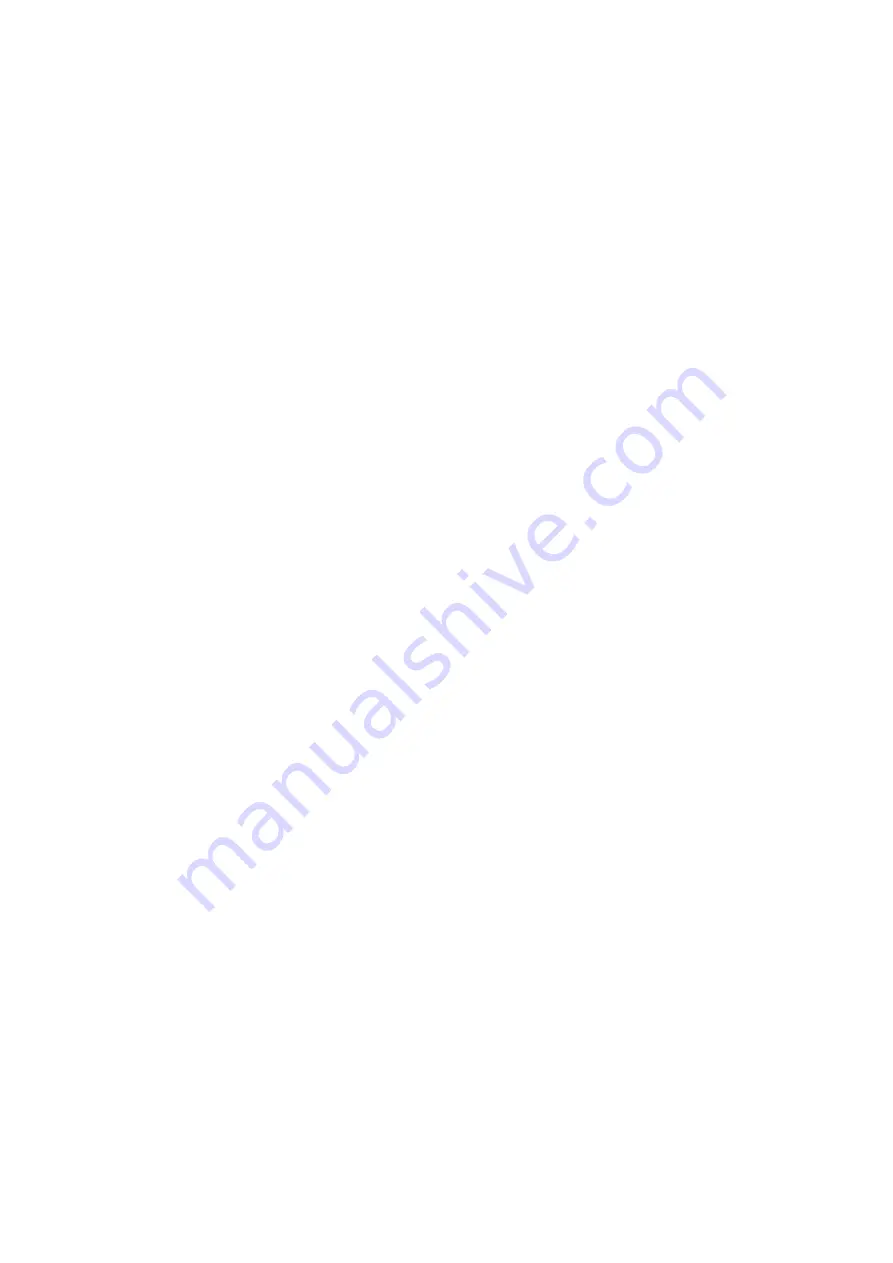
52
Bad performance of engine under low speed or idling speed
Diagnosis Cause
1
、
Check ignition timing and valve clearance
→Incorrect→ 1
、
CDI failure
Correct 2
、
Magneto failure
。
3
、
Sensor failure
4
、
Too narrow the valve clearance
2
、
Check joint and leakage of carburetor
→Leakage is found 1. Distortion of seal ring of carburetor
No leakage 2. Loose and drop of carburetor joint
3
、
Fracture of sealing ring
3
、
Check sparkover of spark plug
→Weak spark or sparkover of intermittent→ 1
、
Spark plug damaged
Normal spark 2
、
Magneto failure
3
、
Ignition coil failure
4
、
CDI Failure
5
、
Sensor failure
6
、
Ignition switch failure
7
、
Spark plug cap failure
8
、
Wrong connection or short circuit in
power source circuit
Bad performance when engine under high speed
Diagnosis
Cause
1
、
Check valve clearance and ignition timing
→Incorrect→ 1
、
Magneto failure
Correct
2
、
CDI failure
3
、
Sensor failure
4
、
Incorrect valve clearance
2
、
Open fuel tube of carburetor
→Fuel flow was limited→ 1
、
Fuel in fuel tank used up
Fuel smoothly flow out 2
、
Ventilation hole on fuel tank cap blocked
3
、
Fuel tube from fuel tank to carburetor
blocked
4
、
Fuel switch blocked
5
、
Gasoline filtering screen blocked
6
、
Bad connection negative pressure tube
of fuel tube
3
、
Check carburetor
→Carburetor blocked→
1
、
Float needle blocked
Carburetor unblocked
2
、
Low level of fuel float
3
、
Main jet of carburetor blocked
4
、
Float seized up
4
、
Check gas distribution timing
→Incorrect→ 1. Incorrect installation for timing chain and sprocket wheel
Correct 2.Heavy abrasion of gear
5
、
Check sparkover of spark plug under high speed
→Abnormal→ 1
、
Magneto failure
Normal sparkover
2
、
CDI failure