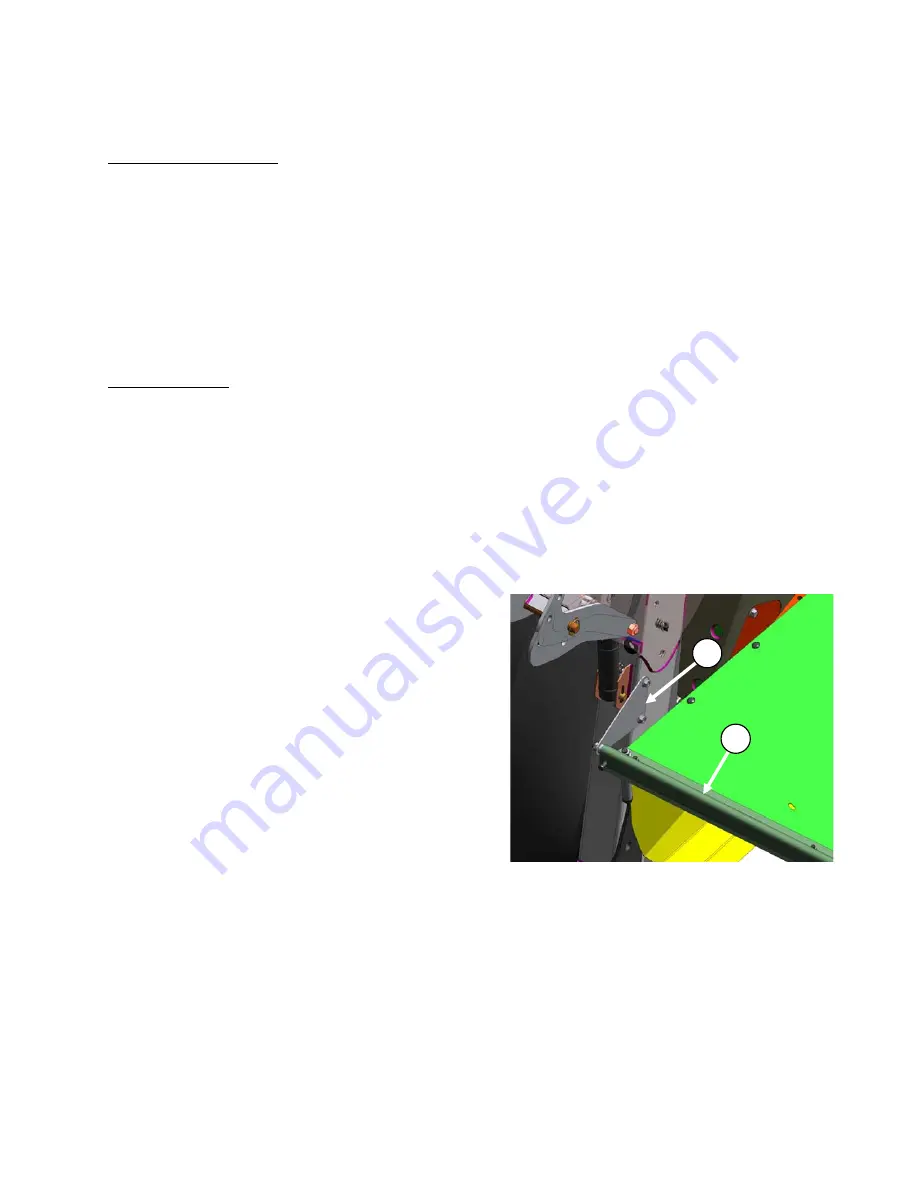
OPERATION
Form 169216
January 2009
19
Operating Recommendations:
15’, 16’, 18’, 20’ Headers: On the first pass, the
side delivery system is raised and crop is
deposited between tractor wheels. On the return
pass, the side delivery system is lowered and
crop is deposited outside of the tractor wheels to
the right, beside the previously laid windrow.
Position of the crop can be adjusted by using the
side deflectors on the forming shields when
depositing the crop in the center and by varying
the draper speed when depositing the crop to
the side. The faster the draper speed is set, the
farther the crop will be delivered to the side.
25’, 30’ Headers: The side delivery system is
lowered at all times. Crop is deposited outside
the tractor wheels and laid beside the previously
deposited windrow on return pass. Position of
the crop can be adjusted by varying the draper
speed when depositing the crop to the side.
One can also raise the side delivery system and
center deliver all the time.
Operating Recommendations with R80
Header:
The conditioner rolls on an R80 header are
further ahead than all other headers; therefore
delivering
light crop
from the conditioner rolls to
the side delivery deck may require special
attention:
There are three areas that can affect the crop
flow to the deck:
1.
Crop flow from the cutterbar to the rolls.
a. Header cut width must be kept as full as
possible on the right hand side. Any
less than 75% may have adverse effects
on feeding.
b. Feed plates must be installed for
appropriate crop. They are required for
forage but not for alfalfa. (See R80
Operator’s Manual.)
c. Higher ground speeds will usually result
in better crop flow from the conditioner
rolls to the deck. Ground speed should
be a minimum of 6 mph (10 km/h) for
light crops.
d. Disc speed must be in recommended
range for specific crop/yield. (See R80
operator’s manual.)
2.
Crop flow from rolls to forming shield.
a. Rear baffle on the R80 header should
be in the upmost position. However it
may need to be lower for center
windrowing.
b. If there are fins on the rear baffle,
remove them to prevent interference
with the crop flow.
c. Header angle: The steeper the header
angle, the higher the arc of the crop
trajectory will be. Header angle should
be set such that the crop is projected at
a maximum arc height without excessive
contact with the top forming shield. It
may be possible to shoot crop above the
forming shield with extreme header
angle and rear baffle positions. In rocky
conditions where DWA is necessary, a
high skid shoe kit or adjustment to
gauge rollers may be required to
achieve correct stubble height and also
maintain crop trajectory.
d. Header height: affects the header
angle. Target should be to have the lift
linkage fully down at all times.
e. The roll gap should be small enough to
properly grab the crop and throw it.
f. The roll speed which is mechanically
tied to the disc speed can affect how
fast the crop gets projected. This again
should be in the recommended range.
3.
Forming shield settings:
a. Make sure forming shield (B) is installed
correctly with bracket (A).
b. Buildup of sticky crop residue on
deflector sliding surfaces should be
periodically removed.
c. See “Conditioner Forming Shield
Position” on previous page.
A
B
Содержание M150 2009
Страница 2: ...MACDON DOUBLE WINDROW ATTACHMENT ...
Страница 26: ...MAINTENANCE SERVICE Form 169216 January 2009 24 Hydraulic Schematic ...
Страница 30: ...Form 169216 January 2009 28 DECK DRAPER ROLLERS Illustration 2 ...
Страница 32: ...Form 169216 January 2009 30 DECK SUPPORTS LINKAGE Illustration 1 ...
Страница 34: ...Form 169216 January 2009 32 DECK SUPPORTS LINKAGE Illustration 2 ...
Страница 36: ...Form 169216 January 2009 34 HYDRAULICS IN CAB ELECTRICAL ...
Страница 38: ...Form 169216 January 2009 36 HYDRAULIC SERVICE COMPONENTS ...