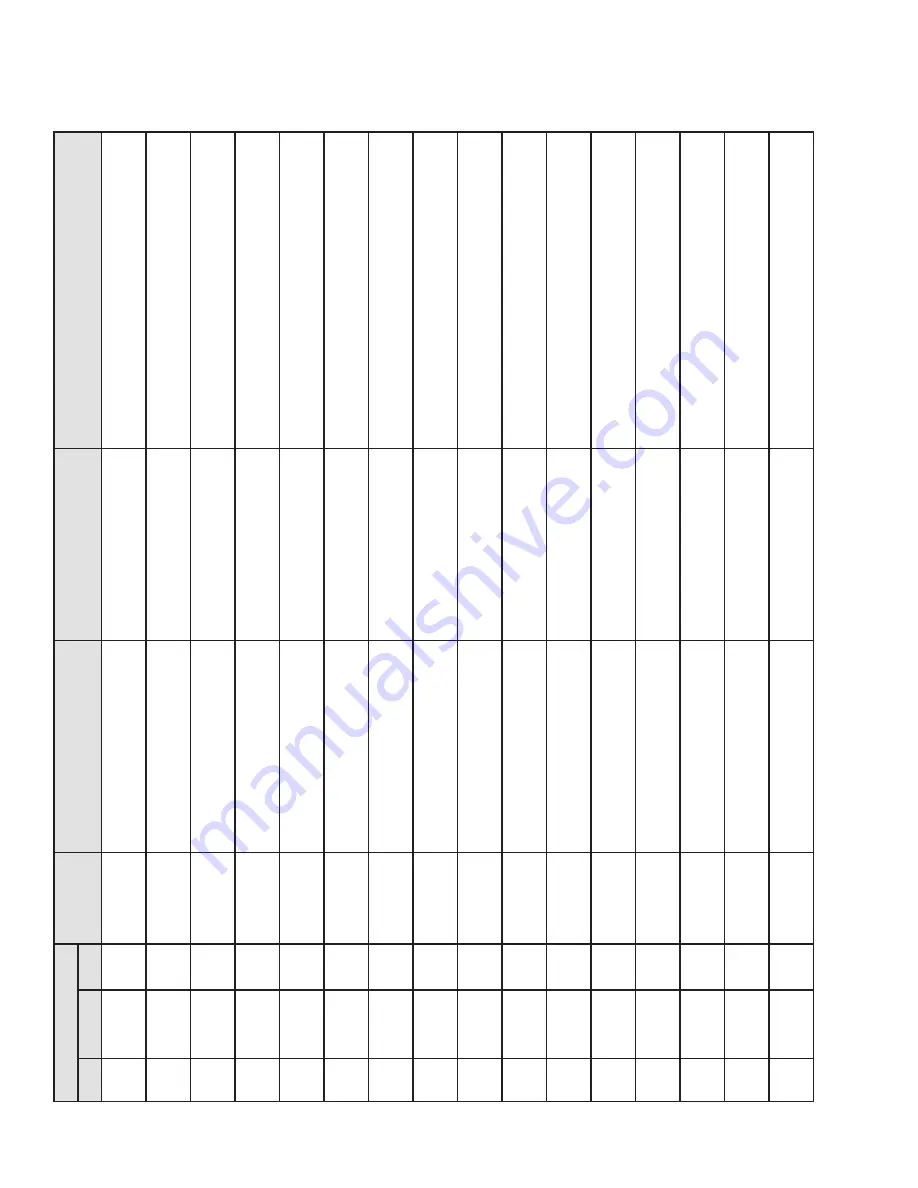
214733
454
Revision A
Fault
Codes
Telltale
Short
Description
Full
Fault
Description
Recommended
Fix/Check
Message
SA
SPN
FMI
176
521483
1
Electrical
Syst
e
m
Roof
Relay
Module
Err
or
-
Module,
Roof
mVEC
Contact
Dealer
.
176
521484
1
Electrical
Syst
e
m
Roof
Relay
Module
Err
or
-
Module,
Roof
mVEC
Contact
Dealer
.
176
521485
1
Electrical
Syst
e
m
Roof
Relay
Module
Err
or
-
Module,
Roof
mVEC
Contact
Dealer
.
176
521486
1
Electrical
Syst
e
m
Roof
Relay
Module
Err
or
-
Module,
Roof
mVEC
Contact
Dealer
.
178
521186
1
Electrical
Syst
e
m
Brake
Lights,
Cab
Fwd
BK1
Relay
coil
open
or
not
present
Check
chassis
module
for
missing
replay
.
Replace
relay
.
178
521186
2
Electrical
Syst
e
m
Brake
Lights,
Cab
Fwd
BK1
Relay
Coil
short
ed
or
failed
relay
driver
Replace
relay
.
178
521186
3
Electrical
Syst
e
m
Brake
Lights,
Cab
Fwd
BK1
Relay
Normally
Open
contact
is
open
Replace
relay
.
178
521186
4
Electrical
Syst
e
m
Brake
Lights,
Cab
Fwd
BK1
Relay
Normally
Closed
contact
is
open
Replace
relay
.
178
521186
5
Electrical
Syst
e
m
Brake
Lights,
Cab
Fwd
BK1
Relay
coil
is
not
receiving
power
Contact
Dealer
.
178
521186
6
Electrical
Syst
e
m
Brake
Lights,
Cab
Fwd
BK1
Relay
Normally
open
contact
is
short
ed
Replace
relay
.
178
521186
7
Electrical
Syst
e
m
Brake
Lights,
Cab
Fwd
BK1
Relay
Normally
closed
contact
is
short
ed
Replace
relay
.
178
521194
1
Electrical
Syst
e
m
High
Beam,
Engine
Fwd
BK2
Relay
coil
open
or
not
present
Check
chassis
module
for
missing
replay
.
Replace
relay
.
178
521194
2
Electrical
Syst
e
m
High
Beam,
Engine
Fwd
BK2
Relay
Coil
short
ed
or
failed
relay
driver
Replace
relay
.
178
521194
3
Electrical
Syst
e
m
High
Beam,
Engine
Fwd
BK2
Relay
Normally
Open
contact
is
open
Replace
relay
.
178
521194
4
Electrical
Syst
e
m
High
Beam,
Engine
Fwd
BK2
Relay
Normally
Closed
contact
is
open
Replace
relay
.
178
521194
5
Electrical
Syst
e
m
High
Beam,
Engine
Fwd
BK2
Relay
coil
is
not
receiving
power
Contact
Dealer
Содержание M1170
Страница 1: ...M1170 Windrower Operator s Manual 214733 Revision A Original Instruction The harvesting specialists ...
Страница 3: ...Declaration of Conformity 1026635 214733 Revision A ...
Страница 4: ...1026636 214733 Revision A ...
Страница 44: ......
Страница 287: ...214733 271 Revision A 5 5 5 Electrical System Module Layout MAINTENANCE AND SERVICING ...
Страница 288: ......
Страница 289: ...MAINTENANCE AND SERVICING Module Locations 1024956 A B C D E F G H J 214733 273 Revision A ...
Страница 401: ...214733 385 Revision A Figure 5 204 Roof Headliner Fuse Decal MD 207819 Group E 1018767 MAINTENANCE AND SERVICING ...
Страница 418: ......
Страница 514: ......
Страница 526: ......