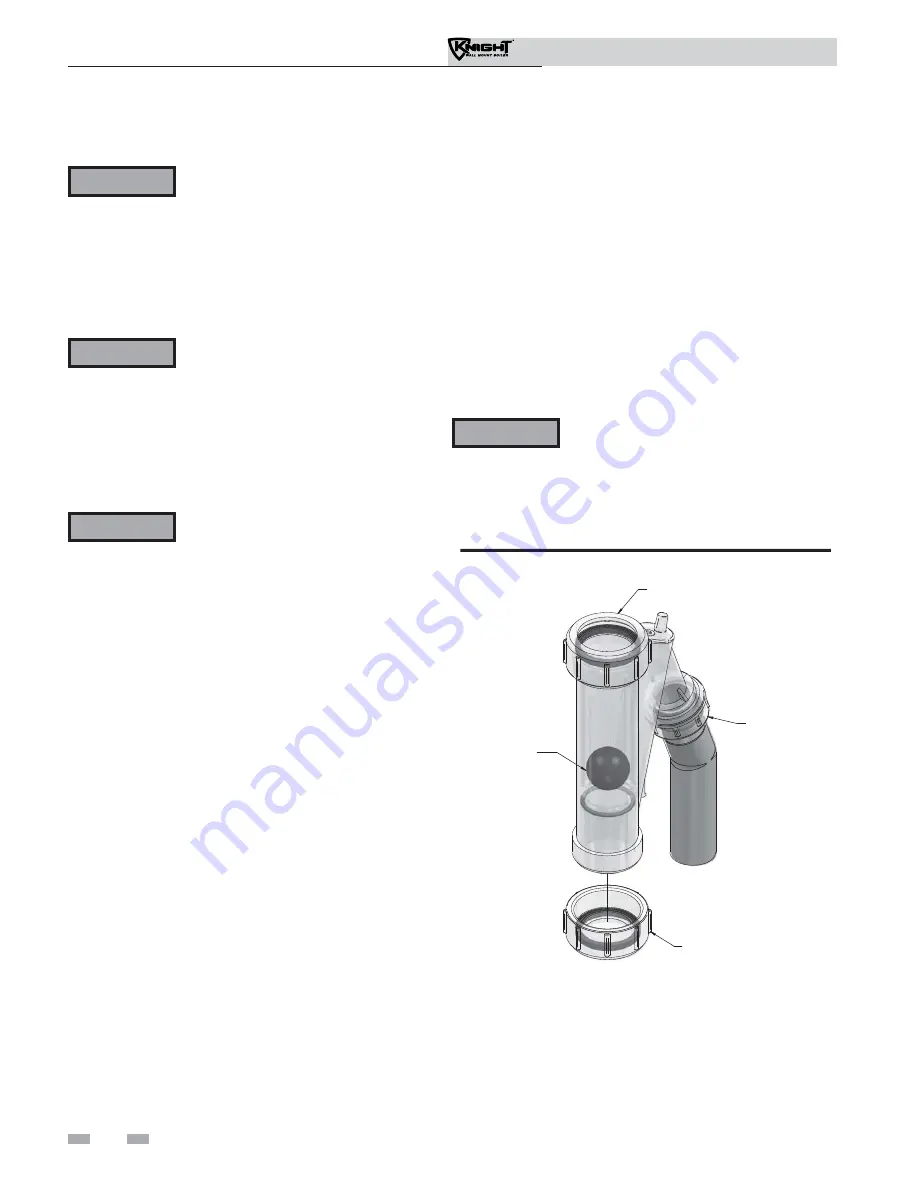
58
Installation & Operation Manual
10
Start-up
Check for gas leaks
Before starting the boiler, and during
initial operation, smell near the floor and
around the boiler for gas odorant or any
unusual odor. Remove the front access
panel and smell the interior of the boiler
enclosure. Do not proceed with startup
if there is any indication of a gas leak.
Use an approved leak detection solution.
Repair any leaks at once.
DO NOT adjust gas valve outlet pressure.
The gas valve is factory set for the correct
outlet pressure. This setting is suitable
for natural gas and propane, requiring
no field adjustment. Attempting to
alter the gas valve outlet pressure could
result in damage to the valve, causing
potential severe personal injury, death, or
substantial property damage.
Propane boilers only – Your propane
supplier mixes an odorant with the propane
to make its presence detectable. In some
instances, the odorant can fade, and the
gas may no longer have an odor. Before
startup (and periodically thereafter), have
the propane supplier verify the correct
odorant level in the gas.
Inspect/fill condensate system
Inspect/check condensate lines and fittings
1. Inspect the condensate drain line, condensate fittings and
condensate trap.
2. Fill condensate trap with enough water to make the ball
float (FIG. 10-1).
3. Loosen compression fitting (FIG. 10-1).
4. Slide condensate trap onto condensate drain at the bottom
of the unit.
5. Tighten compression fitting.
The condensate trap (FIG. 10-1) must have
the float ball in place during all times of
boiler operation to avoid flue gas emission
from the condensate drain line. Failure to
ensure the float ball is in place could result in
severe personal injury or death.
CONDENSATE
DRAIN
REMOVABLE CAP TO
CLEAN OUT TRAP
COMPRESSION
FITTING
FLOAT BALL
IMG00209
Figure 10-1 Condensate Trap
WARNING
WARNING
WARNING
WARNING
Clean/Inspect Trap Assembly
1. Remove the clean out cap on the bottom of the trap. Let the
condensate and any debris drain out.
2. Refill the trap according to the instructions above.
Check thermostat circuit(s)
1. Disconnect the two external wires connected to each
of the heat/loop demand terminals on the connection
board.
2. Connect a voltmeter across these two incoming wires.
Close each thermostat, zone valve, and relay in the
external circuit one at a time and check the voltmeter
reading across the incoming wires.
3. There should NEVER be a voltage reading.
4. If a voltage does occur under any condition, check and
correct the external wiring. (This is a common problem
when using 3-wire zone valves.)
5. Once the external thermostat circuit wiring is checked and
corrected if necessary, reconnect the external thermostat
circuit wires to the connection board.