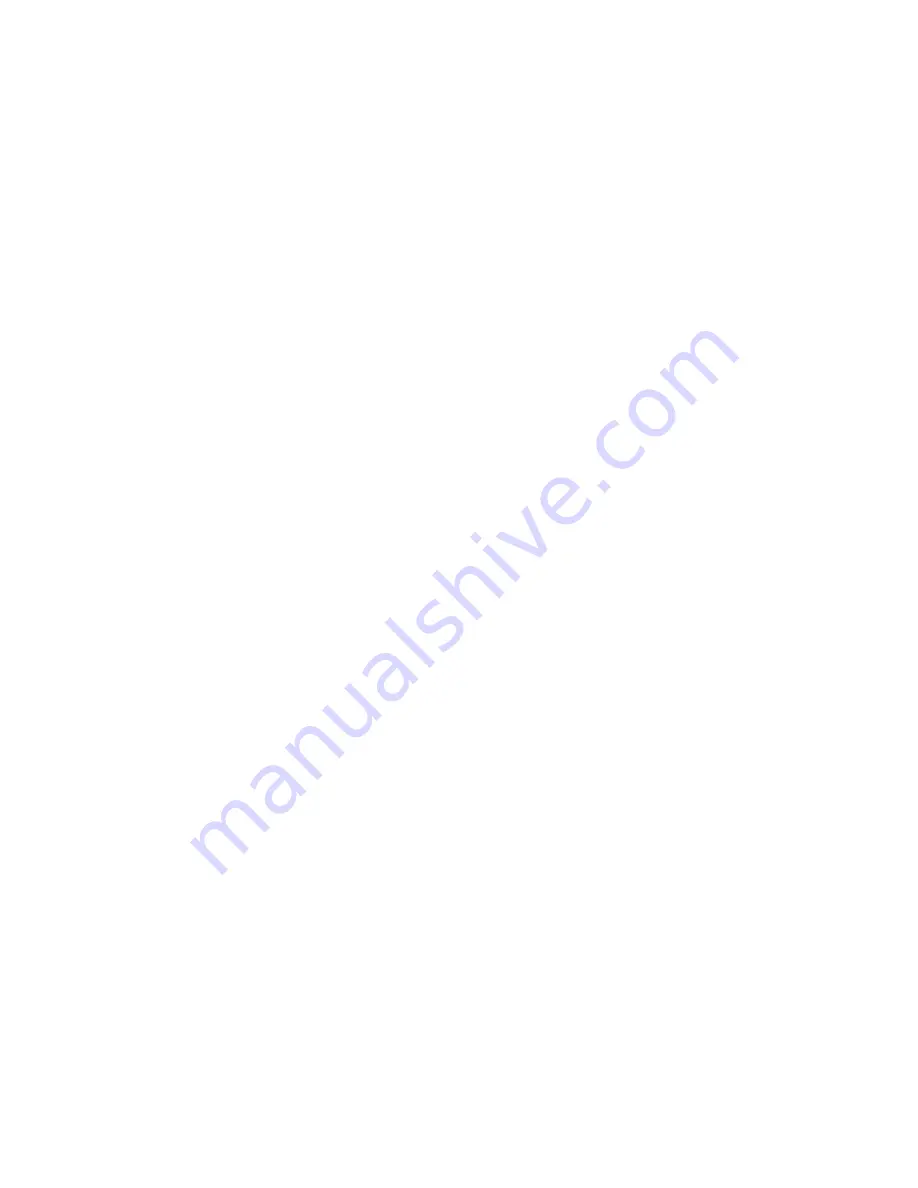
Appendix – Anti-Rollback Setup
127
pulls through the brake to start the car, is a result of poor velocity reference release vs brake
release timing. With ARB the velocity reference should not be released to move away from
zero until after the brake is mechanically released. Otherwise the ARB feature cannot work.
4. Anti-Rollback can be used with external load weighing and pre-torque, as these features are
independent of each other. If motor pre-torque values are not precisely correct at the time of
starting the elevator drive, as may occur during elevator re-leveling, the features of ARB will
intervene to help reduce rollback. If pre-torque is accomplished correctly, Anti-rollback will not
need to do anything. However, it can still cause vibration or oscillation if ARB gains are set too
high.
5. It is not always convenient to use payload weights during adjustment. Most elevators are
counterweighted such that an empty car represents an unbalanced load of 43-57%, with the
counterweight being heavier. If Anti-rollback works effectively with an empty car at all landing
stops, it should also perform adequately with full payload weight in the car. Step 7 in the
adjustment procedure indicates how to verify and adjust ARB operation with a full car payload, but
it is not always necessary.
Anti-rollback may also be used to hold the car at a constant position at the end of an elevator run.
Normally this is not required because the velocity regulator, E-Reg, will stabilize and hold an armature
current value as necessary to hold the car at a standstill at the end of an elevator run. However,
turning ARB back on may be useful to aid car re-level positioning without first setting the brake for a
total drive re-start. Set ARB mode to “2” to re-enable ARB when the car returns to zero speed at the
end of an elevator run. Zero speed in this case is measured by the encoder, not the reference, and
defined by the up/down threshold. ARB will remain enabled until the drive is either shut down by
removal run logic, or the internal velocity reference is increased to again be larger than the ARB
threshold. If u/d threshold is set too high, there may be a jerk felt as the car comes to rest and the
control switches to the ARB zero speed / position hold mode. If u/d threshold is set too low, minor
disturbances and movement may delay and possibly prevent control transfer to the ARB hold mode
because the measured encoder speed over a relatively short measuring time appears to not fall below
the threshold value. Set up/down threshold to the lowest value that yields repeatable results.
Содержание Quattro DC
Страница 145: ...Appendix Dimensions and Weights 143 Figure 23 Dimensions without optional Customer I O Panel no Top Hat...
Страница 146: ...Appendix Dimensions and Weights 144 Figure 24 Dimensions with optional Customer I O Panel no Top Hat...
Страница 147: ...Appendix Dimensions and Weights 145 Figure 25 Dimensions without optional Customer I O Panel includes Top Hat...
Страница 148: ...Appendix Dimensions and Weights 146 Figure 26 Dimensions with optional Customer I O Panel includes Top Hat...
Страница 160: ...Appendix Input Voltage Requirements 158 Figure 39 200A Application Guide Figure 40 250A Application Guide...
Страница 161: ...Appendix Input Voltage Requirements 159 Figure 41 300A Application Guide...
Страница 177: ......