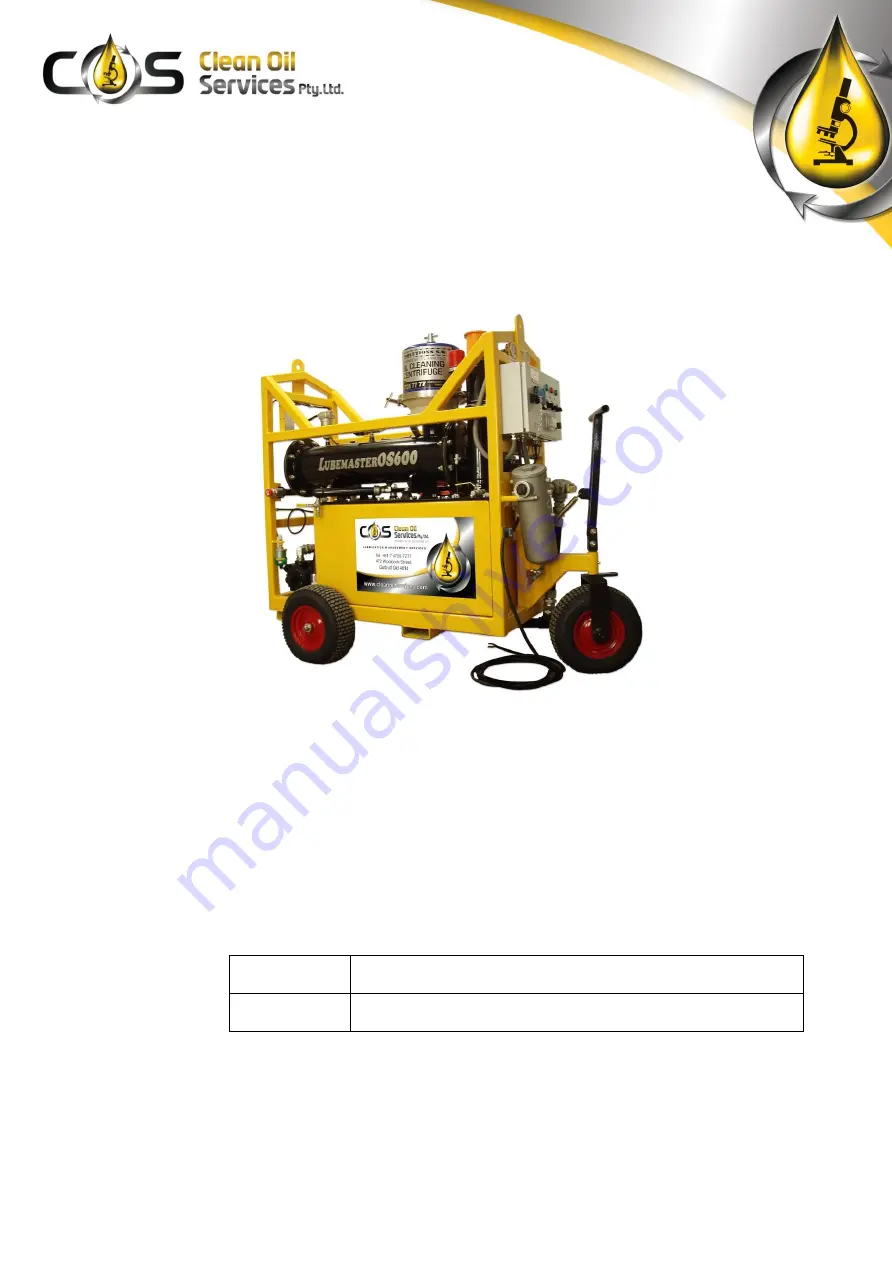
Lubemaster Model OS600 Standard
OPERATING INSTRUCTIONS
AND
PARTS MANUAL
Serial No OS600
Unit No
OS600-0
This equipment is protected by the following patent/applications
Australia 2003277964 New Zealand 540199 Europe 1 563 037
USA 10 / 533403 International 10 / 5334
472 Woolcock Street
PO Box 7942, Garbutt Qld 4814 Australia
P
+61 7 4728 7777
F
+61 7 4728 7799
W
www.cleanoilservices.com
E
ABN 89 058 024 936
L U B E M A S T E R A U S T R A L I A P T Y L T D
Содержание OS600 Standard
Страница 3: ...Lubemaster OS600 Std 3102 Operating Manual V2020 01 Page 4 of 29 1 SAFETY PROCEDURES 1 1 SAFE LIFTING ...
Страница 27: ...Lubemaster OS600 Std 3102 Operating Manual V2020 01 Page 27 of 29 7 DIAGRAMS 7 1 ELECTRICAL CIRCUIT ...
Страница 28: ...Lubemaster OS600 Std 3102 Operating Manual V2020 01 Page 28 of 29 7 2 P ID ...
Страница 29: ...Lubemaster OS600 Std 3102 Operating Manual V2020 01 Page 29 of 29 8 CE CERTIFICATION ...