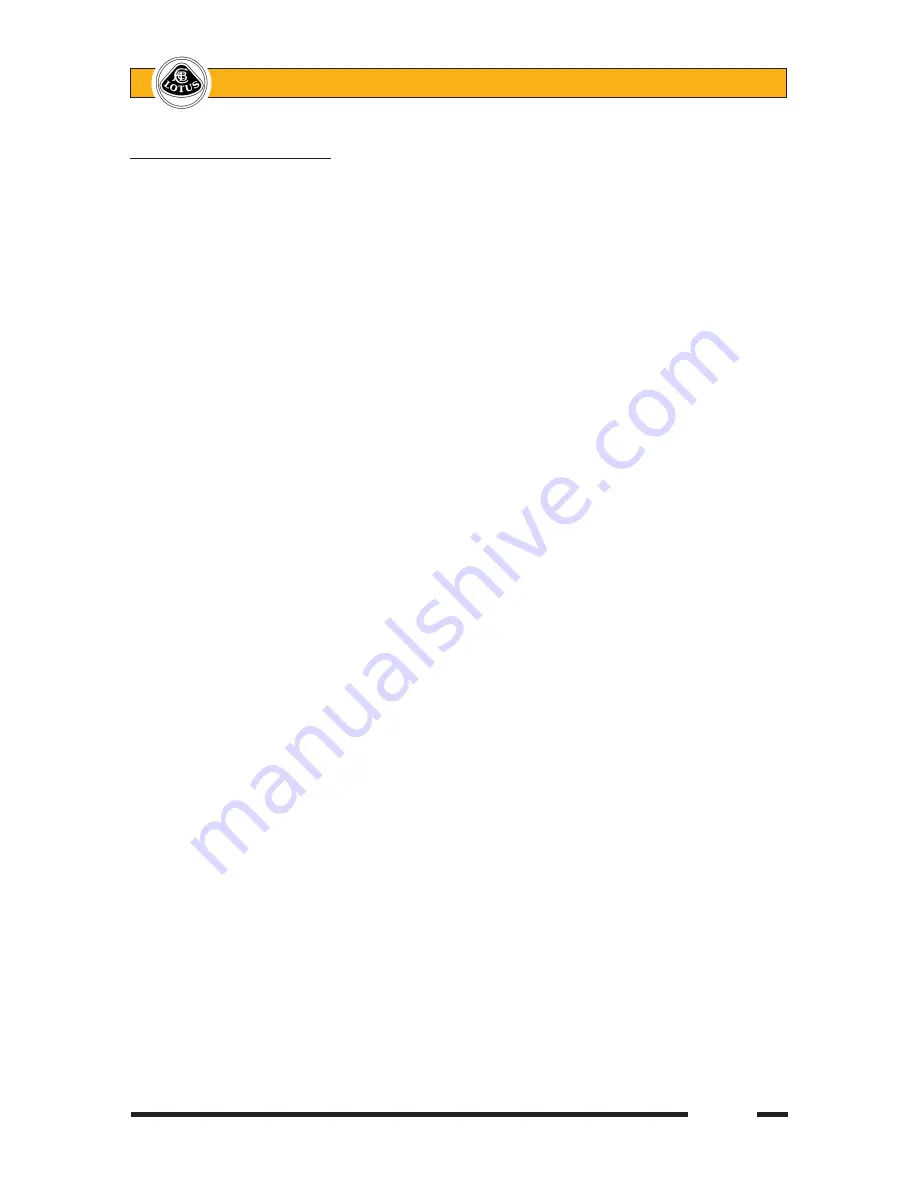
Page 3
Lotus Service Notes
Section AJ
AJ.1 - GENERAL DESCRIPTION
The chassis frame of the Lotus Eagle is constructed primarily from aluminium alloy extrusions and formed
alloy sheet, with the various sections bonded together using an epoxy adhesive with secondary drive-in fasten-
ers. The main chassis unit includes the passenger cell, footwells, front bulkhead, front scuttle with door hinge
posts and the fuel tank bay. At the rear, the main chassis siderails extend rearwards beyond the fuel tank bay
and alongside the engine bay, to terminate in mounting faces for the galvanised steel rear subframe. Similarly,
the front bulkhead/toe board provides mountings for the alloy front subframe. A large diameter tubular steel
seat belt mounting frame is bolted to the top face of the chassis side members, and incorporates a roof hoop
with backstays for additional occupant protection.
The cabin rear bulkhead, body sills (inc. 'B' posts), roof panel, and windscreen mounting frame, are all
constructed from glass fibre composite and are bonded to the chassis structure using an elastomeric adhesive.
The front and rear outer body clamshells are each constructed from glass fibre composite mouldings, fixed to
the body and chassis structure with threaded fasteners to facilitate service access and economic repair.
Two main chassis siderail extrusions, 226mm wide and 80mm deep, each comprising three box sections,
run along each side of the passenger compartment between the front and rear subframe mountings. Each
member incorporates two bends to allow the siderails to angle inwards afore and behind the seating area in
order to accommodate the wheel wells. Each bend is formed by notching the extrusion, bending the outer wall
and restoring the three cut faces with bonded and riveted patches. The front joint is reinforced by an inboard
gusset panel, and the rear joint by the fuel tank crossmember. At the rear, each siderail is raised above the
lower wishbone front pivot by having the siderail lowermost section machined away, and adding a folded up-
per gusset to the siderail top surface, to reinforce a vertical end face used for attachment of the rear subframe
supension tower.
Five crossmembers link the bottom of the two siderails; one at the toe-board, two bonded together at the
seat front mountings, one for the seat rear mountings, and one across the front of the fuel tank bay. Two single
skin sheet sections are used to complete the cabin floor.
Behind the passenger cell, the siderails are linked by a pair of transverse crossmembers which are used
in conjunction with a folded sheet upper panel to form an open bottomed fuel tank cell with a detachable, screw
fixed, lower closing panel. Note that this closing panel contributes to the structural integrity of the chassis, such
that the vehicle should not be operated without it properly fitted.
The front scuttle structure comprises a scuttle beam, the two door hinge posts and the foowells. A verti-
cal extrusion is used to form each door hinge post, which is secured to the end of the scuttle beam, and, by a
rearwards leading tapering channel section, to the chassis siderail. Perforated flat plates are also used to tie
the lower ends of the hinge posts to the siderails. The folded sheet footbox links the front of the scuttle beam to
the siderails, the toe-board and to vertical strongpoints which are used to terminate the front end of the siderails
and provide mounting points for the front subframe.
A galvanised, sheet steel, fabricated rear subframe, provides mountings for the rear suspension, powertrain
and exhaust muffler, and is bolted to the rear ends of the chassis siderails. The subframe also serves as a de-
formable crash structure to provide the necessary energy dissipation in the event of a rear impact. This feature
also facilitates accident repair by separating the suspension mounting points from the main chassis structure.
At the front of the car, a front subframe uses the same construction techniques as the main chassis tub,
with aluminium alloy extrusions bonded and riveted together to provide mounting points for the front suspension,
front body clamshell and cooling radiators, and also houses the heating/a.c. system. The structure consists
primarily of a box section extrusion at each side, continuing forwards from the front of the chassis tub to which
each side is fixed by a 6 bolt flange. These two longerons, house the mounting points for the top wishbone
pivots and carry drop towers down to the lower wishbone pivots. The foremost of these are linked by a lower
crossmember which also carries the power steering rack, with the whole area reinforced by a bolted upper
crossmember/bulkead panel forming the front of the HVAC chamber. The front ends of the longerons are linked
by another crossmember secured at each side by two M8 fixings. The construction of the subframe also serves
to dissipate energy and control the rate of deceleration sustained by the occupants in a frontal collision. As
at the rear, this feature also facilitates accident repair by separating the suspension mounting points from the
main chassis structure.
Note that the whole of the chassis structure as so far described, is machined to allow assembly into right
or left hand drive configuration.
The bonded and rivetted main chassis tub described above is considered a non-serviceable single unit,
jig built to fine tolerances, to which no structural repairs are approved. Superficial, cosmetic, or non-structural
localised damage may be cosmetically repaired as necessary, but in the case of accident damage resulting
Содержание Evora
Страница 13: ...Page 7 Lotus Service Notes Section AJ ...
Страница 81: ... Lotus Service Notes Section EMR Page 9 EMR 3 COMPONENT LOCATION em239 O2 O2 O2 O2 2009 02 ...
Страница 82: ...Page 10 Lotus Service Notes Section EMR em240 2009 02 ...
Страница 115: ... Lotus Service Notes Section EMR Page 43 2009 02 ...
Страница 116: ...Page 44 Lotus Service Notes Section EMR 2009 02 ...
Страница 118: ...Page 46 Lotus Service Notes Section EMR 2009 02 ...
Страница 184: ...Page 2 Lotus Service Notes Section JL GENERAL LAYOUT TBA ...
Страница 207: ...Page 25 Lotus Service Notes Section JL ...
Страница 233: ...Page 9 Lotus Service Notes Section MR Blank page ...
Страница 259: ...Page 35 Lotus Service Notes Section MR ...
Страница 260: ...Page 36 Lotus Service Notes Section MR ...
Страница 261: ...Page 37 Lotus Service Notes Section MR ...
Страница 262: ...Page 38 Lotus Service Notes Section MR ...
Страница 263: ...Page 39 Lotus Service Notes Section MR ...
Страница 264: ...Page 40 Lotus Service Notes Section MR ...
Страница 265: ...Page 41 Lotus Service Notes Section MR ...
Страница 266: ...Page 42 Lotus Service Notes Section MR ...
Страница 267: ...Page 43 Lotus Service Notes Section MR ...
Страница 268: ...Page 44 Lotus Service Notes Section MR ...
Страница 269: ...Page 45 Lotus Service Notes Section MR ...
Страница 270: ...Page 46 Lotus Service Notes Section MR ...
Страница 271: ...Page 47 Lotus Service Notes Section MR ...
Страница 272: ...Page 48 Lotus Service Notes Section MR ...
Страница 273: ...Page 49 Lotus Service Notes Section MR ...
Страница 274: ...Page 50 Lotus Service Notes Section MR ...
Страница 275: ...Page 51 Lotus Service Notes Section MR ...
Страница 276: ...Page 52 Lotus Service Notes Section MR ...
Страница 277: ...Page 53 Lotus Service Notes Section MR ...
Страница 278: ...Page 54 Lotus Service Notes Section MR ...
Страница 279: ...Page 55 Lotus Service Notes Section MR ...
Страница 280: ...Page 56 Lotus Service Notes Section MR ...
Страница 281: ...Page 57 Lotus Service Notes Section MR ...
Страница 282: ...Page 58 Lotus Service Notes Section MR ...
Страница 283: ...Page 59 Lotus Service Notes Section MR ...
Страница 284: ...Page 60 Lotus Service Notes Section MR ...
Страница 285: ...Page 61 Lotus Service Notes Section MR ...
Страница 286: ...Page 62 Lotus Service Notes Section MR ...
Страница 287: ...Page 63 Lotus Service Notes Section MR ...
Страница 288: ...Page 64 Lotus Service Notes Section MR ...
Страница 289: ...Page 65 Lotus Service Notes Section MR ...
Страница 290: ...Page 66 Lotus Service Notes Section MR ...
Страница 291: ...Page 67 Lotus Service Notes Section MR ...
Страница 292: ...Page 68 Lotus Service Notes Section MR ...
Страница 293: ...Page 69 Lotus Service Notes Section MR ...
Страница 294: ...Page 70 Lotus Service Notes Section MR ...
Страница 295: ...Page 71 Lotus Service Notes Section MR ...
Страница 296: ...Page 72 Lotus Service Notes Section MR ...
Страница 297: ...Page 73 Lotus Service Notes Section MR ...
Страница 298: ...Page 74 Lotus Service Notes Section MR ...
Страница 299: ...Page 75 Lotus Service Notes Section MR ...
Страница 300: ...Page 76 Lotus Service Notes Section MR ...
Страница 301: ...Page 77 Lotus Service Notes Section MR ...
Страница 302: ...Page 78 Lotus Service Notes Section MR ...
Страница 303: ...Page 79 Lotus Service Notes Section MR ...
Страница 304: ...Page 80 Lotus Service Notes Section MR ...
Страница 305: ...Page 81 Lotus Service Notes Section MR ...
Страница 306: ...Page 82 Lotus Service Notes Section MR ...
Страница 307: ...Page 83 Lotus Service Notes Section MR ...
Страница 336: ...Page 2 Lotus Service Notes Section QJ GENERAL LAYOUT Illustration TBA ...
Страница 357: ...Page 2 Lotus Service Notes Section WF Illustration to follow ...