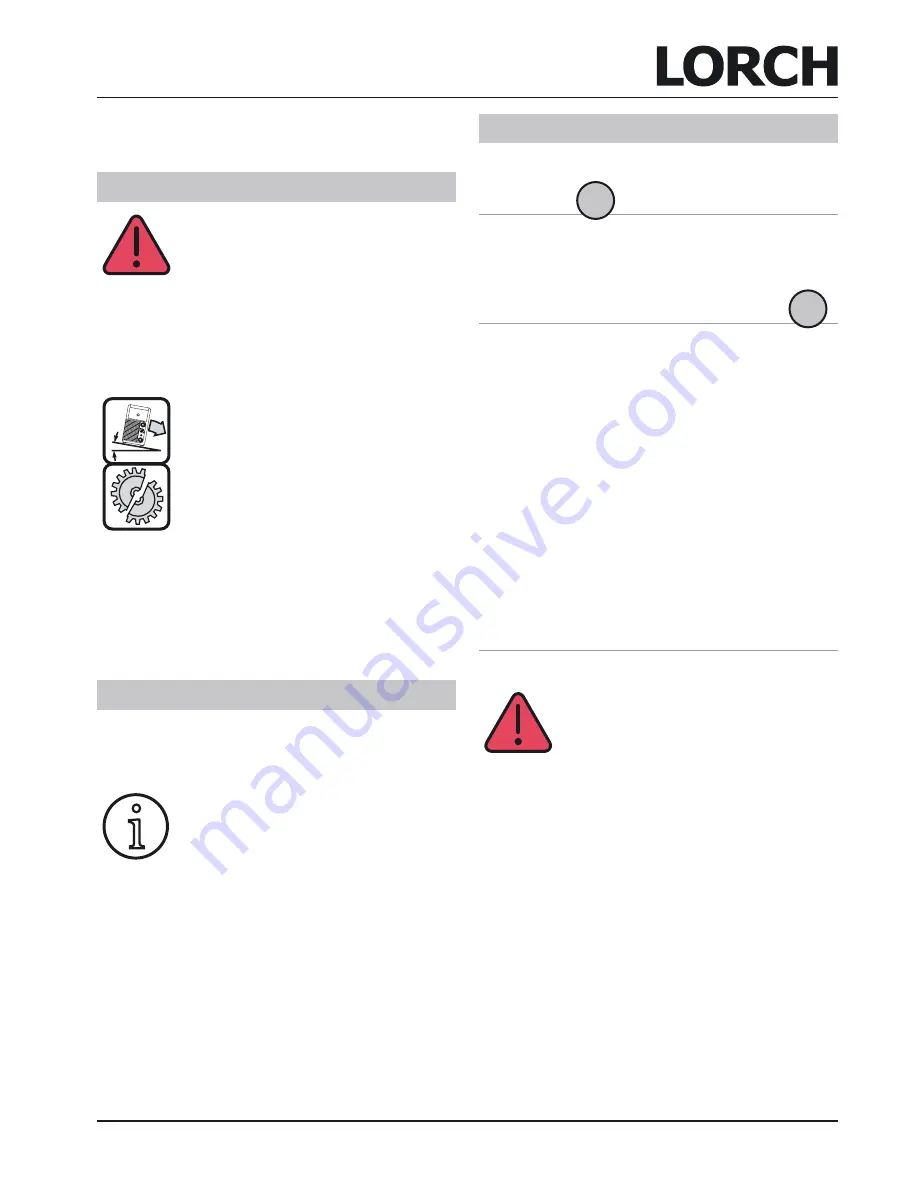
Before start-up
909.2049.9-00
- 21 -
01.14
caused by electromagnetic fields (possibly with technical
assistance by the manufacturer).
10 Setup and transport
Danger of injury due to the device falling
over and crashing.
Before transport, disconnect the mains plug.
Carry the device using the transportation belt
and keep it in a horizontal position.
Do not use a fork-lift truck or similar device to
lift the machine by its housing or transporta-
tion belt.
The machine must be set up only on firm,
level and dry surfaces. The maximum admis-
sible angle of inclination for setting up is 10°.
Therefore, always ensure that the cooling air
openings are always uncovered.
–
Do not set up the device directly by a wall.
–
Do not cover any cooling air openings.
The device may overheat and be damaged.
Cooling air openings are located on the
–
Front side of the housing
–
Rear side of the housing
11 Brief operating instructions
Â
Connect the mains or battery cable.
Â
Connect the component guide and electrode holder to the
sockets 3 and 4.
Observe the polarity according to the data of
the electrode manufacturer (see also elec-
trode welding).
Â
Tension the stick electrode on the electrode holder.
Â
Switch the machine on by pressing the On/Off button
17 for 2 sec..
Â
Select the desired electrode operating mode using the
16 button.
Â
Set the desired welding current using the rotary knob
12.
9
The machine is now ready for welding.
12 Before start-up
12.1 Fastening the transportation
belt
II
Â
Thread the transportation belt 1 into the welding ma-
chine and plastic slides 8. See sequence of the num-
bering in the picture.
12.2 Connecting the ground cable
III
When selecting the working space, ensure that the
ground cable and the ground clamp can be fastened
properly.
The ground clip must be fastened to an exposed
location of the welding table or component, so that it is
highly conductive. It must be located in the immediate
vicinity of the welding area, so that the welding current
cannot seek its own return path across machine parts,
ball bearings or electric circuitry.
Do not place the ground clamp on the welding ma-
chine, as otherwise the welding current will be carried
via the protective conductors and it will destroy these.
Never attach the workpiece connection loosely. Connect
the ground clamp firmly to the welding bench or the
workpiece.
12.3 Connecting the power supply
Mains cable with device coupling
Danger of death through electrocution!
If the plug-in mains cable is used incor-
rectly when humidity or moisture is pre-
sent, particularly outdoors, then electro-
cution is possible.
When working in mains operation, ob
-
serve the following:
First, connect the mains cable to the ma-
chine coupling on the welding machine
and then connect the mains cable to the
mains plug in the mains socket.
Always disconnect the mains plug from
the mains socket before disconnecting
the machine coupling.
Mains operation
Before commissioning the machine, ensure that a suit-
able mains connection is available. The fuse must meet
the requirements stated in the technical data.
i
Содержание MicorStick
Страница 1: ...909 2049 9 00 EN Operation Manual Page 17 MicorStick ...
Страница 3: ... 909 2049 9 00 3 01 14 MicorStick MobilePower 1 2 3 4 ...
Страница 4: ... 4 01 14 909 2049 9 00 1 2 3 4 7 6 5 8 1 53 54 51 50 55 56 I II IV 2 1 1 1 L1 R L2 S L3 T N MP PE III ...
Страница 5: ... 5 01 14 909 2049 9 00 3 58 62 63 66 60 61 65 64 10 11 12 13 14 15 16 17 18 V VI VII VIII ...
Страница 18: ... 117 01 14 909 2049 9 00 ...