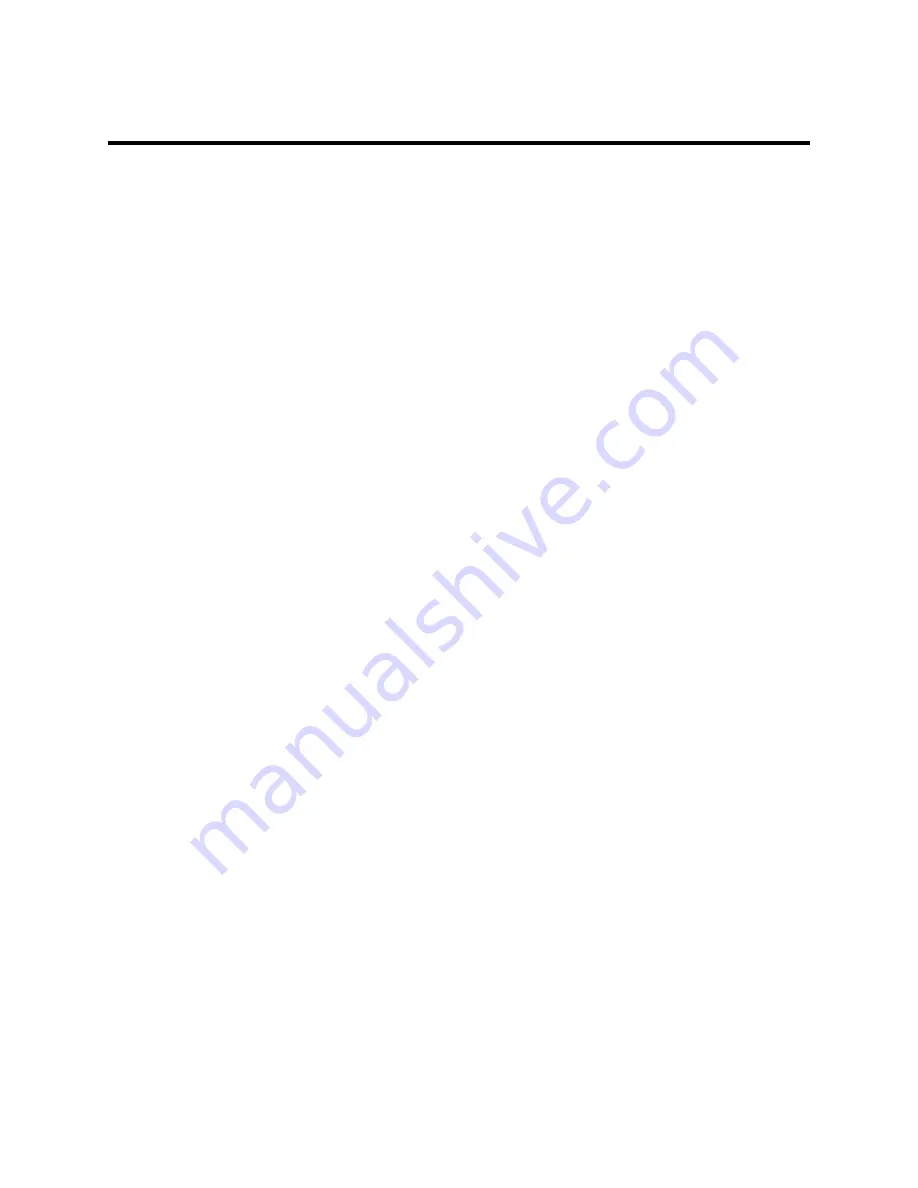
Control/Monitoring
HIGH (REFRIGERANT) PRESSURE - Red
Located on the upper left side of the
controller. Flashing when a high
compressor discharge pressure condition
exists (warning). If pressure continues to
increase and exceeds the setpoint, the light
will become solid (alarm) and the unit will
shut down.
REFRIGERANT - Red
Located on the upper right side of the
controller. Flashing when a low refrigerant
level is sensed in the receiver. The light will
become solid when the unit shuts down on
low suction pressure (after the time delay).
COMPRESSOR OVERLOAD (FAULT) - Red
Located on the lower right side of the
controller. 3 flash sequence.
Activated after a 2 second time delay
by the current sensor in one of the
leads to the compressor motor when
the motor has been shut down due
to excessive temperature.
PUMP OVERLOAD (FAULT) - Red
Located on the lower right side of the
controller. 2 flash sequence. Activated
when the pump amperage exceeds the
overload setting.
PUMP LOW FLOW (FAULT) - Red
Located on the lower right side of the
controller. Single flash. Activated when the
pump flow falls below setpoint to warn the
operator of an impending low flow condition.
PHASE REVERSAL (FAULT) - Red
Located on the lower right side of the
controller. Solid light. Activated when
phases of the unit need to be reversed.
This may happen on initial start up of the
unit. If it occurs, switch phases external to
the unit and power the unit again.
To restart the unit after any fault occurs, the power must be cycled. To cycle the power, place
the ON/OFF/SET switch in the OFF position and open the main circuit breaker for a few
seconds. When power is reapplied and the ON/OFF/SET switch is placed in the ON position,
the unit should restart.
Artisan Technology Group - Quality Instrumentation ... Guaranteed | (888) 88-SOURCE | www.artisantg.com