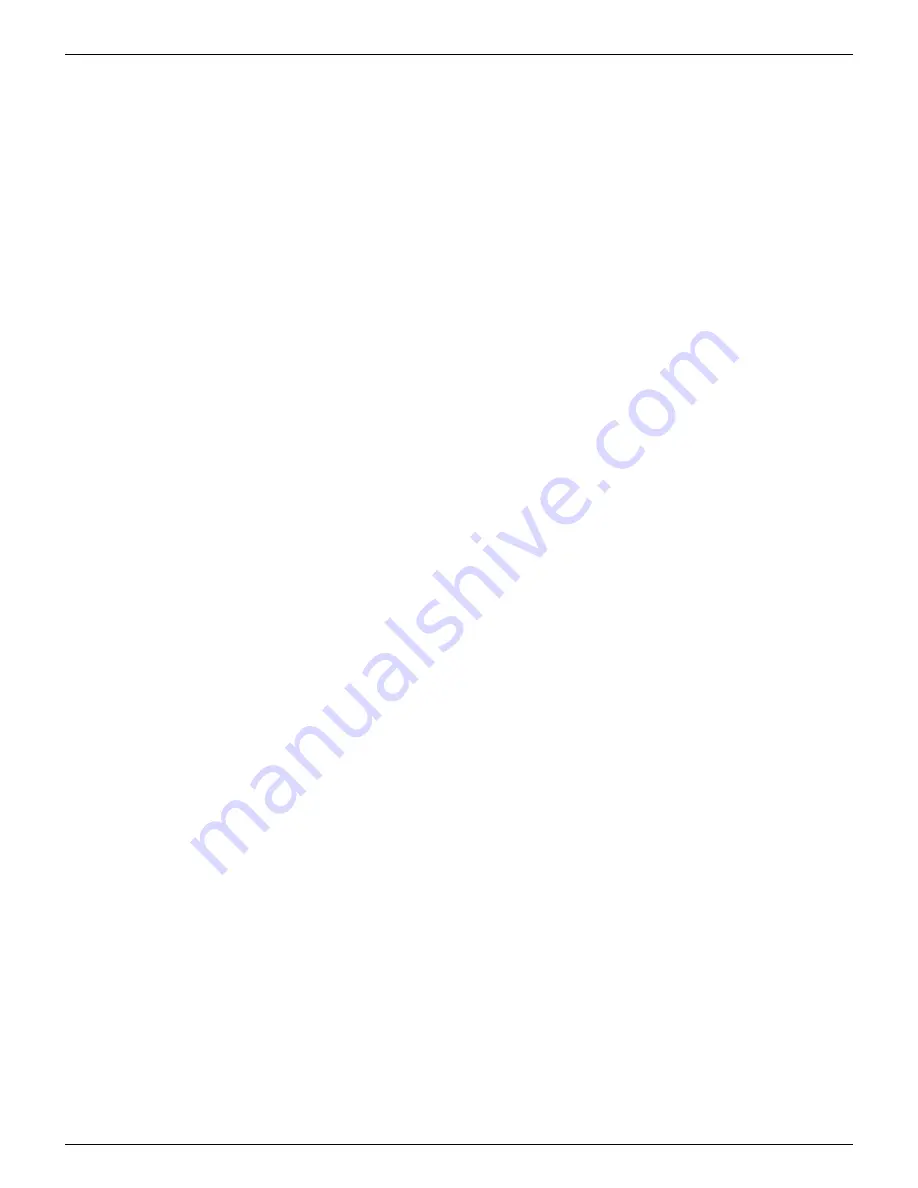
M A G U I R E P R O D U C T S , I N C .
99
W E I G H S C A L E B L E N D E R
Material Dispense Device:
Approx. Grams
per Second:
½” Auger Feeders, Micro Pulse Valves
0.5 - 02
1” Auger Feeders
06 - 10
Vertical Valves
20 - 40
WSB 100 - Slide Gates
250 - 450
WSB 220, 420 -
3” Round Slide Gates
500 - 900
WSB 240, 260, 440, 460, 940, 960, 1840, 1860 - 2
” x 3” Slide Gates
500 - 900
WSB 240, 260, 440, 460, 940, 960, 1840, 1860 -
3” x 6” Slide Gates
3000 - 5000
Regrinds are always lower then naturals. Bulk density will also cause wide variations in flow rates.
ERROR CORRECTIONS: RATE NUMBERS:
(DATA line 2)
The RATE numbers are used by the software, each cycle, to calculate material dispense times. They are adjusted every cycle until
flow rates stabilize. When a significant error is detected, the software adjusts the RATE numbers.
The GRAM number is adjusted first. The TIME number (interrupts) is changed only if the GRAM number goes below 16,000 or
above 32,000 (approximately). In this event both GRAM and TIME numbers are doubled or halved to bring the GRAM number
back to between 16,000 and 32,000.
This serves to keep all numbers as large as possible allowing for the most accurate math, but not so large as to overflow the
registers.
Only the GRAM number changes from cycle to cycle, except under the conditions noted above.
Check the GRAM number for a series of consecutive cycles. If it remains unchanged, then the dispenses are accurate enough to
not trigger error corrections. Another possibility is that the parameters (MI and NC) that determine when error corrections occur are
somehow out of range preventing corrections that should be occurring.
The PRC parameter limits adjustments to 10 percent. Do not expect any single GRAM number change larger then 10 percent.
A gradual decrease in the GRAM number indicates a slowing rate, a hopper that is becoming empty for example. A jump in rate
(increased GRAM number) occurs when the hopper is refilled.
If Errors are occurring, but the GRAM number is NOT adjusting, check the NC parameter and the MI parameter. These control
weather or not error corrections occur. Both are set and adjusted automatically by the software. MI is set after each start up, after
10 cycles have run without retries. MI will be set to indicate 50 percent of normal dispense rate expressed as grams per second.
NC adjusts slowly over extended periods of running. NC indicates, in grams, the upper limit of the error in 60 percent of the
dispenses. A high number usually indicates poor flowing material. Vibration or drifting load cells are other possibilities.
DISPENSE TIMING
: (DATA line 3)
The second number is the number of interrupts calculated to dispense the material. If these times are consistent but the weight of
the first dispense varies, then the material does not flow well, or consistently. Another possibility is excessive vibration or
interference with the weigh bin.
Excess vibration, particularly on small dispenses, may cause incorrect weight readings even though the weight dispensed was, in
fact, correct.
If the timing number is very small, 10, 20, 30 interrupts, perhaps this is asking too much from a slide valve. Very short times mean
you want small amounts, but are using a high rate dispense valve to do the job. An auger, a vertical valve, a horizontal valve with a
flow restrictor, or a smaller valve would help to improve accuracy and control.
If the timing number is below 5, you are operating in a range were it is difficult for the blender to perform well.
The LAG time parameter adds time to every dispense. This is to compensate for the time at the beginning of a dispense when the
solenoid valve shifts and air pressure builds, before the valve starts to move. LAG times are always set slightly longer then the
necessary minimum. If a calculated dispense time is very short, the Lag time that is added, while small, may interfere with
accuracy, and cause an over dispense.
PERCENTAGE ERRORS
: (DATA line 1)
Содержание WEIGH SCALE BLENDER WSB-100 Series
Страница 6: ...M A G U I R E P R O D U C T S I N C 6 W E I G H S C A L E B L E N D E R EC Declaration of Conformity...
Страница 10: ...M A G U I R E P R O D U C T S I N C 10 W E I G H S C A L E B L E N D E R Blender Parts Identification...
Страница 17: ...M A G U I R E P R O D U C T S I N C 17 W E I G H S C A L E B L E N D E R...
Страница 123: ...M A G U I R E P R O D U C T S I N C 123 W E I G H S C A L E B L E N D E R Technical Drawings...
Страница 124: ...M A G U I R E P R O D U C T S I N C 124 W E I G H S C A L E B L E N D E R...
Страница 125: ...M A G U I R E P R O D U C T S I N C 125 W E I G H S C A L E B L E N D E R...
Страница 126: ...M A G U I R E P R O D U C T S I N C 126 W E I G H S C A L E B L E N D E R...
Страница 127: ...M A G U I R E P R O D U C T S I N C 127 W E I G H S C A L E B L E N D E R...
Страница 128: ...M A G U I R E P R O D U C T S I N C 128 W E I G H S C A L E B L E N D E R...
Страница 129: ...M A G U I R E P R O D U C T S I N C 129 W E I G H S C A L E B L E N D E R...
Страница 130: ...M A G U I R E P R O D U C T S I N C 130 W E I G H S C A L E B L E N D E R...
Страница 131: ...M A G U I R E P R O D U C T S I N C 131 W E I G H S C A L E B L E N D E R...
Страница 132: ...M A G U I R E P R O D U C T S I N C 132 W E I G H S C A L E B L E N D E R...
Страница 133: ...M A G U I R E P R O D U C T S I N C 133 W E I G H S C A L E B L E N D E R...
Страница 134: ...M A G U I R E P R O D U C T S I N C 134 W E I G H S C A L E B L E N D E R...
Страница 135: ...M A G U I R E P R O D U C T S I N C 135 W E I G H S C A L E B L E N D E R FCA INSTALLATION DIAGRAM...
Страница 143: ...M A G U I R E P R O D U C T S I N C 143 W E I G H S C A L E B L E N D E R...
Страница 144: ...M A G U I R E P R O D U C T S I N C 144 W E I G H S C A L E B L E N D E R FCA INSTALLATION DIAGRAM...