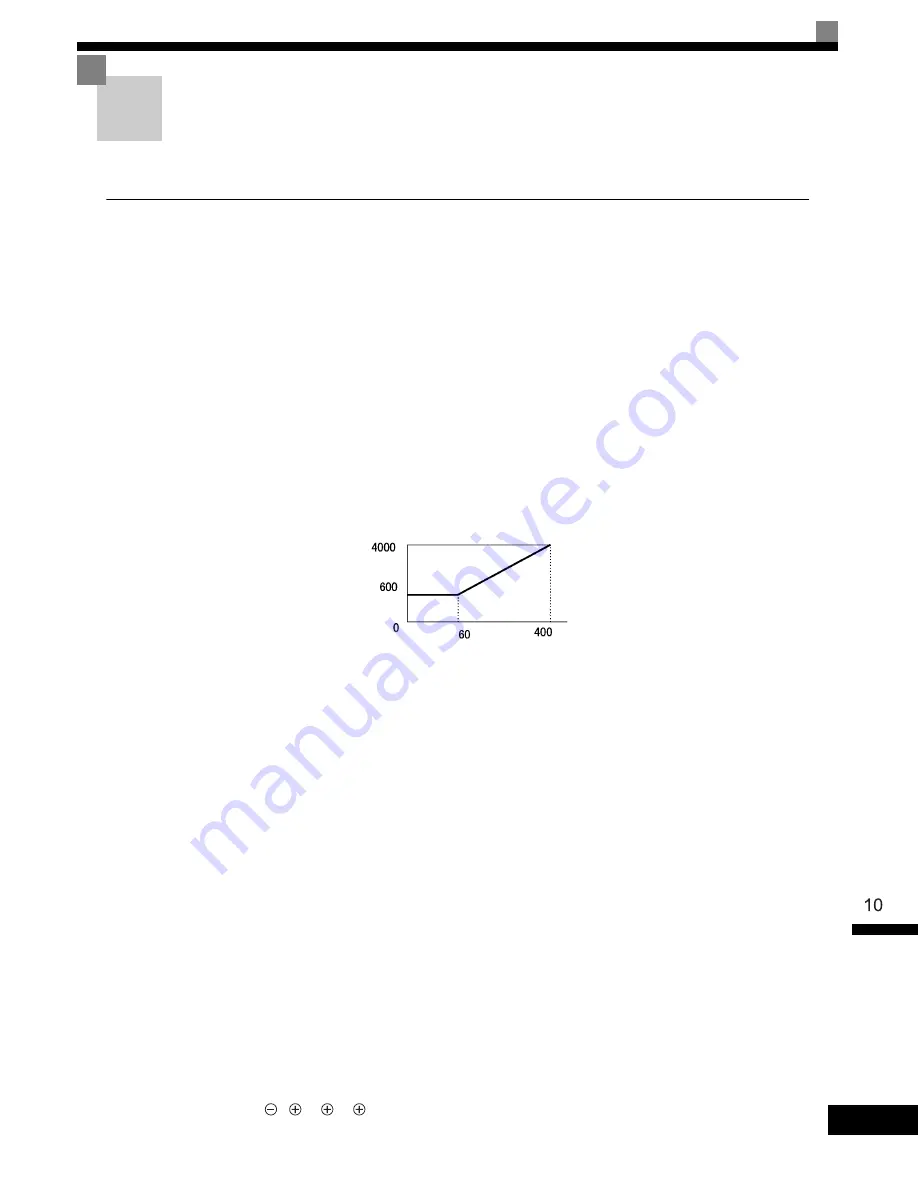
Drive Application Precautions
10-
7
Drive Application Precautions
This section provides precautions for selecting, installing, setting, and handling Drives.
Selection
Observe the following precautions in selecting Drive.
Installing Reactors
A large peak current will flow in the power input circuit when the Drive is connected to a large-capacity power
transformer (600 kVA or higher) or when switching a phase capacitor. Excessive peak current can destroy the
convertor section. To prevent this, install a DC or AC reactor (optional) to improve the power supply power
factor.
DC reactors are built into 200-240 V class Drives of 18.5 to 110 kW and 380-480 V class Drives of 18.5 to 300
kW.
If a thyristor convertor, such as a DC drive, is connected in the same power supply system, connect a DC or
AC reactor regardless of the power supply conditions shown in the following diagram.
Fig 10.5
Drive Capacity
When connecting special motors or multiple motors in parallel to Drive, select the Drive capacity so that the
rated output current of the Drive is 1.1 times the sum of all the motor rated currents.
Initial Torque
The startup and acceleration characteristics of the motor are restricted by the overload current ratings of the
Drive that is driving the motor. The torque characteristics are generally less than those required when starting
using a normal commercial power supply. If a large initial torque is required, select Drive with a somewhat
larger capacity or increase the capacity of both the motor and the drive.
Emergency Stop
Although the Drive's protective functions will stop operation when a fault occurs, the motor will not stop
immediately. Always provide mechanical stop and protection mechanisms on equipment requiring an emer-
gency stop.
Options
Terminals B1, B2,
,
1,
2,
3 are for connecting only the options specifically provided by
Magnetek
. Never connect any other devices to these terminals.
Power supply
capacity (kVA)
DC or AC reactor
Required
DC or AC reactor
Not required
Drive capacity (kVA)