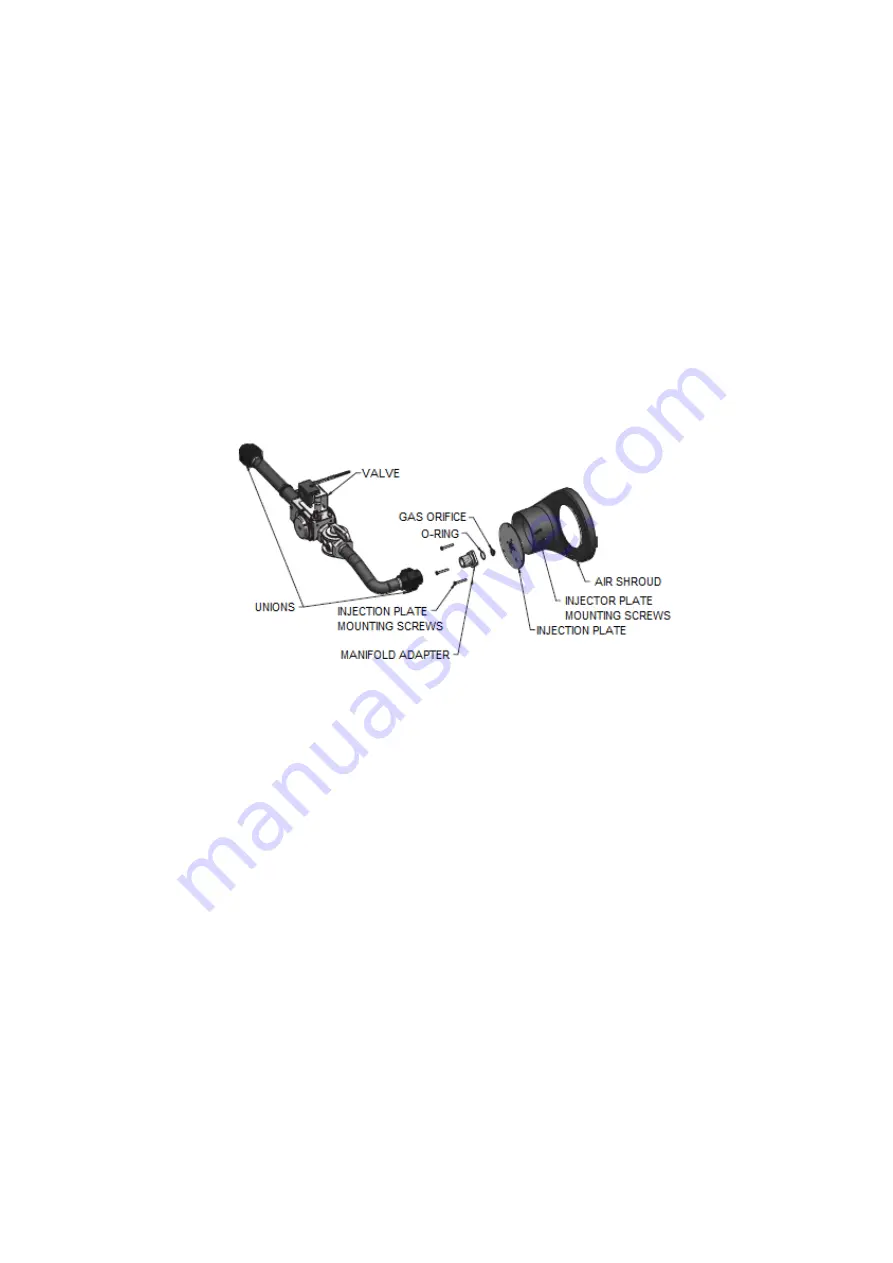
44
14.2.4
EKW145CE (FROM SERIAL NUMBER L09H10120786)
1.
Remove the top and front access covers from the unit (no tools required for removal).
2.
Remove the gas valve and manifold from the unit via the unions on each end (
Figure 14.4
).
3.
Remove the three screws mounting the injector plate on the air shroud (
Figure 14.4
).
4.
Remove the four screws securing the manifold adapter to the injector plate taking care not to damage the
O-ring.
5.
Locate the propane orifice disk from the conversion kit bag. Verify that the stamping on the orifice disk is
correct for the heater (see
Table 14.1
).
6.
Remove the existing orifice from the O-ring in the side of the injector plate and replace it with the orifice
from the kit. Position and secure the orifice in the injector plate as shown in
Figure 14.4
.
7.
Reposition the manifold adapter to the injector plate and replace the four manifold adapter mounting
screws. Handle the O-ring with care, do not damage.
8.
Reposition the injector plate to the air shroud and replace the three injector plate mounting screws.
9.
After installation is complete, attach the propane conversion label (in the conversion kit bag) next to the
heater rating plate.
Attach the LPG warning label (in the conversion kit bag) to the appliance casing, next to
the gas inlet pipework.
10.
Replace the top and front access covers.
FIGURE 14.4
CONVERSION PROCEDURE EKW145CE (FROM SERIAL NUMBER L09H10120786)