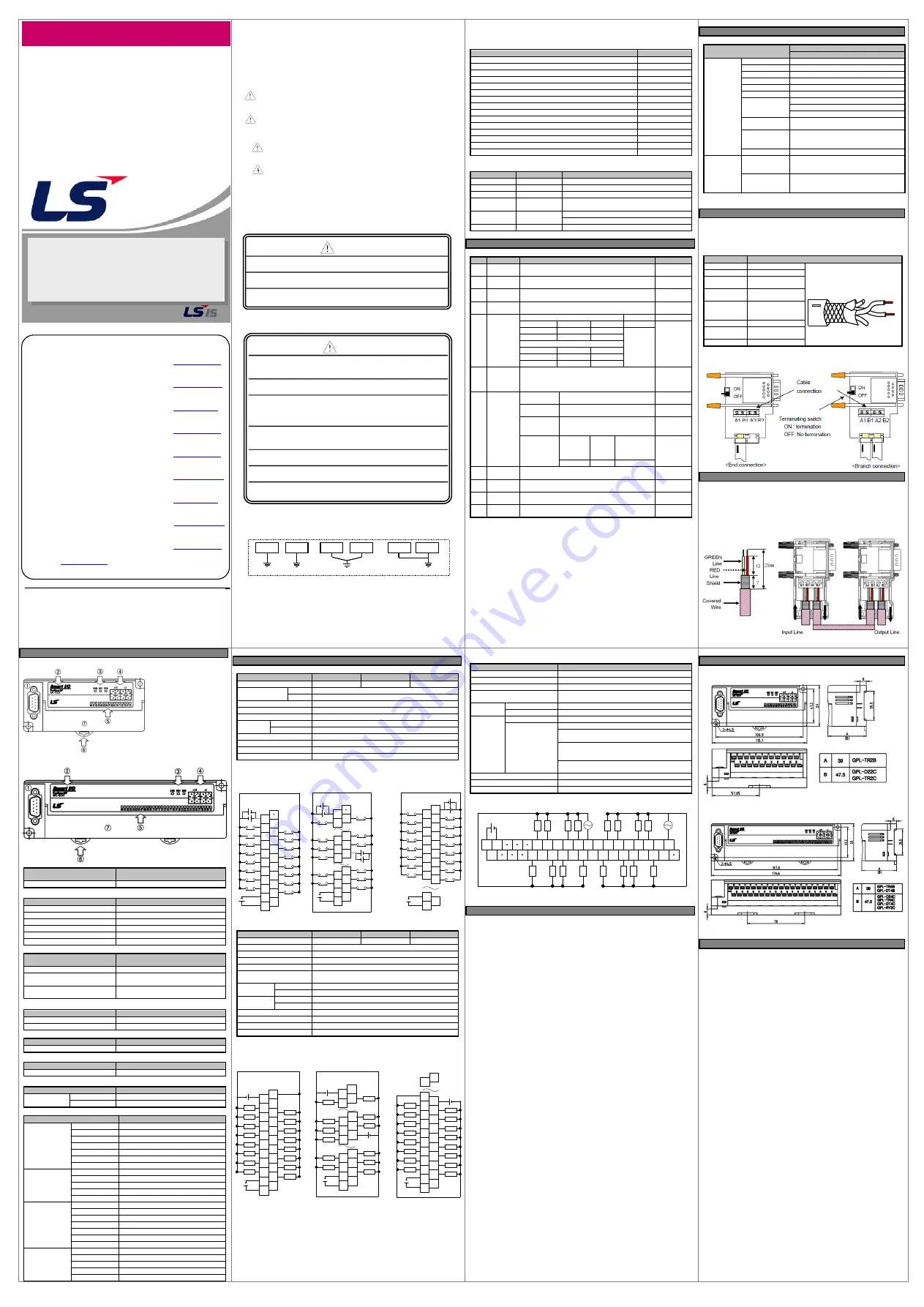
Related Manual
Read this data sheet carefully prior to any operation, mounting, installation or start-up of the
product.
Name
Code
GLOFA-GMWIN Programming software
10310000318
GLOFA-GMWIN Instruction & Programming
10310000377
GLOFA-GM/MASTER-K Smart I/O User’s manual
10310000353
GLOFA-GM Pnet I/F Module User’s Manual
10310000334
KGLWIN(Programming software)
10310000345
MASTER-K Instruction & Programming
10310000346
XG5000 Programming software
10310000512
XGK/XGB Instruction & Programming
10310000510
XGI/XGR/XEC Instruction & Programming
10310000833
XGK CPU series
10310000508
XGI CPU series
10310000832
XGB Hardware
10310000893
XGB Hardware (IEC)
10310000981
XGT Pnet I/F Module User’s Manual
10310000636
Smart I/O user manual
10310000353
Revision History
Publication
Version
Description
2003.07.
V1.0
The first edition
2005.06.
V1.1
Head office address and Group CI changed
2009.08.
V2.0
Branch address changed
2011.05
V3.0
KOREAN/ENGLISH data sheet integrated
CI Changed
2013.11
V3.1
Terminal block screwing torque added
Domain of Homepage changed
2014.04
V3.2
Terminal block drawing edited.
1. General Specifications
No
Item
Specification
Standard
1
Operating
temperature
0 ~ 55
℃
-
2
Storage
temperature
-25 ~ 70
℃
-
3
Operating
humidity
5 ~ 95%RH, non-condensing
-
4
Storage
humidity
5 ~ 95%RH, non-condensing
-
5
Vibration
resistance
For discontinuous vibration
-
-
Frequency
Acceleration
Amplitude
times
IEC61131-2
10≤f
∠
57 Hz
-
0.075 mm
10 times in
each
direction
for
X, Y, Z
57 ≤f≤150 Hz 9.8
㎨
(1G)
-
For continuous vibration
Frequency
Acceleration
Amplitude
10≤f
∠
57 Hz
-
0.035 mm
57≤f≤150 Hz 4.9
㎨
(0.5G)
-
6
Shocks
resistance
•
Max. impact acceleration : 147
㎨
(15G)
•
Authorized time : 11
㎳
•
Pulse wave : Sign half-wave pulse
(Each 3 times in X,Y,Z directions)
IEC61131-2
7
Noise
resistance
Square wave
impulse
noise
AC: ±1,500V
DC: ±900V
LSIS
standard
Electrostatic
discharge
Voltage: 4kV (Contact discharge)
IEC61131-2
IEC61000-4-2
Radiated
electromagnetic
field noise
80 ~ 1,000 MHz, 10 V/m
IEC61131-2
IEC61000-4-3
Fast transient
/burst noise
Segment
Power
supply
module
Digital/analog
input/output
communication
interface
IEC61131-2
IEC61000-4-4
Voltage
2 kV
1 kV
8
Ambient
conditions
No corrosive gas or dust
-
9
Operating
height
2000m or less
-
10
Pollution
degree
2 or less
-
11
Cooling
type
Natural air cooling
-
2. Performance Specifications
Items
Performance spec.
GPL-D22C/D24C/DT4B/C/TR2B/C/TR4B/C/RY2C
Transmission
spec.
Standard
EN50170 / DIN 19245
Interface
RS-485(Electric)
Media Access
POLL
Topologe
BUS Type
Encording Method NRZ
Cable type
Twisted Pair Shielded Cable
Comm. Distance
1200m(9.6k ~ 187.5 kbps)
400m(500kbps)
200m(1.5Mbps)
Max. Node
number
99
Max. Node
number
(per segment)
32
Max. I/O Data
Input : 4Byte / Output : 4Byte
Basic spec
External current
consumption(mA)
GPL-D22C : 70 / GPL-D24C : 85
GPL-DT4B/C : 100 / GPL-TR2B/C : 85
GPL-TR4B/C : 115 / GPL-RY2C : 160
Weight(g)
GPL-D22C : 188 / GPL-D24C : 286
GPL-DT4 B/C : 254/284 /GPL-TR2 B/C : 160/189
GPL-TR4 B/C : 255/285 / GPL-RY2C : 332
3. Cable Specifications
(1) Belden Network Cable
(a) Type : Network Components
(b) Protocol : FMS-DP-PA
(c) Certification : No
(d) Order No. : 3077F, 3079A
Item
Twinax
AWG
22
Type
BC-Bare Copper
Insulation
Method
PE-Polyethylen
Insulation
Thickness
0.035 (Inch)
Shield
Aluminum Foil-
Polyester Tape/Braid
Shield
Capacity
8500
㎊
/ft
Characteristic
Impedance
150
Ω
Core
2 Core
(2) Connector
4. Wiring of communication cable
(1) Wiring and Termination
(a) Please connect a GREEN line to A1,A2 and a RED line to B1,B2 in general.
In addition, Shield is connected to the clamp of connector.
(b) Please use cable of over 80% shield density.
(c) Please ensure that you have terminated both ends of each segment.
(d) If there are more than 0ne segment, it is necessary that you should
terminate every segment.
5. Parts Name and Descriptions
(1) GPL-D22C/TR2B/TR2C
(2) GPL-D24C/DT4B/DT4C/TR4B/TR4C/RY2C
Connector
Connector for connecting with
communication module
9-PIN Plug
9-pin female connector for Pnet
Part name display section
Display the Part name of Smart I/O
GPL-D22C
DC Input 16
GPL-D24C
DC Input 32
GPL-DT4B/DT4C
DC Input 16//TR Output 16
GPL-TR2B/TR2C
TR Output 16
GPL-TR4B/TR4C
TR Output 32
GPL-RY2C
RELAY Output 16
Communication LED
Display the status of communication
module
RUN
Display the status of power
RDY
Displays the communication status of
Comm. Module
ERR
Displays the abnormal err of comm..
module
Station Switch
0 ~ 99 (0:Reserved)
×
10
Set 10 digit of station number
×
1
Set 1 digit of station number
LED display section
Display the ON/OFF status of module
LED(0~15, 0~31)
Display the ON/OFF status of module
HOOK
HOOK
HOOK
Hook for mounting on DIN Rail
Screwing Part
Screwing Torque
Terminal block
screw
Screw tightening 3.7 kgf above
Screw loosening 3.7 kgf above
Terminal Block
In/Output terminal & Power input
GPL-D22C
/
GPL-D24C
0 ~ 15
Input terminal(GPL-D22C)
0 ~ 31
Input terminal(GPL-D24C)
COM
Common(16 points/COM)( GPL-D22C)
COM0/COM1
Common(16 points/COM)( GPL-D24C)
FG
Frame Ground
DC 24V
+24VDC Input terminal
DC 24G
-24VDC Input terminal
GPL-DT4B
/
GPL-DT4C
0 ~ 15/0 ~ 15
Input/Output terminal
COM0/COM1
Common(16 points/COM)
FG
Frame Ground
DC 24V
+24VDC Input terminal
DC 24G
-24VDC Input terminal
GPL-TR2B/C
/
GPL-TR4B/C
0 ~ 15
Output terminal(GPL-TR2B/TR2C)
0 ~ 31
Output terminal(GPL-TR4B/TR4C)
COM
Common(16 points/COM) (GPL-TR2B/C)
COM0/COM1
Common(16 points/COM) (GPL-TR4B/C)
FG
Frame Ground
24V
+24VDC Input terminal
24G
-24VDC Input terminal
GPL-RY2C
0 ~ 15
Output terminals
COMA~COMD
Common(8 points/COM)
FG
Frame Ground
DC 24V
+24VDC Input terminal
DC 24G
-24VDC Input terminal
6. Specification of Input/Output Module
(1) GPL-D22C/D24C/DT4B/DT4C(Input)
Specifications
GPL-D22C
GPL-D24C
GPL-DT4B/C
Number of input points
16 points
32 points
16 points
Rated Input
Current
B
7 mA
C/C1
5 mA
Operating Voltage Range
DC 20.4~28.8V(ripple: less than 5%)
ON Voltage
DC 19V or less
OFF Voltage
DC 6V or less
Response
Time
OFF
→
ON
0~3ms or less
ON
→
OFF
0~3ms or less
Common Terminal
16 points/COM
Operating indicator
LED turns on at ON state of input
External connections
Terminal block connector(M3
×
6 screws)
Insulation Method
Photo Coupler
(a) External Connection
<GPL-D22C> <GPL-D24C> <GPL-DT4B/C>
15
13
11
09
07
05
03
01
DC
24G
DC
24V
14
10
08
06
04
02
00
COM1
FG
12
+
+
-
-
13
11
09
07
05
03
01
DC
24G
DC
24V
10
08
06
04
02
00
COM
FG
12
15
COM
14
+
-
+-
+
-
+
-
30
18
16
15
03
01
DC
24G
DC
24V
31
17
04
02
00
FG
19
+
+
-
-
COM1
COM0
+ -
+
-
+
-
(2) GPL-TR2B/TR4B/DT4B/TR2C/TR4C/DT4C(Output)
Specifications
GPL-TR2B/C
GPL-TR4B/C
GPL-DT4B/C
Number of output points
16 points
32 points
16 points
Rated load voltage
DC 24V
Max. load current
0.5A/point, 3A/COM
OFF leakage current
0.1mA or less
Max. inrush current
4A /10ms or less
Maximum voltage drop
at ON circuit
DC 1.0V or less
External
Power supply
Voltage
DC 24V
±
10%(ripple voltage : 4Vp-p or less)
Current
30mA(TYP. All points On)
Response
Time
OFF
→
ON
1ms or less
ON
→
OFF
1ms or less
Common Method
16 points/COM
Operating Indicator
LED turns on at ON state of output
External connections
Terminal block connector (M3
×
6 screws)
Insulation method
Photo coupler
(a)
External Connection
<GPL-TR2B/C> <GPL-TR4B/C> <GPL-DT4B/C>
15
COM1
0V
13
11
09
07
05
03
01
DC
24G
DC
24V
10
08
06
04
02
00
FG
12
L
15
COM0
14
L
L
L
L
L
L
L
L
L
L
L
L
L
L
L
+ -
+
-
30
18
16
15
03
01
DC
24G
DC
24V
0V
31
17
04
02
00
FG
19
COM1
COM0
+
-
+ -
L
L
L
L
L
L
L
L
L
L
L
L
+
-
13
11
09
07
05
03
01
DC
24G
DC
24V
0V
10
08
06
04
02
00
COM
FG
12
L
15
COM
14
L
L
L
L
L
L
L
L
L
L
L
L
L
L
L
+
-
+
-
(3) GPL-RY2C
Specification
GPL-RY2C
Number of output points
16 points
Rated load voltage/current
DC24V/AC220V, 2A(Cos
ϕ
=1)/point 5A/COM
Minimum load voltage/current
DC 5V/1mA
Minimum load voltage/
Maximum switching frequency
AC 250V DC 110V, 1,200 times/hour
Response
Time
OFF
→
ON
10ms or less
ON
→
OFF
12ms or less
Service
Life
Mechanical
20 million times or more
Electrical
Rated load voltage/current 100,000 times or more
AC 200V/1.5A,AC 240V/1A(Cos
ϕ
=0.7) 100,000 times
or more
AC 200V/1A,AC 240V/0.5A(Cos
ϕ
=0.35) 100,000
times
or more
DC 24V/1A,DC 100V/0.1A(L/R=7ms) 100,000 times
or more
Common Method
8 points/COM
Operating Indicator
LED turns on at ON state of output
External connections
Terminal block connector(M3
×
6 screws)
(a) External Connection
DC
24V
DC
24G
01
02
05
06
09
10
13
14
COMA
COMA COMA
COMC
COMC COMC
FG
03
04
07
08
11
12
15
COMB
COMC
COMC
COMD
COMA
00
COMA
L
L
L
L
L
L
L
L
L
L
L
L
L
L
L
L
+ -
* Internally, The COMA and COMC are wired each other.
7. Precaution on installation
(1) When setting up the network, be sure not to duplicate the station number.
If there is any duplicated station number, the communication will not be established.
(2) Use cable complied with specification of this data sheet. Otherwise, it can cause serious
communication error.
(3) Make sure that communication cable connector fastened firmly. Otherwise, it can cause
serious communication error.
(4) Improper cable connection (snarled cable, redundant connection, etc) can cause
communication error.
(5) Do not place communication cable near power cable or inductive noise source.
(6) Change of station number will not take effect before power is re-applied.
8. Dimension (
㎜
)
(1) GPL-D22C/TR2B/TR2C
(2) GPL-D24C/TR4B/TR4C/DT4B/DT4C/RY2C
9. Warranty
(1) Warranty period
LSIS provides an 18-month-warranty from the date of the production.
(2) Warranty conditions
For troubles within the warranty period, LSIS will replace the entire PLC or
repair the troubled parts free of charge except the following cases.
(a) The troubles caused by improper condition, environment or treatment
except the instructions of LSIS.
(b) The troubles caused by external devices.
(c) The troubles caused by remodeling or repairing based on the user’s own
discretion.
(d) The troubles caused by improper usage of the product.
(e) The troubles caused by the reason which exceeded the expectation from
science and technology level when LSIS manufactured the product.
(f) The troubles caused by natural disaster.
(3) This warranty is limited to the PLC itself only. It is not valid for the whole system
which the PLC is attached to.
•
HEAD OFFICE
LS Tower, 127, LS-ro, Dongan-gu, Anyang-si,Gyeonggi-do, 431-848, Korea
Tel: 82-2-2034-4870
Fax: (82-2)2034-4648
e-mail:
•
LSIS(ME) FZE _ Dubai, U.A.E.
Tel: 971-4-886-5360
Fax: 971-4-886-5361
e-mail:
•
LSIS Tokyo Office _ Tokyo, Japan
Tel: 81-3-3582-9128
Fax: 81-3-3582-2667
e-mail:
•
LSIS Shanghai Office _ Shanghai, China
Tel: 86-21-5237-9977(609) Fax: 89-21-5237-7189 e-mail:
•
LSIS Beijing Office _ Beijing, China
Tel: 86-10-5825-6027(666) Fax: 86-10-5825-6028 e-mail:
•
LSIS Guangzhou Office _ Guangzhou, China
Tel: 86-20-8328-6754
Fax: 86-20-8326-6287 e-mail:
•
LSIS Chengdu Office _ Chengdu, China
Tel: 86-20-8328-6754
Fax: 86-20-8326-6287 e-mail:
•
LSIS Qingdao Office _ Qingdao, China
Tel: 86-532-8501-6068
Fax: 86-532-8501-6057 e-mail:
•
LSIS Europe B.V., Netherlands
Tel: +31 (0)20 654 1420
Fax: +31(0)20 654 1429 e-mail:
•
Homepage:
LS constantly endeavors to improve our products so that information in this
datasheet is subject to change without notice
.
The date of issue: 2013. 11
10310000448 Ver 3.2
GPL-TR2B
GPL-TR4B
GPL-DT4B
GPL-D22C
GPL-D24C
GPL-DT4C
GPL-TR2C
GPL-TR4C
GPL-RY2C
LS Programmable Logic Controller
Pnet(Profibus-DP) I/F Module
DATA SHEET
- When using LSIS equipment, thoroughly read this
datasheet and associated manuals introduced in this
datasheet. Also pay careful attention to safety and handle
the module properly.
- Store this datasheet in a safe place so that you can take it
out and read it whenever necessary.
Smart I/O
Caution
►
Be sure to check the rated voltage and terminal arrangement for the
module before wiring work.
Risk of electric shock, fire and malfunction.
►
Tighten the screw of terminal block with the specified torque range.
If the terminal screw is loose, it can cause fire and electric shock.
►
Use the PLC in an environment that meets the general
specifications contained in this datasheet.
Risk of electrical shock, fire, erroneous operation and deterioration of the
PLC.
►
Be sure that external load does not exceed the rating of output
module.
Risk of fire and erroneous operation.
►
Do not use the PLC in the environment of direct vibration
Risk of electrical shock, fire and erroneous operation.
►
Do not disassemble, repair or modify the PLC.
Risk of electrical shock, fire and erroneous operation
►
When disposing of PLC and battery, treat it as industrial waste.
Risk of poisonous pollution or explosion.
Precautions for use
►
Do not Install other places except PLC controlled place.
►
Make sure that the FG terminal is grounded with class 3 grounding which is
dedicated to the PLC. Otherwise, it can cause disorder or malfunction of PLC
►
Connect expansion connector correctly when expansion module is needed.
►
Do not detach PCB from the case of the module and do not modify the module.
►
Turn off power when attaching or detaching module.
►
Cellular phone or walkie-talkie should be farther than 30cm from the PLC.
►
Input signal and communication line should be farther than 10cm from a high-
tension and a power line in order not to be affected by noise and magnetic field.
A) Best
B) Good
C) Bad
Others
PLC
Others
PLC
PLC
Others
Safety Precautions
►
Safety Precautions is for using the product safely and correctly in order to prevent
the accidents and danger, so please go by them.
►
The precautions explained here only apply to this module. For safety precautions
on the PLC system, refer to User’s manual.
►
The precautions are divided into 2 sections, ‘Warning’ and ‘Caution’. Each of the
meanings is represented as follows.
If you violate instructions, it can cause death, fatal injury or a
considerable loss of property
If you violate instructions, it can cause a slight injury or a slight
loss of products
►
The symbols which are indicated in the PLC and User’s Manual mean as follows.
This symbol means paying attention because of danger of injury, fire,
or malfunction
►
This symbol means paying attention because of danger of electric shock.
Store this datasheet in a safe place so that you can take it out and read
it whenever necessary. Always forward it to the end user
Handing Precautions
►
Don’t drop or make impact.
►
Don’t detach PCB from case. It may cause problem.
►
When wiring, let no foreign material go into the module. If it goes into the module,
remove it.
►
Don’t detach the module from slot while power is on
Warning
►
Do not contact the terminals while the power is applied.
Risk of electric shock and malfunction.
►
Protect the product from being gone into by foreign metallic matter.
Risk of fire, electric shock and malfunction.
►
Risk of fire, electric shock and malfunction.
Risk of injury and fire by explosion and ignition.
Warning
Caution
Содержание Smart I/O
Страница 2: ......