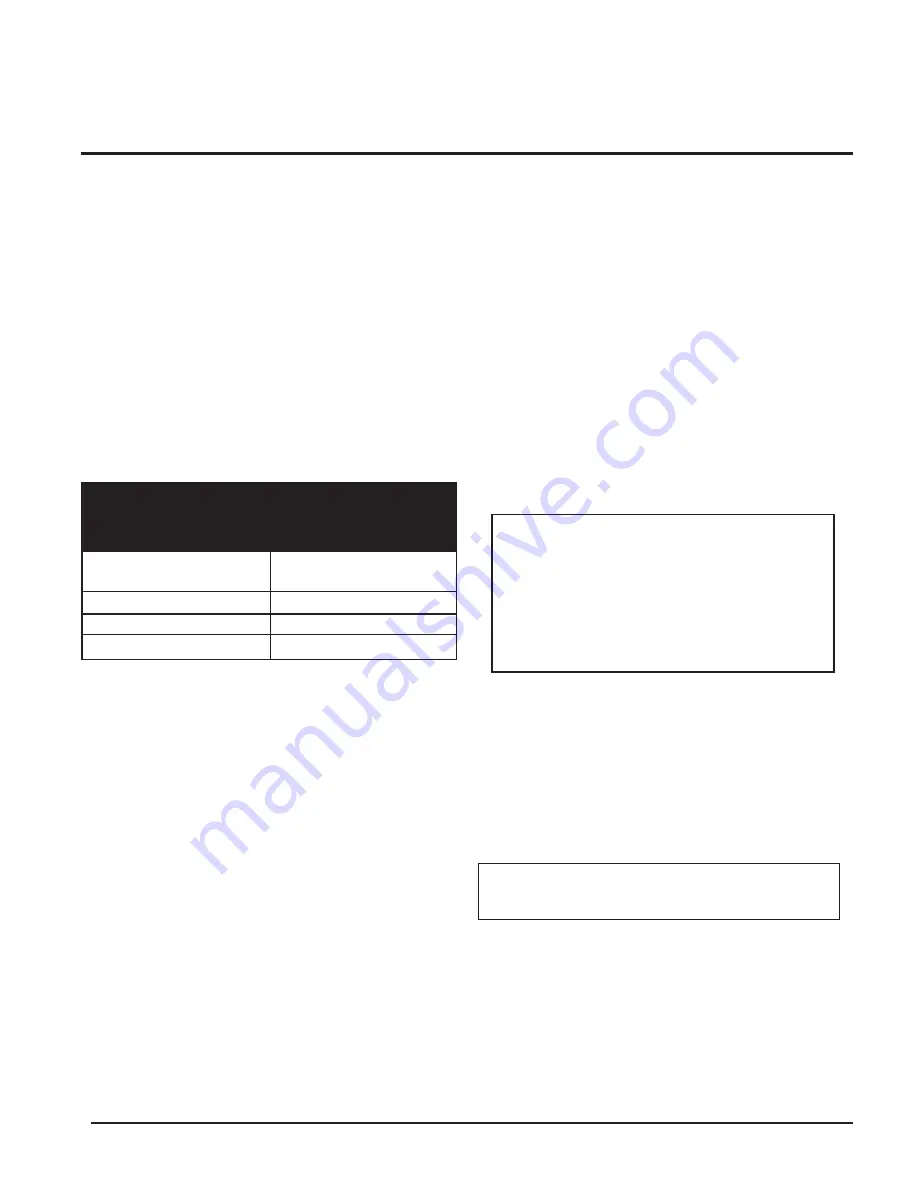
Installation and
Service Manual
7
Base for Combustible Floors
There are no manufactured combustible floor base kits
available for
990,000 - 2,070,000
Btu models. See Table-A
below for floor base kits that are available.
You must construct a base for combustible floor installation.
Install unit over a base of hollow clay tiles or concrete blocks
from 8" to 12" thick and extending at least 24" beyond the unit
sides. Place tiles or blocks so that the holes line up horizontally
to provide a clear passage through the tiles or blocks. Place a
1/2" fireproof millboard over the top of the tile or block base.
Place a 20-gauge sheet metal cover over the fireproof
millboard. Center the unit on the base. Also follow this
procedure if electrical conduit runs through the floor beneath
the unit. This base must meet all local fire and safety codes.
FREEZE PROTECTION
Although these units are CSA International design certified for
outdoor installations, such installations are not recommended
in areas where the danger of freezing exists. You must provide
proper freeze protection for outdoor installations, units
installed in unheated mechanical rooms or where temperatures
may drop to the freezing point or lower. If freeze protection is
not provided for the system, a low ambient temperature alarm
is recommended for the mechanical room. Damage to the unit
by freezing is non-warrantable.
Anytime the temperature measured at any of the sensors
(except the outside air temperature sensor) drops below 35°F
(2°C), the control turns on the pump contact and the alarm
relay. The screen displays an error message (EO2).
Pump Operation
This unit is equipped with a pump delay feature as standard.
The delay is selectable through the temperature controller. As
shipped from the factory, the
Δ
T
MIN
is set to “OFF”, which
creates a 30 second pump delay at the end of a Call for Heat.
The value of
Δ
T
MIN
can be changed to a value between 1°F
and 20°F. This will cause the unit to continue pump operation
until the
Δ
T is less than the value selected (30 second
minimum).
A value of “ON” is selectable through the control for
Δ
T
MIN
.
This will operate the pump continuously. Alternatively, the
pump can be powered by a separate circuit for continuous
operation.
Note:
Pump relay is rated for 1 HP maximum.
Location
Locate indoor boilers and hot water supply boilers in a room
having a temperature safely above freezing [32°F (0°C)].
Hydronic System Antifreeze
Freeze protection for a heating boiler or hot water supply
boiler using an indirect coil can be provided by using hydronic
system antifreeze. Follow the appliance manufacturers
instructions. Do not use undiluted or automotive type
antifreeze.
Outdoor Boiler Installation
Adequate hydronic system antifreeze must be used. A snow
screen should be installed to prevent snow and ice
accumulation around the unit or its venting system.
WARNING
: Do not use antifreeze in
domestic water heater applications.
CAUTION
: A mechanical room
operating under a negative pressure may
experience a down draft in the flue of a
boiler which is not firing. The cold outside
air pulled down the flue may freeze a heat
exchanger. This condition must be
corrected to provide adequate freeze
protection.
399,999
CFK3301
500,000
CFK3302
650,000
CFK3303
750,000
CFK3304
TABLE - A
COMBUSTIBLE FLOOR KITS
Input Btu/hr
Kit Number