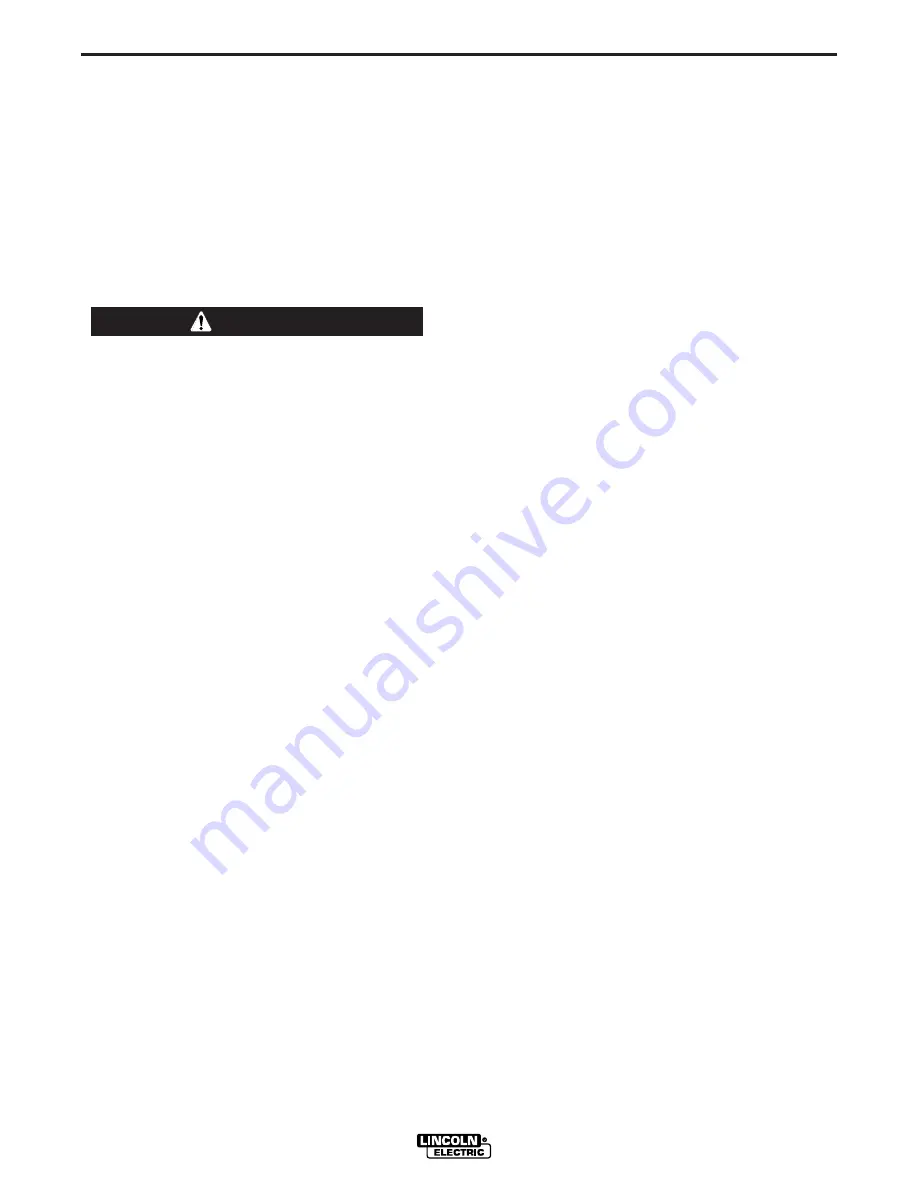
B-5
OPERATION
B-5
NOMINAL PROCEDURES
The Power Wave is designed to operate with 3/4"
electrode stick-out for CV and Pulse processes and a
1/2" stick-out for STT processes.
FRINGE PROCEDURES
Excessively short or long electrode stick-outs may
function only on a limited basis, if at all.
MAKING A WELD
The serviceability of a product or structure utiliz-
ing the welding programs is and must be the sole
responsibility of the builder/user. Many variables
beyond the control of The Lincoln Electric
Company affect the results obtained in applying
these programs. These variables include, but are
not limited to, welding procedure, plate chemistry
and temperature, weldment design, fabrication
methods and service requirements. The available
range of a welding program may not be suitable
for all applications, and the build/user is and must
be solely responsible for welding program selec-
tion.
-----------------------------------------------------------------------
The steps for operating the Power Wave will vary
depending upon the options installed in the user inter-
face (control box) of the welding system. The flexibility
of the Power Wave system lets the user customize
operation for the best performance.
First, consider the desired welding process and the
part to be welded. Choose an electrode material,
diameter, shielding gas and process (GMAW, GMAW-
P, GMAW-STT, etc.)
Second, find the program in the welding software that
best matches the desired welding process. The stan-
dard software shipped with the Power Waves encom-
passes a wide range of common processes and will
meet most needs. If a special welding program is
desired, contact the local Lincoln Electric sales repre-
sentative.
To make a weld, the Power Wave needs to know the
desired welding parameters. The Power Feed (PF)
family of feeders communicate settings to the Power
Wave through control cable connection. Arc length,
wire feed speed, arc control, etc. are all communicat-
ed digitally via the control cable.
WELDING ADJUSTMENTS
All adjustments are made on the system component
known as the User Interface (Control Box), which con-
tains the switches, knobs, and digital displays neces-
sary to control both the Power Wave and a Power
Feed wire feeder. Typically, the Control Box is sup-
plied as part of the wire feeder. It can be mounted
directly on the wire feeder itself, the front of the power
source, or mounted separately, as might be done in a
welding boom installation.
Because the Control Box can be configured with many
different options, your system may not have all of the
following adjustments. Regardless of availability, all
controls are described below. For further information,
consult the Power Feed wire feeder instruction manu-
al.
•
WFS / AMPS
:
In synergic welding modes (synergic CV, pulse
GMAW, STT) WFS (wire feed speed) is the dominant
control parameter, controlling all other variables. The
user adjusts WFS according to factors such as weld
size, penetration requirements, heat input, etc. The
Power Wave then uses the WFS setting to adjust its
output characteristics (output voltage, output current)
according to pre-programmed settings contained in
the Power Wave. In non-synergic modes, the WFS
control behaves more like a conventional CV power
source where WFS and voltage are independent
adjustments. Therefore to maintain the arc character-
istics, the operator must adjust the voltage to compen-
sate for any changes made to the WFS.
In constant current modes (stick, TIG) this control
adjusts the output current, in amps.
POWER WAVE 455/STT
WARNING
Содержание POWER WAVE 455/STT
Страница 43: ...NOTES POWER WAVE 455 STT...