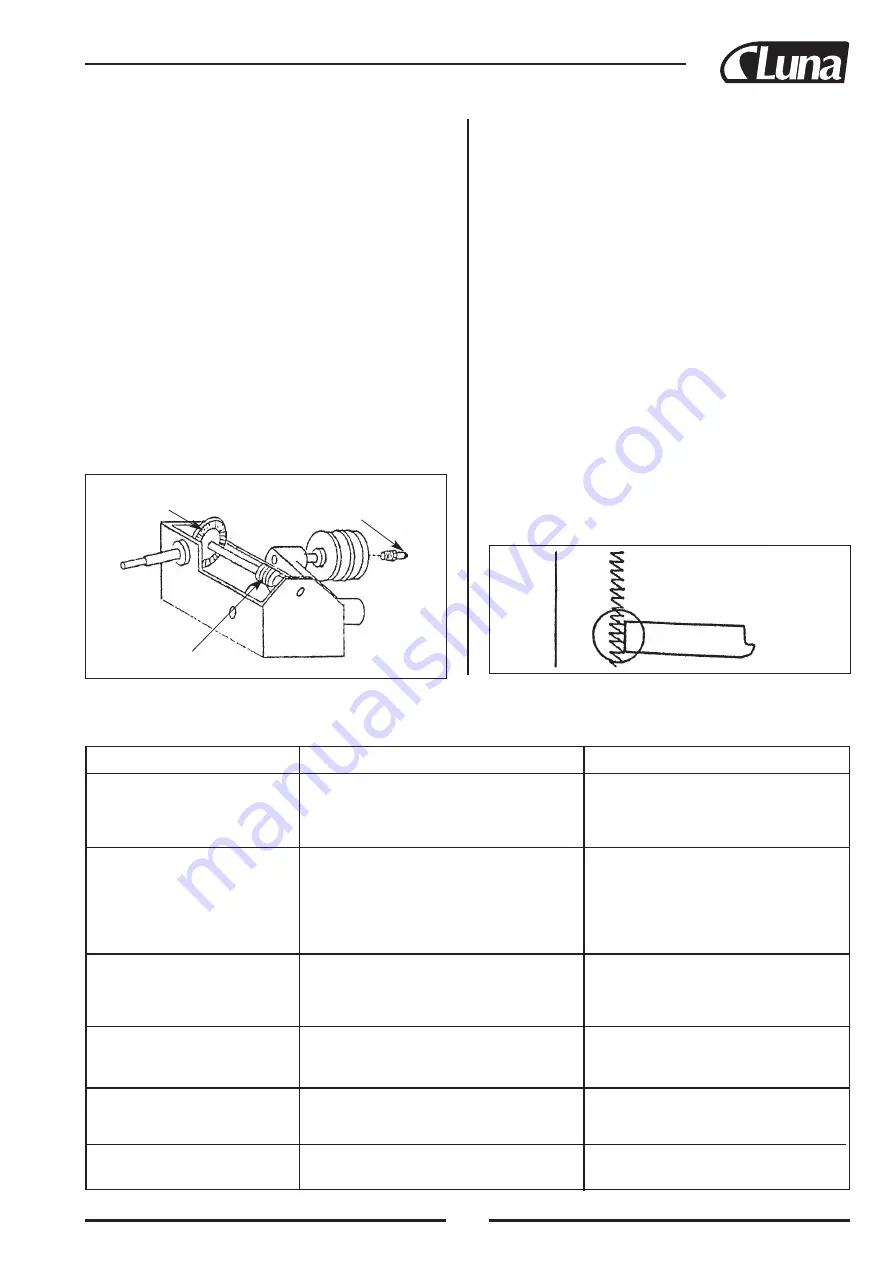
47
4. MAINTENANCE AND REPAIR PROCEDURE
FOR MECHANIC COMPONENTS
(1) Maintenance
1. Free/drive wheel
a. Do not work with objects which may release oil or water during opera-
tion. This will cause the rubber in the blade wheel to swell and be
damaged.
b. Remove the iron scrap on the blade wheel to protect the rubber on the
wheel.
c. Adjust the blade to a reasonable tension. The blade may break when it
is too tight and slippery when it is too loose and the rubber will be
damaged which will affect the quality.
2. Brake
a. Check if the oil level is within the standard range, otherwise andd- #69
gear oil.
b. Change gear oil after first month and then change the oil for every three
months. Use #69 gear oil.
c. Do not block the air vent of the brake. It may cause overheating and
reduce the machine service time.
d. Do not overload the machine. It will reduce the brake service time.
3. Transmission mechanism:
Spread grease once
a month
Spread grease
once a month
Spread grease once a month
Includ 2-4 pitch
Problem
Cause
Solution
Blade broken
Curve cutting patch
Saw tooth broken
Bad cutting surface
Blade tooth worn too fast
Vibration
Guide worn out.
Guide too far from each other.
Rubber ring in blade wheel worn out.
Blade wheel work incorrectly.
Guide worn out.
Guide adjust incorrectly.
Guide rod loose.
Insertion pressure too high.
Tooth pitch too small.
Low blade tension.
Tooth pitch too small.
Working object not fixed.
High insert pressure.
Swarf gutter block.
Blade speed too slow.
Blade pitch too large.
Insert pressure too high.
Use wrong cutting parameter.
Defects in the object surface (rust, sand
or stiff surface).
Low blade tension.
Unavoidable nature frequency.
Change the guide.
Adjust the guide.
Change the rubber ring.
Adjust the blade wheel.
Change the guide.
Readjust the guide.
Adjust the rod.
Reduce the pressure.
Use larger pitch blade.
Increase the tension.
Use larger pitch blade.
Fix the working object.
Reduce the pressure.
Remove the swarf.
Increase the speed.
Use small pitch blade.
Reduce the pressure.
Change to right values.
Reduce the insert pressure or clean the
surface.
Increase the blade tension.
Fine tune the blade speed.
(2). Solution of problems
a. Do not shift unless the motor is running. Otherwise it may break the
transmission rack or bend the adjust screw.
b. Apply the lube grease every month to make sure the transmission wheel
bearing and the shaft is well lubed.
4. Transmission wheel
a. Do not turn the hand wheel unless the motor is running to keep the
shape of the hand wheel.
b. Set the cutting speed to 50-60 m/min after finishing the job to keep the
shape of the wheel.
c. Open the back cover and apply lube oil with inject gun to the shaft of
wheel. Do not use too much oil to cause belt slippery and affect the per-
formance.
5. Welder
a. Adjust the pressure based on the width of the blade when using welder.
b. Clean the welding claw regularly to maintenance its electric conductivi-
ty and make the welder work smoothly.
c. Zero the welding pressure to keep the spring in good condition after
finishing the welding and keep it in good condition.
6. Blade selection:
a. Use high pitch blade for hard material and use low pitch blade for soft
material. These will maintain the quality of the process and extend the
service time.
b. Use low pitch blade for thicker material and high pitch blade for thin
material. Allow 2-4 teeth for the width of the object. This is suitable for
most material. (See the following diagram.)
Содержание 20144-0203
Страница 2: ...Vertikal bands g Vertical bandsaw MBS 40V MBS 60V 20144 0203 20144 0302 20144 5103 20144 5202...
Страница 5: ...3 Danska 4 Suomi 21 English 38 Norsk 55 Svenska 72...
Страница 99: ...97 9 Welder assembly...
Страница 102: ...100 11 Machine body assembly MBS 60 V...
Страница 104: ...102 10 ELECTRICAL SCHEMATIC...