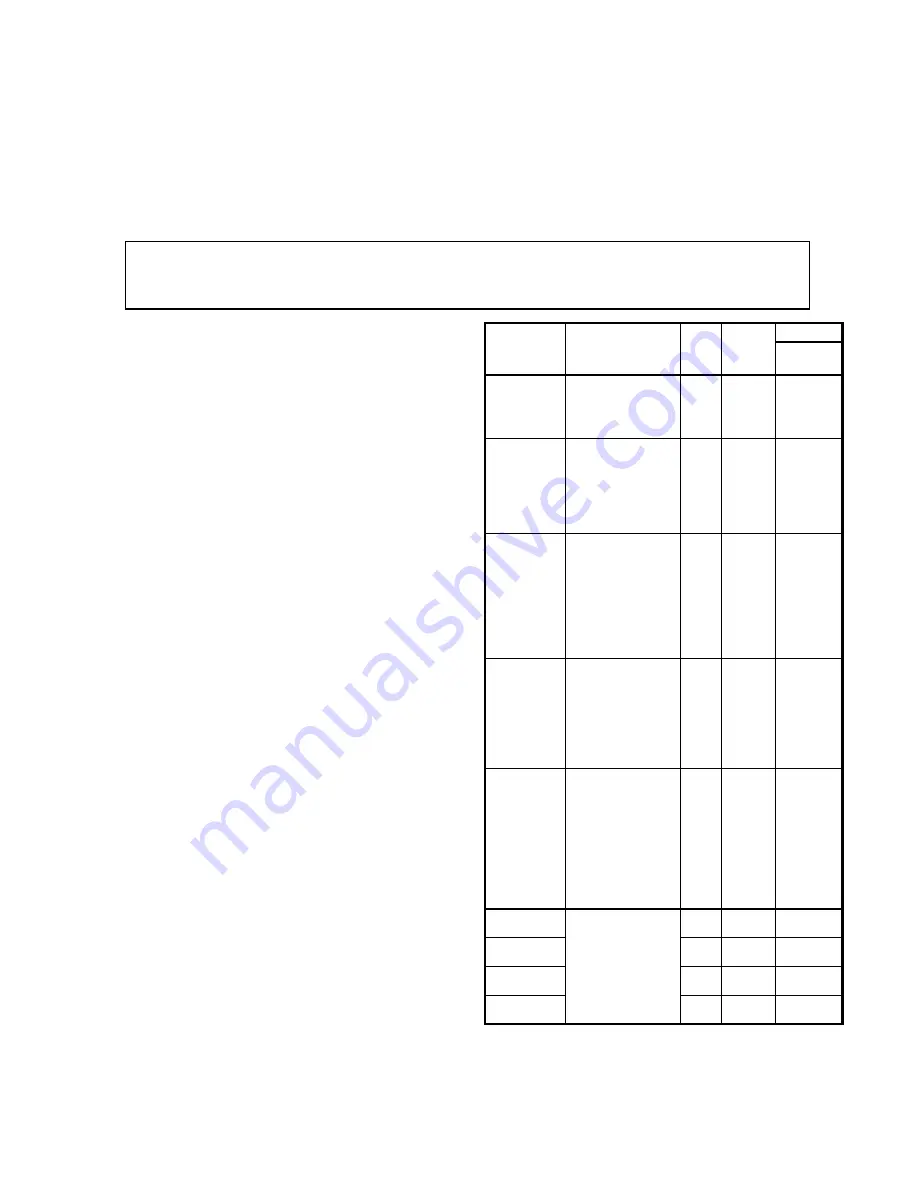
Drive A1 Submenu
58
ANTI-ROLLBACK
Anti-Rollback is an independent function meant to calculate the amount of torque necessary to hold
the car when load weighing is not available. See below for help in adjusting and setting up ARB for a
HPV900 S2 drive.
Please note:
ARB should be a final adjustment. All adjustments in tuning the drive
for smooth car ride (high speed, slowing, and stop) should occur before attempting to tune ARB
To set-up ARB2:
1. Set car in middle of the hoistway so
rollback will not cause the elevator to go
pass the final limits while adjusting ARB2
2. Set the controller to run on Inspection
Speed at 0 speed (allows you to see the
actual rollback). The 0 speed can be done
either in the controller by setting inspection
speed from where it is to 0 speed or on the
drive by changing the Speed Command
Source (C1) from what it is currently set for
to some other type (either Multistep, Serial,
or Analog). NOTE: make sure to write
down what was the Speed Command
Source (C1) set to before changing it
because the motor will not rotate if this is
set incorrectly.
3. The KI1, KP1, KI2, and KP2 gains, ARB
Feed Forward, and the ARB Deadband
should NOT have to be change from
default but if needed to, KI and KP should
be adjusted in increments of 0.100 while
ARB Deadband and ARB feed forward,
should ONLY be change by increments of
1. Too high of a number can cause
oscillation/jerking and too low of a number
will cause rollback.
4. The time set in ARB Timeout should be set
to a time slightly longer than the rollback
observed on the sheave.
5. ARB Advance time should be
increased/decrease by 0.05s until the
rollback is removed.
6. ARB Decay Time should be set to a time
that will allow the drive to stabilize without
oscillating. This value should rarely need
to be below 0.2s.
7. Then set the controller/drive back up to run
on automatic and observe for rollback
Name
Description
Units Range
Recommended
Settings
ENGLISH
(U3)
METRIC (U3)
ARB
Advance
Time period from
when motion is
detected and
brake is opened
sec
0
– 2.00
0.30
ARB Decay
Drop off time
from ARB
Advance to ARB
turned off.
Typically 0.2 to
0.4 seconds.
sec
0
– 2.00
0.40
ARB
Timeout
Time period from
when the drive is
enabled and ARB
stops looking for
motion. Set to
ARB A
ARB Decay +
0.2.
sec
0.80
–
2.00
1.00
ARB
Deadband
The amount of
encoder pulses
the drive ignores
before
acknowledging
rollback is
occurring
-
0-20
4
ARB Feed
Forward
Feedfoward gain,
should be set as
small as possible
to improve ARB
stability. Adjust
after ARB Decay
and ARB
Advance have
been set.
-
0-100
0
ARB KP1
Gains that should
normally not
need changing.
-
0.0
–
32.000
1.0
ARB KI1
-
0.0
–
32.000
0.50
ARB KP2
-
0.0
–
32.000
6.00
ARB KI2
-
0.0
–
32.000
6.00
CAUTION
ARB cannot be used in conjunction with PreTorque. PRETORQUE SRC (C1) = NONE when ARB
SELECT (C1) is set to ARB2 or ARB3.
Содержание HPV 900 Series 2
Страница 4: ......
Страница 195: ...APPENDIX Dimensions Mounting Holes Weights 173 Figure 46 Frame 2 Dimensions Mounting Holes and Weight...
Страница 196: ...APPENDIX Dimensions Mounting Holes Weights 174 Figure 47 Frame 3 Dimensions Mounting Holes and Weight...
Страница 197: ...APPENDIX Dimensions Mounting Holes Weights 175 Figure 48 Frame 3 5 Dimensions Mounting Holes and Weight...
Страница 198: ...APPENDIX Dimensions Mounting Holes Weights 176 Figure 49 Frame 4 Dimensions Mounting Holes and Weight...
Страница 199: ...APPENDIX Dimensions Mounting Holes Weights 177 Figure 50 Frame 5 Dimensions Mounting Holes and Weight...
Страница 227: ...205 Z Z MARKER LOST 150 Zero Speed Level parameter 47 Zero Speed logic output 105 Zero Speed Time parameter 47...
Страница 228: ......
Страница 229: ......