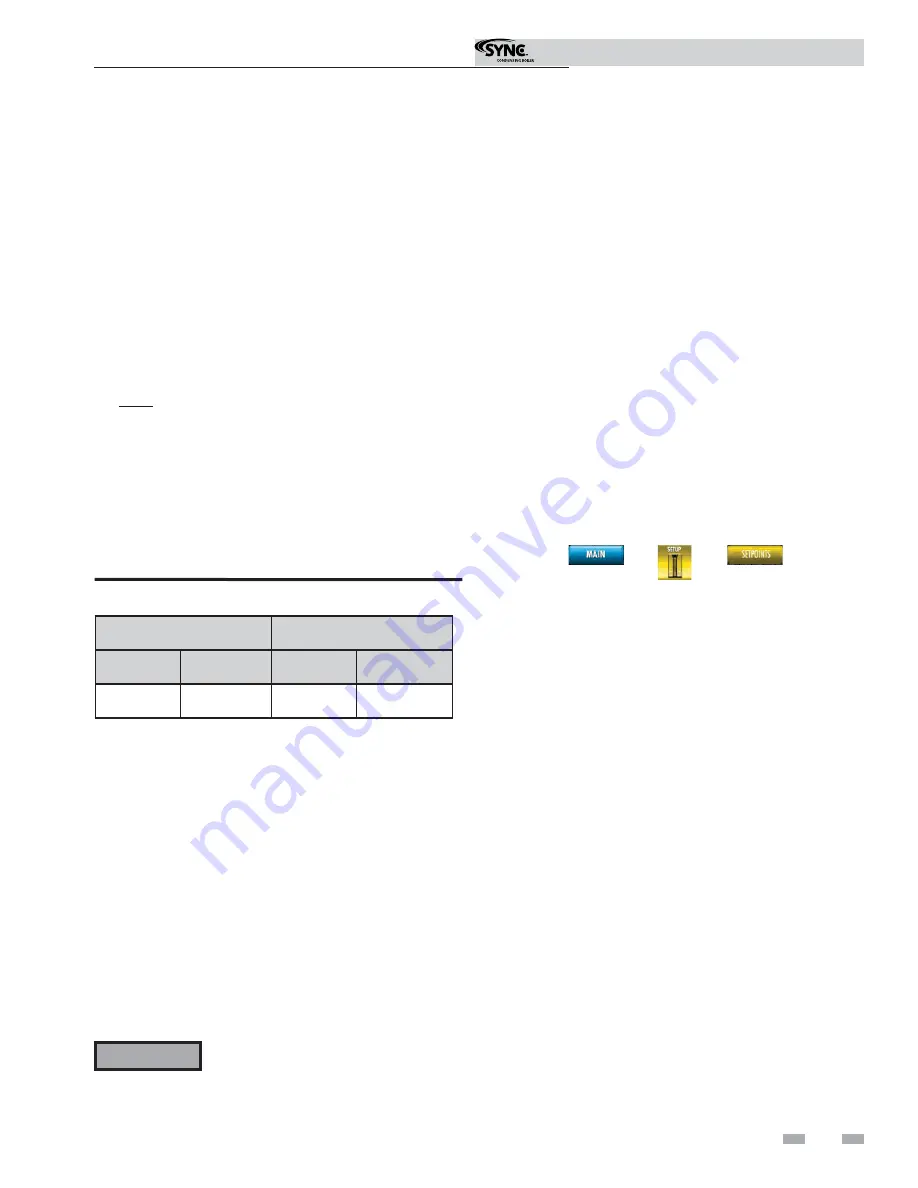
47
Installation & Operation Manual
9
Start-up
(continued)
Check flame and combustion
(continued)
4. Navigate to the Service Mode Screen from the Status
Screen by pressing the MAIN button and then the
SERVICE MODE button.
5. On the Service Screen place Heat Exchanger 1 into
operation by selecting Heat Exchanger 1 with the SELECT
button and turning the heat exchanger on by pressing the
ON/OFF button (OFF indicates that the heat exchanger
is off and ON indicates that the heat exchanger should be
firing).
6. Insert the probe from a combustion analyzer into the hole
left by the removal of the flue temperature sensor.
Note:
Heat Exchanger 1 is the top heat exchanger; please
ensure the probe is in the top flue sensor location.
7. Once the heat exchanger has modulated up to full fire
measure the combustion. The values should be in
the range listed in Table 9A below. CO levels should
be less than 200 ppm for a properly installed unit.
If the combustion is not within range reference the
Troubleshooting
Section in the SYNC Service Manual for
possible causes and corrective actions.
Set space heating operation
Verify space heat circulator mode
The Space Heating Mode controls the system pump (if
connected), and both boiler pumps. When the SMART
TOUCH control receives a space heating call for heat, it turns
on the system pump. If the boiler is not heating an indirect
HW (Hot Water) tank, it also turns on the boiler pump. After
the space heating call for heat ends, the system pump continues
to run for a short period of time. If the boiler pump was
running, it continues to run for a short period of time as well.
These pump delays are factory set to 30 seconds. If different
delays are desired, the appropriate parameters in the control
must be changed. See the SYNC Service Manual for a detailed
explanation of this procedure.
Set space heating set point temperature
During normal operation, space heating set point temperatures
can be adjusted from the Set Points Menu. Press the following
buttons to navigate to the Set Points Menu from the Status
Screen:
1. To change a set point, press the SELECT button next to the
user set point parameter.
2. The first time the user set point parameter is accessed, you
will be required to enter the user password. The user
password is 0704.
3. Using the keypad, enter the password and then press the
OK button. If the password is not entered correctly, the
screen will revert to the Parameter List Screen and you
will not be able to adjust the set point. If a digit has been
entered incorrectly, press the left arrow key on the keypad
to back the digit up. If the password has been entered
correctly, the Parameter Change Screen will appear. The
Parameter Change Screen will display the set point being
changed, the previous setting of the set point, and
adjustment buttons.
4. To adjust the set point, press the + or - buttons to change
the value being displayed.
5. Once the set point has been adjusted to the desired
setting press the APPLY button to change the set point
and return to the Parameter List Screen.
Table 9A Flue Products Chart
8. Once the Heat Exchanger 1 analysis is complete, test the
safety shutoff device by turning the manual shutoff valve
to the OFF position and ensuring that Heat Exchanger
1 shuts down and registers an alarm. Open the manual
shutoff valve, reset the control, and return to Service
Mode.
9. Repeat the same procedure for Heat Exchanger 2
by selecting Heat Exchanger 2 while on the Service
Mode Screen. Be certain to insert the probe from the
combustion analyzer into the Heat Exchanger 2 flue
temperature sensor location.
10. Turn the main power off to the boiler and replace the
flue temperature sensor into the flue pipe connection.
11. Place the boiler back into normal operation.
You must replace the flue gas temperature
sensor to prevent flue gas spillage into
the room. Failure to comply could
result in severe personal injury, death, or
substantial property damage.
WARNING
Natural Gas
Propane
CO
2
O
2
CO
2
O
2
8.0% - 10%
3.0% - 6.5%
9.0% - 11%
4.1% - 6.9%
>>
>>
Содержание Sunc 1.0
Страница 66: ...66 Notes...
Страница 67: ...67 Notes...