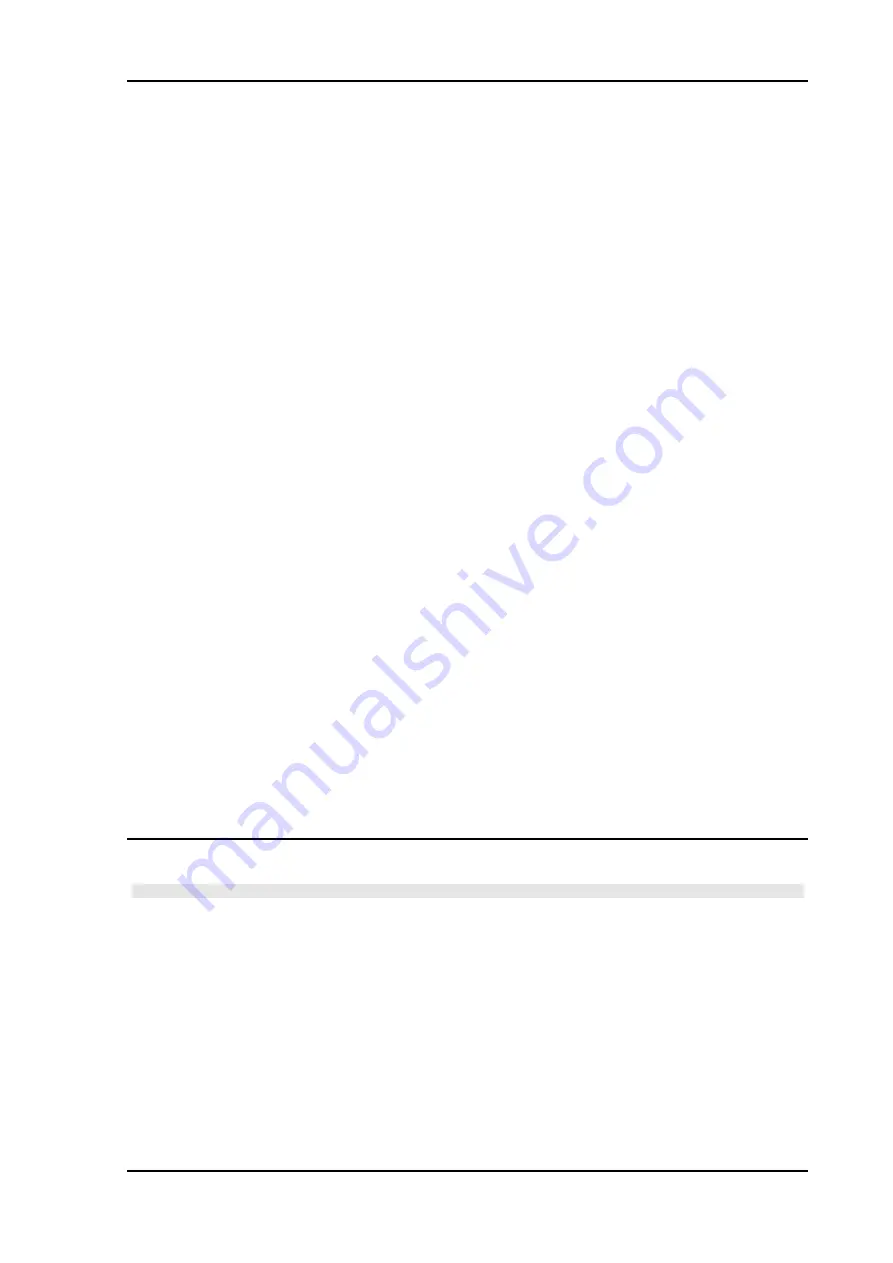
Dune 125 - Dune X 125 - Euro 4
Electrical system
ELE SYS - 93
Short-circuit to positive:
Disconnect the injector connector, turn
the key to ON and activate the compo-
nent through the diagnostic tool.
Verify the absence of voltage at the in-
jector connector PIN 1; if present re-
store the wiring harness, otherwise
proceed with the following checks.
Short circuit to negative:
Disconnect the injector connector, turn
the key to ON and activate the compo-
nent through the diagnostic tool.
Verify the presence of voltage at the
ends of the injector connector; if there
is no voltage, restore the wiring har-
ness, otherwise proceed with the fol-
lowing checks.
Open circuit:
Carry out the check procedure of the
injector and control unit connectors.
Check continuity of cable between
ECU connector and injector connector
(ECU PIN 34 - injector PIN 1). In the
absence of continuity restore the wiring
harness.
Fuel pump
CAUTION
BEFORE CARRYING OUT ANY TROUBLESHOOTING, CAREFULLY READ THE GENERAL TROU-
BLESHOOTING CONCEPTS FOR ELECTRICAL DEVICES AT THE BEGINNING OF THE CHECK
AND CONTROL SECTION IN THE ELECTRICAL SYSTEM CHAPTER.
Содержание Dune 125
Страница 1: ...SERVICE STATION MANUAL ZP682837 Dune 125 Dune X 125 Euro 4 ...
Страница 4: ...Dune 125 Dune X 125 ...
Страница 6: ...INDEX OF TOPICS CHARACTERISTICS CHAR ...
Страница 42: ...SPECIAL TOOLS INDEX OF TOPICS S TOOLS ...
Страница 47: ...INDEX OF TOPICS MAINTENANCE MAIN ...
Страница 59: ...Dune 125 Dune X 125 Euro 4 Electrical system ELE SYS 59 ELECTRICAL SYSTEM INDEX OF TOPICS ELE SYS ...
Страница 60: ...Dune 125 Dune X 125 Euro 4 Electrical system ELE SYS 60 Components arrangement ...
Страница 70: ...Dune 125 Dune X 125 Euro 4 Electrical system ELE SYS 70 General wiring diagram ...
Страница 109: ...ENGINE FROM VEHICLE INDEX OF TOPICS ENG VE ...
Страница 116: ...ENGINE INDEX OF TOPICS ENG ...
Страница 174: ...POWER SUPPLY INDEX OF TOPICS P SUPP ...
Страница 178: ...SUSPENSIONS INDEX OF TOPICS SUSP ...
Страница 190: ...Dune 125 Dune X 125 Euro 4 Suspensions SUSP 190 Remove the screw and washer 7 Remove the shock absorber 8 7 8 ...
Страница 191: ...CHASSIS INDEX OF TOPICS CHAS ...
Страница 222: ...BRAKING SYSTEM INDEX OF TOPICS BRAK SYS ...
Страница 237: ...COOLING SYSTEM INDEX OF TOPICS COOL SYS ...
Страница 245: ...INDEX OF TOPICS BODYWORK BODYW ...
Страница 254: ...Dune 125 Dune X 125 Euro 4 Bodywork BODYW 254 To unload the filter box 7 Remove the filter box 7 ...
Страница 261: ...Dune 125 Dune X 125 Euro 4 Bodywork BODYW 261 Unscrew and remove the screws 7 Remove the radiator cover 8 ...
Страница 264: ...Dune 125 Dune X 125 Euro 4 Bodywork BODYW 264 Remove the tail guard 5 ...
Страница 265: ...Dune 125 Dune X 125 Euro 4 Bodywork BODYW 265 PRE DELIVERY INDEX OF TOPICS PRE DE ...
Страница 269: ...Dune 125 Dune X 125 Euro 4 Pre delivery PRE DE 269 OBD LIST The OBD list are the following ...
Страница 270: ...Dune 125 Dune X 125 Euro 4 Pre delivery PRE DE 270 ...
Страница 271: ...Dune 125 Dune X 125 Euro 4 Pre delivery PRE DE 271 ...
Страница 272: ......