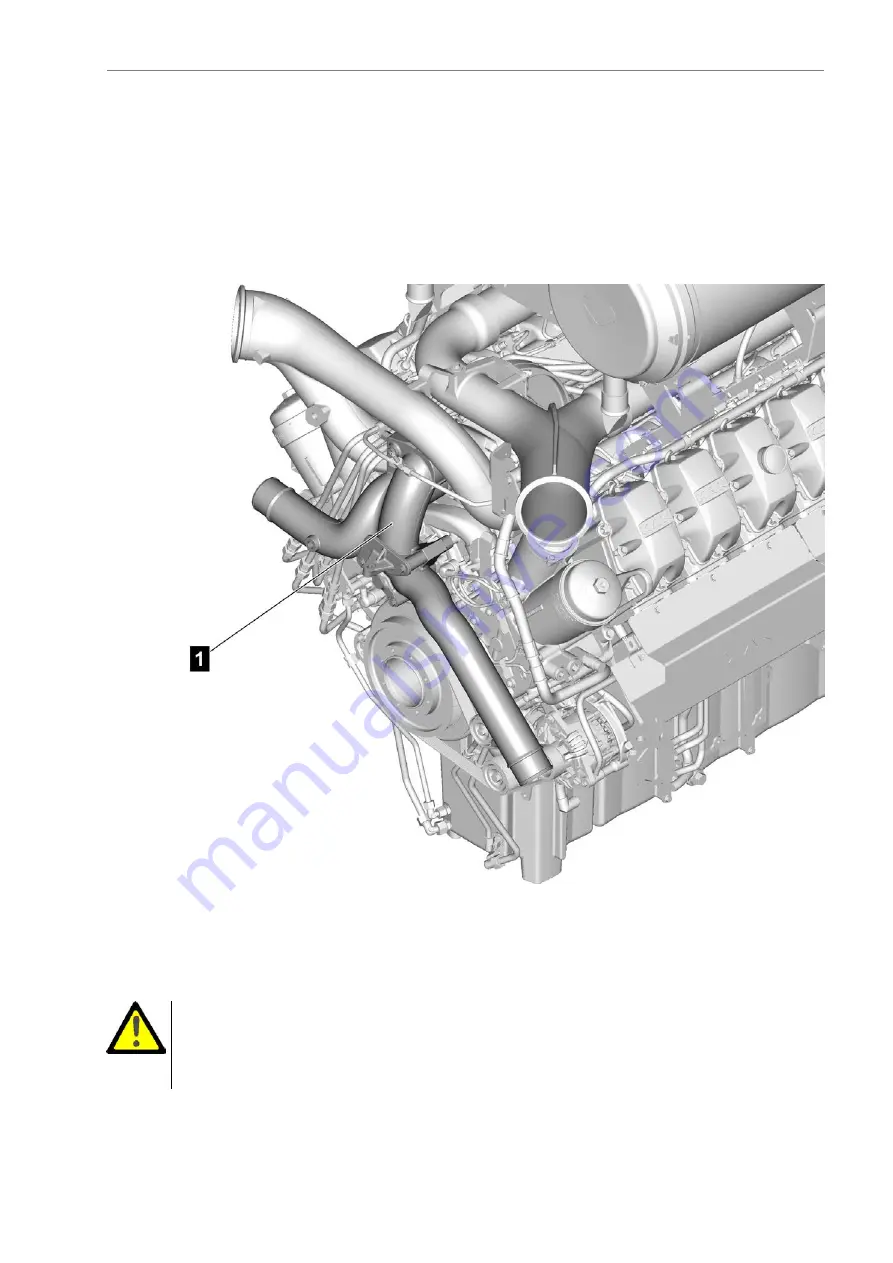
COOLING SYSTEM
COOLANT PUMP COOLANT MANIFOLD
Removing, installing the coolant pump coolant manifold
Additional jobs
–
Removing, installing the cooling system, see 55
–
Removing, installing the ramfan, see 61
–
Removing, installing the fan V-belt, see 85
–
Removing, installing the fan tensioning pulley, see 89
–
Removing, installing the fan carrier with fan bearing, see 91
(1) Coolant pump coolant manifold
Service products
Radiator antifreeze ............................................................................................................ 09.21001-0002
Important information
WARNING
Component damage due to incorrectly tightened screw/bolt connections
• If impact wrenches are used, these may only be used for pretightening to max. 50% of the
specied tightening torque
• Final tightening must always be performed manually using a torque wrench
AE6
3st edition
73
Содержание D2862 LE221
Страница 2: ......
Страница 3: ...Repair Manual AE6 3st edition MAN Industrial Diesel Engines D2862 LE221 D2862 LE223 51 99598 8262 1...
Страница 8: ......
Страница 24: ......
Страница 26: ......
Страница 34: ......
Страница 55: ...COOLING SYSTEM COOLING SYSTEM 1 Coolant manifold 2 Coolant pump 3 Moulded hose 4 Ramfan AE6 3st edition 53...
Страница 56: ......
Страница 62: ......
Страница 74: ......
Страница 78: ......
Страница 82: ......
Страница 86: ......
Страница 108: ......
Страница 166: ......
Страница 174: ......
Страница 182: ......
Страница 188: ......
Страница 212: ......
Страница 213: ...CYLINDER HEAD CYLINDER HEAD 1 Cylinder head cover 2 Cylinder head AE6 3st edition 211...
Страница 214: ......
Страница 246: ......
Страница 252: ......
Страница 256: ......
Страница 264: ......
Страница 269: ...ENGINE LUBRICATION ENGINE LUBRICATION 1 Oil module right 2 Oil module left 3 Oil sump AE6 3st edition 267...
Страница 270: ......
Страница 280: ......
Страница 296: ......
Страница 298: ......
Страница 308: ......
Страница 309: ...CRANK MECHANISM CRANK MECHANISM 1 Flywheel 2 Pistons 3 Vibration damper AE6 3st edition 307...
Страница 310: ......
Страница 316: ......
Страница 334: ......
Страница 355: ...CRANKCASE CRANKCASE 1 Right vent line 2 Left vent line 3 Flywheel housing 4 Engine mount 5 Cover AE6 3st edition 353...
Страница 356: ......
Страница 360: ......
Страница 377: ...TECHNICAL DATA 375 AE6 Stage 2 2st edition Technical Data...
Страница 378: ...TECHNICAL DATA 376 AE6 Stage 2 2st edition...
Страница 402: ...TECHNICAL DATA 400 AE6 Stage 2 2st edition...
Страница 403: ...Special tools 401 AE6 Stage 2 2st edition Special tools...
Страница 404: ...Special tools 402 AE6 Stage 2 2st edition...
Страница 418: ...Special tools 416 AE6 Stage 2 2st edition...
Страница 419: ......